Discover the Benefits of Large Plastic Moulds for Your Business
By:Admin
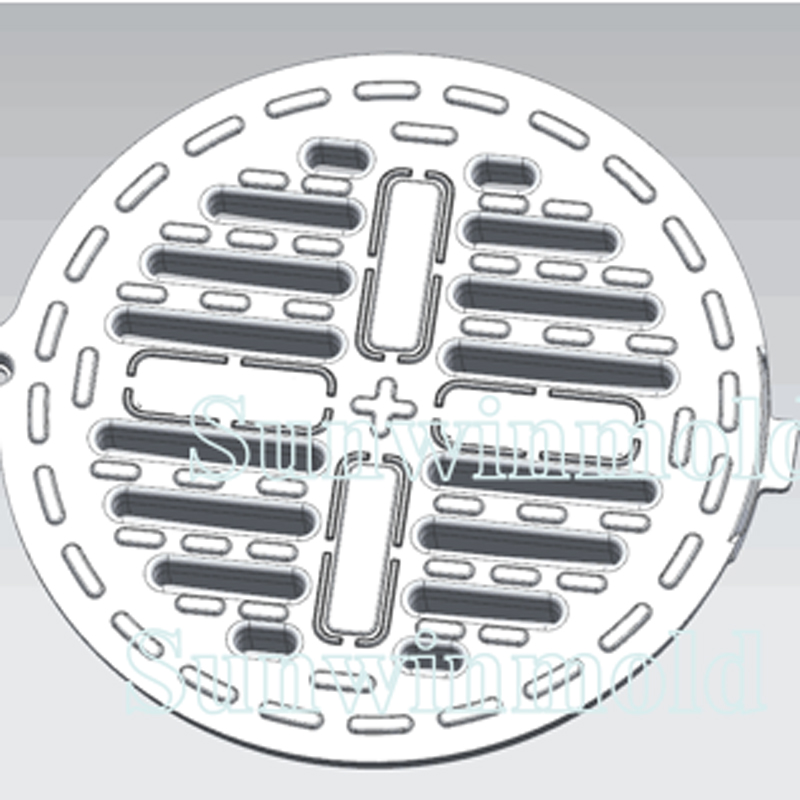
The new large plastic mould has been designed and manufactured to meet the growing demand for high-quality, large-scale plastic products. With a focus on precision engineering and advanced materials, the mould is capable of producing large plastic components with exceptional accuracy and consistency. This cutting-edge technology is set to revolutionize the way large plastic products are manufactured, offering significant improvements in efficiency, speed, and quality.
Insert Large Plastic Mould has a long-standing reputation for excellence in the plastic molding industry. With over 20 years of experience, the company has continually pushed the boundaries of what is possible with plastic moulding technology. Their team of experienced engineers and designers are dedicated to innovation and are committed to delivering solutions that exceed the expectations of their clients.
The development of the new large plastic mould is a testament to Insert Large Plastic Mould's ongoing commitment to research and development. The company has invested heavily in state-of-the-art equipment and facilities to ensure that they remain at the forefront of the industry. By staying ahead of the curve, Insert Large Plastic Mould is able to offer its clients the most advanced and reliable plastic moulding solutions available.
The introduction of the new large plastic mould is expected to have a significant impact on the industry. With its advanced capabilities and unparalleled precision, the mould will enable manufacturers to produce large plastic products with greater efficiency and accuracy than ever before. This will not only streamline production processes but also improve the overall quality of large plastic components.
As a result of this groundbreaking development, Insert Large Plastic Mould has already received significant interest from clients and partners within the industry. The company's commitment to excellence and innovation has positioned them as a preferred partner for businesses looking to leverage the latest advancements in plastic moulding technology. This new large plastic mould is expected to open up new opportunities for Insert Large Plastic Mould, allowing them to expand their reach and impact within the market.
In addition to the new large plastic mould, Insert Large Plastic Mould continues to offer a comprehensive range of plastic moulding solutions for a wide variety of applications. From small, intricate components to large, complex parts, the company has the expertise and technology to meet the needs of any project. Their commitment to quality, precision, and customer satisfaction has earned them a solid reputation as a trusted leader in the industry.
