Exploring the Efficiency and Advantages of Plastic Blow Molding
By:Admin
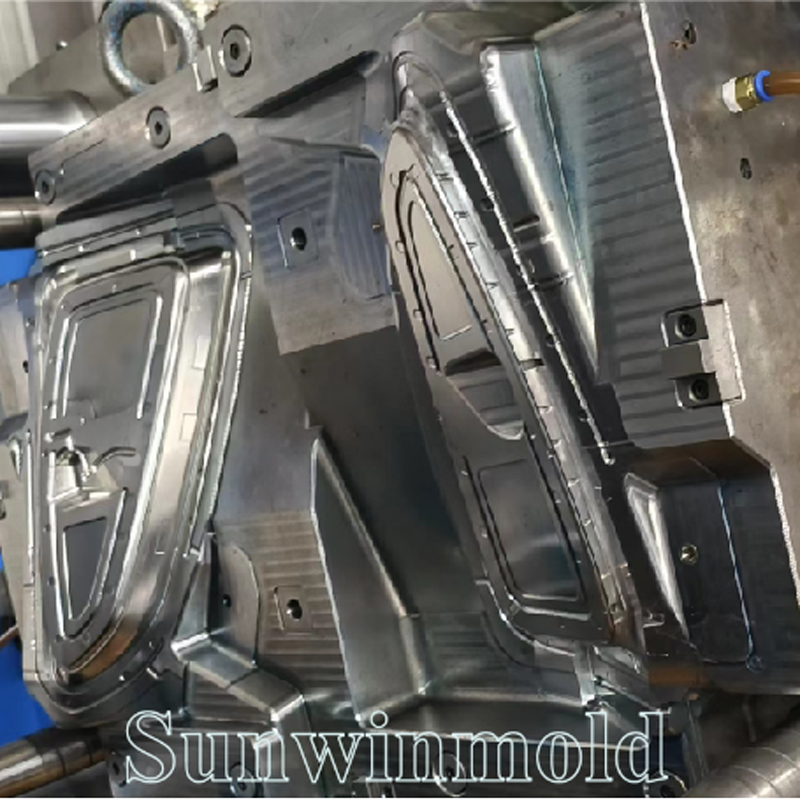
In today’s world, plastic has become an indispensable part of our lives. From disposable water bottles to complex machinery parts, plastic is used in almost every aspect of our daily routine. However, the process of producing high-quality plastic products requires sophisticated techniques and expensive machinery.
This is where Plastic Blow Molding comes in. Plastic blow molding is a manufacturing process that involves the use of blow molding machines to mold plastic into various shapes and sizes. The process is widely used in the production of bottles, containers, and other types of plastic products.
One company that has established itself as a leader in the field of plastic blow molding is a well-known company. The company has been providing high-quality blow-molded products for over 20 years and has become a trusted name in the industry.
The company boasts state-of-the-art facilities and a team of experienced professionals who are dedicated to producing top-quality plastic products. Their advanced machinery allows for the production of various types of plastic products, ranging from small containers to large industrial tanks.
One of the key benefits of plastic blow molding is its versatility. The process allows for the production of complex shapes and designs that would otherwise be impossible to achieve with traditional molding techniques. The end product is strong, durable, and lightweight, making it ideal for use in various industries, including automotive, construction, and packaging.
Moreover, plastic blow molding is an eco-friendly process as it requires minimal energy and produces little to no waste. The process also uses recycled materials, which helps to reduce environmental impact and conserve resources.
Another benefit of plastic blow molding is its cost-effectiveness. The process requires less labor and produces a higher yield than traditional molding techniques, making it a more cost-effective option for businesses.
The company has also implemented strict quality control measures to ensure that every product meets the highest standards. This includes rigorous testing of raw materials, in-process inspection, and final product testing. With a commitment to quality and customer satisfaction, the company has established a loyal customer base and a reputation for excellence.
In addition to providing high-quality products, the company also offers a range of services to its clients. This includes product design and development, prototyping, and custom molding. They work closely with clients to understand their needs and provide customized solutions that meet their requirements.
Overall, plastic blow molding is a highly effective and versatile manufacturing process that has revolutionized the industry. With the help of companies like the one discussed, businesses can take advantage of the benefits of plastic blow molding and produce top-quality plastic products at a reasonable cost.
In conclusion, with advancements in technology and an increasing demand for plastic products, the future of plastic blow molding looks bright. The industry is set to expand in the coming years, and companies like the one discussed will continue to play a crucial role in the growth and development of the industry.
Company News & Blog
Unlocking Efficiency and Precision: Essential Guide to Blow Mold Tooling
Title: Revolutionary Blow Mold Tooling Innovates Manufacturing Process Introduction:In a groundbreaking move toward enhancing the manufacturing industry, an innovative blow mold tooling technique has been introduced by an industry-leading company. With its ability to revolutionize the production process, this cutting-edge technology promises to increase efficiency, reduce costs, and improve the quality of manufacturing across various sectors.Developed by a team of skilled engineers at the forefront of industrial innovation, this blow mold tooling technique is poised to address long-standing challenges and streamline production processes. By removing the limitations of traditional manufacturing methods, this advancement positions companies to meet the ever-increasing demands of the global market.Streamlined Production Process:The Blow Mold Tooling technique simplifies the manufacturing process, allowing companies to significantly reduce production time. By incorporating a sophisticated design, this tooling solution eliminates the need for wasteful intermediary steps, resulting in a more efficient and cost-effective production line. With optimized production cycles, manufacturers can improve productivity and meet customer demands with greater agility.Enhanced Quality and Precision:The Blow Mold Tooling technique offers unparalleled quality and precision in product manufacturing. Employing cutting-edge materials and advanced technology, this solution ensures consistent high-standard output while reducing errors and defects. By eliminating inconsistencies and enhancing overall precision, manufacturers can achieve heightened customer satisfaction and establish a reputation for excellence in their respective industries.Versatility Across Industries:This innovative blow mold tooling solution is versatile and adaptable across a wide range of industries. From automotive and aerospace to consumer goods and packaging, manufacturers can leverage this technology to meet the unique needs of their sector. The ability to produce intricate shapes, complex designs, and diverse product ranges makes the Blow Mold Tooling technique an indispensable asset, enabling businesses to stay competitive in rapidly evolving markets.Cost Savings and Sustainable Manufacturing:The implementation of this groundbreaking blow mold tooling technique can lead to substantial cost savings for manufacturers. With enhanced efficiency and reduced labor requirements, companies can experience significant reductions in production costs. Moreover, the reduction in waste and material usage contributes to a sustainable manufacturing process, aligning with global efforts to minimize environmental impact. By minimizing energy consumption and optimizing resource utilization, manufacturers can establish themselves as responsible industry leaders.Competitive Edge:By adopting this pioneering blow mold tooling technique, companies can gain a competitive advantage in their respective markets. The streamlined production process allows for faster product launches, quicker response times to market trends, and increased flexibility in meeting customer demands. With an enhanced ability to offer customized products and rapid turnaround times, manufacturers can boost their market share, revenue, and overall industry standing.