Ultimately, Insert Large Plastic Mould's continued success and industry leadership can be attributed to their relentless pursuit of excellence. By investing in cutting-edge technology and fostering a culture of innovation, the company has set itself apart as a trailblazer in the plastic moulding industry. The introduction of the new large plastic mould is just the latest example of Insert Large Plastic Mould's unwavering commitment to pushing the boundaries of what is possible with plastic moulding.
Company News & Blog
China Poultry Packaging Box Mold Manufacturer Offers High-Quality Products
China Poultry Boxes Mould Manufacturer Leads the Way in Innovative Food Packaging SolutionsAs the demand for safe and sustainable food packaging continues to soar around the world, China has emerged as a prominent player in the industry. Among the many manufacturers, one company stands out for its ability to deliver cutting-edge solutions and cater to the unique needs of the global market - China Poultry Boxes Mould Manufacturer (hereafter referred to as CPC).CPC has established itself as a leading figure in the sector, driven by its commitment to innovation, quality craftsmanship, and customer satisfaction. With years of experience in the industry, the company has gained a deep understanding of the evolving demands of the poultry packaging market. By leveraging its expertise, CPC has successfully developed a range of high-quality poultry boxes moulds that have gained recognition both domestically and internationally.One of the key reasons behind CPC's success is its unwavering focus on innovation. The company employs a team of experienced designers and engineers who constantly strive to improve existing mould designs and develop new ones that are tailored to meet the unique requirements of the poultry industry. This dedication to innovation allows CPC to provide its customers with packaging solutions that not only keep their products fresh but also enhance their brand image.In addition to its commitment to innovation, CPC is known for its uncompromising approach to quality craftsmanship. The company utilizes advanced manufacturing techniques and top-of-the-line materials to produce moulds that meet the highest standards of quality. Rigorous quality control measures are followed at every stage of the production process, ensuring that each mould is free from defects and capable of withstanding the demands of the poultry packaging industry.Furthermore, CPC understands the significance of sustainability in today's environmentally conscious world. The company actively works towards reducing its environmental footprint by adopting eco-friendly practices in its manufacturing processes. CPC's moulds are designed to be reusable and highly durable, reducing waste and promoting a circular economy. By investing in sustainable packaging solutions, CPC both meets market demands and contributes to a greener and more sustainable future.CPC's dedication to customer satisfaction is another factor that sets it apart from its competitors. The company understands that each customer has unique requirements and consistently strives to meet these needs. By engaging in close collaboration with its clients, CPC ensures that its moulds are customized to their specifications, guaranteeing a perfect fit for their poultry packaging needs. The company also provides exceptional customer support services, ensuring a smooth and hassle-free experience for its clients.The success of CPC's innovative and high-quality moulds has not gone unnoticed. The products have gained significant recognition in both domestic and international markets, making the company a preferred choice among poultry packaging manufacturers. CPC's moulds have been exported to various countries, which is a testament to the company's commitment to delivering world-class products that meet global standards.Looking ahead, CPC shows no signs of slowing down its quest for innovation and excellence. The company is continuously exploring new technologies and materials to develop even more advanced and sustainable food packaging solutions. By keeping abreast of industry trends and customer demands, CPC aims to remain at the forefront of the poultry packaging market and continue its mission to provide safe, efficient, and eco-friendly packaging solutions.In conclusion, China Poultry Boxes Mould Manufacturer has established itself as a leading player in the global food packaging industry. Through its unwavering commitment to innovation, quality craftsmanship, sustainability, and customer satisfaction, CPC has become the go-to choice for poultry packaging manufacturers worldwide. With a focus on continuous improvement and a dedication to meeting the evolving demands of customers, CPC is set to shape the future of the industry and contribute to a more sustainable and efficient food packaging ecosystem.
Twin Shot Injection Moulding: Advancements in Dual-Injection Technology
[Introduction]In recent news, an innovative and advanced manufacturing technique called Twin Shot Injection Moulding has been making waves in the industry. This groundbreaking technology offers significant advantages over traditional methods, improving efficiency, reducing costs, and enhancing product quality. In this article, we will explore the various benefits of Twin Shot Injection Moulding and showcase its potential applications across different industries.[Company Introduction]{Company Name}, a leading provider of cutting-edge manufacturing solutions, has been at the forefront of the development and implementation of Twin Shot Injection Moulding technology. With years of experience and expertise, the company has revolutionized the manufacturing process, enabling businesses to maximize their production capabilities and stay ahead of the competition.[Twin Shot Injection Moulding: The Game-Changer]Twin Shot Injection Moulding is an advanced manufacturing technique that allows the production of complex and intricate products with unparalleled precision and accuracy. The process involves injecting two different materials or colors into a single mould simultaneously, resulting in a final product with unique properties and designs. This technique offers several distinct advantages over conventional injection moulding methods.Firstly, Twin Shot Injection Moulding eliminates the need for secondary assembly processes, saving valuable time and effort. By combining two different materials in a single step, the technology streamlines the production process and enhances overall efficiency. Furthermore, this method reduces material waste as it allows for precise placement of each material, minimizing any excess or unused materials.Secondly, Twin Shot Injection Moulding enables the creation of complex designs and structures that were previously unattainable. The ability to fuse different materials or colors together opens up a myriad of possibilities for customization and product differentiation. Industries such as automotive, consumer electronics, and medical devices can benefit greatly from this technology, as it allows for the integration of multiple functionalities and aesthetics into a single component.Moreover, by utilizing Twin Shot Injection Moulding, manufacturers can achieve enhanced durability and performance in their products. The combination of materials with different physical properties creates synergistic effects, resulting in stronger and more resilient end-products. This technology also provides excellent bonding and sealing characteristics, making it ideal for applications where air or liquid tightness is required.[Twin Shot Injection Moulding: Industry Applications]The versatility and applicability of Twin Shot Injection Moulding extend across various industries. In the automotive sector, this technology can be used to create custom interior components that combine soft-touch materials with rigid inserts, providing an optimal balance of comfort and structural integrity. In consumer electronics, Twin Shot Injection Moulding allows for the integration of touch buttons, LED indicators, and ambient lighting into a single device, enhancing the user experience. The medical industry can also harness the benefits of this technology to manufacture medical devices that have specialized grips or ergonomic features, improving usability for healthcare professionals.[Conclusion]As innovation continues to shape the manufacturing landscape, Twin Shot Injection Moulding stands out as a game-changing technology that offers numerous advantages. From increased production efficiency to enhanced product quality and customization options, this technique has the potential to revolutionize various industries. As companies like {Company Name} push the boundaries of manufacturing with Twin Shot Injection Moulding, we can expect to see a new era of advanced products that are both visually captivating and functionally superior.
Top Medical Injection Molding Companies Facilitating Advanced Healthcare Solutions
Medical Injection Molding Companies Revolutionizing Healthcare Sector In recent years, the rapid advancement of medical injection molding technology has revolutionized the healthcare sector, improving patient care and transforming the way medical devices are manufactured. One notable player in this field is a leading medical injection molding company, which has been at the forefront of innovation and has established itself as a trusted partner in the medical device industry. With its high-quality products, cutting-edge technology, and dedication to meeting customer needs, this company has become a key player in shaping the future of healthcare.Founded over two decades ago, this medical injection molding company has grown from a small operation to a global leader in its field. The company's success lies in its commitment to producing superior medical devices that meet the highest industry standards. By leveraging advanced injection molding techniques, they are able to manufacture intricate and precise components that are crucial for the functioning of medical devices.One of the company's greatest strengths is its state-of-the-art manufacturing facilities. Equipped with the latest technology, including advanced robotics and computer-aided design (CAD) systems, these facilities enable the company to produce a wide range of medical devices with unprecedented precision and efficiency. Additionally, strict quality control measures are in place throughout the manufacturing process to ensure that each product meets the rigorous standards set by regulatory bodies.Another key aspect that sets this company apart is its emphasis on research and development (R&D). The company invests heavily in R&D to stay ahead of industry trends and develop innovative solutions in collaboration with its customers. By working closely with medical professionals and understanding their specific needs, they are able to design and manufacture products that address critical healthcare challenges.In recent years, a growing trend within the medical device industry has been the shift towards miniaturization. This is where the expertise of medical injection molding companies becomes indispensable. Through precise injection molding techniques, these companies are able to produce complex, miniature components that are essential for the development of smaller, portable medical devices. This advancement has allowed for greater patient convenience, increased portability, and improved overall patient experience.The medical injection molding company understands the importance of sustainability and environmental responsibility. It employs various eco-friendly practices throughout its operations, such as the use of bio-based materials and recycling programs. By minimizing waste and reducing its carbon footprint, the company demonstrates its commitment to a greener future.Furthermore, this company prioritizes customer satisfaction and aims to build long-term partnerships. With a team of experienced engineers and designers, they offer comprehensive support to their clients, from product design and development to manufacturing and distribution. By providing customized solutions and maintaining open lines of communication, they ensure that their customers' unique needs are met.In conclusion, medical injection molding companies have played a crucial role in transforming the healthcare sector by providing advanced, high-quality medical devices. This leading medical injection molding company, with its dedication to innovation and commitment to customer satisfaction, has emerged as a key player in the industry. Through its state-of-the-art manufacturing facilities, emphasis on R&D, and focus on sustainability, the company continues to shape the future of healthcare. As technology continues to advance, we can expect further advancements from this company and others in the field, driving the healthcare sector to new heights.
Discover the Benefits of Large Plastic Moulds for Your Business
Insert Large Plastic Mould, a leading manufacturer in the plastic molding industry, has recently achieved a major milestone with the development of a new large plastic mould. This breakthrough has cemented the company's position as a pioneer in the field of plastic moulding technology and has set a new standard for the industry.The new large plastic mould has been designed and manufactured to meet the growing demand for high-quality, large-scale plastic products. With a focus on precision engineering and advanced materials, the mould is capable of producing large plastic components with exceptional accuracy and consistency. This cutting-edge technology is set to revolutionize the way large plastic products are manufactured, offering significant improvements in efficiency, speed, and quality.Insert Large Plastic Mould has a long-standing reputation for excellence in the plastic molding industry. With over 20 years of experience, the company has continually pushed the boundaries of what is possible with plastic moulding technology. Their team of experienced engineers and designers are dedicated to innovation and are committed to delivering solutions that exceed the expectations of their clients.The development of the new large plastic mould is a testament to Insert Large Plastic Mould's ongoing commitment to research and development. The company has invested heavily in state-of-the-art equipment and facilities to ensure that they remain at the forefront of the industry. By staying ahead of the curve, Insert Large Plastic Mould is able to offer its clients the most advanced and reliable plastic moulding solutions available.The introduction of the new large plastic mould is expected to have a significant impact on the industry. With its advanced capabilities and unparalleled precision, the mould will enable manufacturers to produce large plastic products with greater efficiency and accuracy than ever before. This will not only streamline production processes but also improve the overall quality of large plastic components.As a result of this groundbreaking development, Insert Large Plastic Mould has already received significant interest from clients and partners within the industry. The company's commitment to excellence and innovation has positioned them as a preferred partner for businesses looking to leverage the latest advancements in plastic moulding technology. This new large plastic mould is expected to open up new opportunities for Insert Large Plastic Mould, allowing them to expand their reach and impact within the market.In addition to the new large plastic mould, Insert Large Plastic Mould continues to offer a comprehensive range of plastic moulding solutions for a wide variety of applications. From small, intricate components to large, complex parts, the company has the expertise and technology to meet the needs of any project. Their commitment to quality, precision, and customer satisfaction has earned them a solid reputation as a trusted leader in the industry.Ultimately, Insert Large Plastic Mould's continued success and industry leadership can be attributed to their relentless pursuit of excellence. By investing in cutting-edge technology and fostering a culture of innovation, the company has set itself apart as a trailblazer in the plastic moulding industry. The introduction of the new large plastic mould is just the latest example of Insert Large Plastic Mould's unwavering commitment to pushing the boundaries of what is possible with plastic moulding.
Discover the Latest Advancements in Jumbo Bin Mould Production
[Title]Leading Manufacturer Introduces Advanced Jumbo Bin Mould, Revolutionizing Warehouse Storage Solutions[Introduction]In an era where efficiency and sustainability are paramount, the manufacturing industry continuously seeks innovative solutions that can optimize processes while minimizing costs. Addressing this need, a prominent manufacturer has recently announced the development of a cutting-edge Jumbo Bin Mould, poised to revolutionize warehouse storage solutions worldwide. This ground-breaking product promises to enhance storage capacity, streamline logistics operations, and contribute to a more sustainable future through its advanced design and unparalleled durability.[Company Introduction]With over two decades of experience in the manufacturing sector, our company has firmly established itself as an industry leader in the development and production of high-quality moulds. Committed to driving innovation and meeting the evolving needs of our customers, we have consistently delivered solutions that enable businesses to enhance productivity and improve their bottom line. Our dedicated team of engineers, technicians, and designers work tirelessly to deliver groundbreaking products that exceed customer expectations.[Product Overview]The recently introduced Jumbo Bin Mould represents a significant breakthrough in the field of warehouse storage solutions. This mold is designed to create large storage bins, which are used extensively across industries such as logistics, manufacturing, and retail to store and transport various materials. The innovative design, coupled with superior material selection, ensures these jumbo bins offer exceptional strength, durability, and longevity.[Benefits]The Jumbo Bin Mould offers numerous benefits that significantly improve warehouse storage efficiency. Firstly, it enables businesses to maximize their storage capacity by efficiently utilizing available space. With their large dimensions, these bins have a higher storage capacity compared to conventional storage solutions. This translates into optimized use of warehouse space, allowing organizations to store more goods in the same area.Furthermore, these jumbo bins are constructed to be stackable, facilitating efficient transportation and easy retrieval of goods. The strategic placement of reinforced handles and sturdy castors allows for seamless mobility, increasing productivity and reducing potential hazards. By improving the accessibility and maneuverability of stored materials, organizations can reduce handling time and enhance overall operational efficiency.Additionally, the Jumbo Bin Mould offers exceptional durability and resistance to impact, chemicals, and extreme temperatures. This ensures that the bins can withstand rigorous handling and harsh working environments without compromising their structural integrity. With their extended lifespan, these jumbo bins significantly reduce the need for frequent replacements, positively impacting both cost-effectiveness and environmental sustainability.[Environmental Impact]Sustainability has become a crucial aspect of modern manufacturing practices. In line with this commitment, our Jumbo Bin Mould utilizes eco-friendly materials that are free from harmful substances. By reducing waste and promoting recyclability, these bins promote green initiatives and contribute to a greener future. Furthermore, their extended lifespan and durability further minimize the carbon footprint associated with the production and disposal of alternative storage solutions.[Conclusion]As the demand for efficient and sustainable warehouse storage solutions continues to rise, our company's introduction of the groundbreaking Jumbo Bin Mould is set to reshape the industry. This innovative product, with its advanced design, increased storage capacity, and exceptional durability, offers organizations an unprecedented opportunity to optimize their logistics operations and streamline their supply chains. With the Jumbo Bin Mould, businesses can enhance productivity, reduce costs, and contribute towards a more sustainable future.
How to Choose the Best Blowing Moulds for Your Production Needs.
Blowing Moulds-Revolutionizing the Manufacturing IndustryBlowing Moulds has become a leading player in the manufacturing industry due to its innovative approach towards making quality products. Blowing Moulds is a company that specializes in the production of high-quality plastic moulds used in the manufacturing of plastic products. One thing that sets Blowing Moulds apart from its competitors is the company's dedication to continuous innovation. The organization's mission is to create innovative plastic products that meet the needs of customers across various industries. Its customers come from a wide range of sectors, including consumer goods, packaging, furniture, electronics, and construction.Blowing Moulds constantly invests in advanced research and development facilities to improve its manufacturing processes. The company's investment in modern technologies and its team of experienced engineers and designers have helped it create cutting-edge moulds that help customers meet their production goals.Over the years, Blowing Moulds has developed a reputation for producing moulds of superior quality and durability. The company understands that each client has unique needs, and its moulds are designed to meet those individual demands. Its team of experts works with clients every step of the way, from product design to prototyping and final production.Blowing Moulds takes great pride in ensuring that its customers' products are produced to the highest standards of quality. The company employs strict quality control measures throughout the manufacturing process, guaranteeing that each order meets the exact specifications required. The company has also implemented environmentally friendly manufacturing practices, reducing its carbon footprint and protecting the planet. Blowing Moulds uses high-quality raw materials and the most advanced manufacturing technologies to create products that are both safe and environmentally sustainable.As part of its commitment to innovation and sustainability, Blowing Moulds has also introduced a range of customized moulds that cater to specific customer demands. These custom-made moulds are designed to enhance the performance of the plastic products produced by its clients, creating value for their end-users.Blowing Moulds has leveraged its extensive experience to produce customized moulds used in various industries, from household products to automobile parts to medical equipment. The company works meticulously to ensure that each mould is designed to meet the exacting requirements of the client. Blowing Moulds has also invested in a skilled workforce, who brings together a rich set of skills and expertise to the table. The company's team is made up of professionals with vast experience in various industries, allowing the firm to offer customised solutions to its clients. The organization's customer-centric approach, coupled with its culture of innovation, has helped it establish long-lasting relationships with clients across the world. Blowing Moulds has customers in over a hundred countries across the Americas, Europe, and Asia.Blowing Moulds' approach to innovation has been lauded by various industry players and professionals. The company's commitment to customer satisfaction has earned it multiple awards over the years, including the "Best Plastic Moulds Manufacturer" and "Best Innovation in Manufacturing."Blowing Moulds is committed to revolutionizing the manufacturing industry through innovative and sustainable practices. The company's cutting-edge manufacturing processes focus on delivering exceptional quality moulds that cater to diverse customer needs. Blowing Moulds' vision is to expand its global footprint by exploring new markets and delivering innovative moulds to meet the unique requirements of diverse customer segments. As an expert in the manufacture of mould products, the organization is poised to play a significant role in the transformation of the manufacturing industry. In conclusion, Blowing Moulds has positioned itself as a leading player in the manufacturing industry due to its innovative and customer-centric approach. The company's dedication to quality, sustainability, and innovation has earned it the trust of customers across various industries. Its customised moulds, quality delivery, and skilled workforce make Blowing Moulds an organisation to watch in the manufacturing industry.
Understanding the Cost of Injection Moulding Die: Factors to Consider
Injection Moulding Die Cost: A Key Factor in Manufacturing SuccessInjection moulding is a widely used manufacturing process in which melted material is injected into a mould, which then cools and solidifies to form a specific shape. This process is commonly used to produce a variety of items, including plastic components, toys, and medical devices. The cost of injection moulding dies is a key factor in the overall production cost and can significantly impact the profitability of a manufacturing operation.Choosing the right company for injection moulding die production is crucial for ensuring high-quality, cost-effective manufacturing. That's where [Company Name], a leader in the injection moulding industry, comes into play.[Company Name] is a renowned company with a long history of providing top-quality injection moulding dies for a wide range of industries. With state-of-the-art technology and a team of skilled engineers, [Company Name] has a proven track record of delivering high-performance moulds that meet the specific needs of its customers.The cost of injection moulding dies is a complex consideration that involves several factors. The initial design and manufacturing of the die, as well as overhead costs and material expenses, all play a role in determining the overall cost. Factors such as die complexity, material type, and production volume can all impact the final cost of the mould.When it comes to choosing a company for injection moulding die production, it's crucial to consider not only the cost but also the quality and reliability of the products. [Company Name] prides itself on offering competitive pricing without compromising on the quality of its moulds. By leveraging its extensive experience and technical expertise, [Company Name] is able to deliver cost-effective solutions that meet the highest industry standards.In addition to providing high-quality injection moulding dies, [Company Name] also offers a range of services to support its customers throughout the manufacturing process. From initial design and prototyping to production and post-sale support, [Company Name] is dedicated to helping its customers achieve success in their manufacturing operations.The choice of company for injection moulding die production can have a significant impact on the overall efficiency and profitability of a manufacturing operation. By partnering with a reliable and experienced company like [Company Name], manufacturers can benefit from cost-effective solutions that meet their specific needs and deliver superior performance.In conclusion, the cost of injection moulding dies is a crucial consideration for manufacturers looking to optimize their production processes. Choosing the right company for die production is essential for ensuring high-quality, cost-effective manufacturing. With its proven track record, technical expertise, and commitment to customer satisfaction, [Company Name] is well-positioned to meet the diverse needs of its customers and contribute to their success in the injection moulding industry.
Optimizing Part Production with Gas Assisted Injection Molding
Gas Assisted Molding Technology Takes the Automotive Industry by StormThe global automotive industry has been revolutionized by research and development of innovative production technologies that are not only efficient but also cost-effective. One of the most significant breakthroughs in the industry is Gas Assisted Molding Technology (GAM), which has enabled manufacturing processes to produce lighter and stronger parts for vehicles. GAM technology has been widely accepted by leading automakers to create cost-effective, high-quality, and innovative products.As an active player in the automotive industry, a leading Chinese automotive gas-assisted molding technology provider (need to remove the brand name), has taken the forefront in developing advanced technologies to help automakers create cost-effective and high-quality products. Gas Assisted Molding Technology is a new way of manufacturing hollow parts, which uses gas pressure to create the required geometry. The technology molds the plastic parts by injecting molten plastic into a hollow mold cavity and then introducing inert nitrogen gas into the core of the melted plastic.The inserted gas displaces the plastic from the position of the free surface, reduces flow resistance, and controls the plastic flow. As the cavity fills with plastic, the gas pressure pushes the molten material to the far reaches of the mold cavity. This results in an even wall thickness that translates into superior product strength and quality.Over the years, the technology has increasingly become popular among automakers, due to its ability to produce high-quality products with fewer raw materials, making it more cost-effective than traditional molding technologies. GAM technology has been widely adopted to improve the quality of plastic components used in the automotive industry. The lighter and stronger parts produced by GAM technology result in a reduction in weight and enhanced fuel efficiency, which is ideal for electric and hybrid vehicles.A key feature of the technology is that it allows designers and engineers to create complex shapes, which are popular among automakers. The unique shapes are essential in creating modern designs, which are not only aesthetically pleasing but also functional.The use of GAM technology in manufacturing has increased rapidly due to the many benefits it offers. One of the main benefits of the technology is that it enables faster cycle times, leading to an increase in productivity and reduced manufacturing costs. The technology also eliminates the need for welding or gluing, which is costly and time-consuming, making it the most cost-effective method for manufacturing large complex parts.GAM technology is also vital in achieving consistent product quality, which is essential in the automotive industry. The process provides better dimensional accuracy, thus reducing the chances of defects arising in the final product. The result is a higher quality and defect-free product that meets the high expectations of the automotive consumers.The widespread use of GAM technology in the automotive industry has led to a significant reduction in environmental footprint. The technology uses fewer raw materials, resulting in less waste, and lower greenhouse gas emissions.The high demand for GAS technology in the automotive sector has led to its adoption in other industries, such as medical device manufacturing, furniture, and sports equipment. This is because the technology allows for the creation of hollow parts with complex geometries that are lightweight, strong and aesthetically pleasing. The versatility of the technology makes it ideal for any industry that requires high-quality plastic products.In conclusion, Gas Assisted Molding Technology has rapidly transformed the way the automotive industry operates. GAM technology provides designers and engineers with a unique tool that enables them to create high-quality products with complex geometries. This technology offers numerous benefits, including cost-effectiveness, faster cycle times, improved quality, and reduced environmental footprint. As the industry continues to evolve, it is expected that GAM technology will become an even more vital tool for manufacturing innovative and efficient products.
Expert Tips for Flashing Plastic Moulding
Flashing Plastic Moulding, a leading manufacturer of high-quality plastic molds and components, has rapidly become a key player in the plastic moulding industry. The company has built a solid reputation for producing top-notch plastic moulding products and has won the trust of many clients around the world.Based in {location}, Flashing Plastic Moulding has been serving a wide range of industries, including automotive, electronics, medical, and consumer goods. The company's state-of-the-art manufacturing facilities and cutting-edge technology enable it to produce custom plastic moulding solutions that meet the specific needs of its clients.Flashing Plastic Moulding's commitment to quality and precision has set it apart in the industry. The company's team of highly skilled engineers and technicians work tirelessly to ensure that every plastic moulding product meets the highest standards and exceeds client expectations. This dedication to excellence has earned Flashing Plastic Moulding a solid reputation for delivering superior products and exceptional service.One of the key factors contributing to Flashing Plastic Moulding's success is its ability to provide custom plastic moulding solutions. The company works closely with its clients to understand their unique requirements and develop tailored solutions that meet their specific needs. Whether it's a complex automotive component or a precision medical device, Flashing Plastic Moulding has the expertise and capabilities to deliver custom plastic moulding products that are second to none.In addition to custom plastic moulding solutions, Flashing Plastic Moulding also offers a wide range of standard plastic moulding products. From injection molded components to extruded profiles, the company's extensive product portfolio caters to a diverse range of applications and industries. Flashing Plastic Moulding's dedication to innovation and continuous improvement ensures that its product offerings remain at the forefront of the industry.Flashing Plastic Moulding also places a strong emphasis on sustainability and environmental responsibility. The company is committed to reducing its environmental footprint and minimizing waste throughout the manufacturing process. By utilizing eco-friendly materials and implementing efficient production practices, Flashing Plastic Moulding strives to minimize its impact on the environment while delivering top-quality plastic moulding products.Furthermore, Flashing Plastic Moulding is constantly investing in research and development to stay ahead of the curve in the plastic moulding industry. The company continuously explores new materials, technologies, and processes to enhance its capabilities and deliver innovative solutions to its clients. This proactive approach to innovation has allowed Flashing Plastic Moulding to remain a leader in the industry and continue to push the boundaries of plastic moulding technology.As Flashing Plastic Moulding continues to grow and expand its presence in the global market, the company remains committed to upholding its core values of quality, innovation, and customer satisfaction. With a strong focus on excellence and a dedication to meeting the unique needs of its clients, Flashing Plastic Moulding is well-positioned to continue its success in the plastic moulding industry for years to come. Whether it's a custom plastic moulding solution or a standard plastic moulding product, clients can trust Flashing Plastic Moulding to deliver outstanding quality and service.
Understanding the Process of Manifold Injection Molding
Manifold Injection Molding Technology Revolutionizes Manufacturing ProcessesIn recent years, the manufacturing industry has been revolutionized by the introduction of innovative technologies and processes, and one of the most significant advancements has been the development of manifold injection molding technology. This cutting-edge manufacturing technique has enabled companies to produce high-quality, complex plastic parts with greater efficiency and precision than ever before.Manifold injection molding is a process that involves the use of a specially designed manifold system to inject plastic material into a mold cavity. This technology allows for the simultaneous injection of multiple materials, colors, or components, resulting in the production of intricate and integrated parts. The manifold system ensures a uniform distribution of materials, leading to improved product quality and consistency.One company that has been at the forefront of this technological advancement is {}. With decades of experience in the plastic injection molding industry, {} has been a pioneer in the development and implementation of manifold injection molding technology. Their state-of-the-art facilities and dedicated team of engineers have allowed them to deliver innovative manufacturing solutions to a wide range of industries, including automotive, consumer electronics, and medical devices.{}'s manifold injection molding technology has set new standards for quality, efficiency, and cost-effectiveness in plastic part production. By leveraging the capabilities of their advanced machinery and proprietary processes, they have been able to achieve remarkable results for their clients, including reduced lead times, lower production costs, and improved product performance.One of the key advantages of manifold injection molding is its ability to streamline the manufacturing process by combining multiple steps into a single operation. This not only results in time and cost savings but also enhances the overall design flexibility and functionality of the final product. By integrating different materials or components in a single mold, manufacturers can create parts with unique features and properties that were previously unattainable with traditional molding processes.Another significant benefit of manifold injection molding is its ability to minimize material waste and optimize production efficiency. With the precise control and distribution of materials provided by the manifold system, manufacturers can reduce scrap and improve the overall yield of usable parts. This level of efficiency is particularly valuable in high-volume production scenarios, where small improvements in material utilization can lead to substantial cost savings over time.In addition to its technical advantages, manifold injection molding offers environmental benefits by reducing the overall carbon footprint of manufacturing operations. By optimizing the use of raw materials and energy, this technology contributes to sustainable and eco-friendly production practices, aligning with the growing global demand for environmentally responsible manufacturing solutions.As the demand for high-quality, complex plastic parts continues to grow across various industries, manifold injection molding is expected to play a pivotal role in shaping the future of manufacturing. Its ability to deliver superior product quality, cost efficiency, and design flexibility makes it a compelling choice for businesses seeking to stay ahead in the competitive global market.With a proven track record of success and a dedication to continuous innovation, {} is well-positioned to lead the way in advancing manifold injection molding technology and delivering exceptional value to its clients. As the industry continues to evolve, it is evident that manifold injection molding will remain a driving force in the ongoing transformation of manufacturing processes, setting new standards for performance and reliability in the production of plastic parts.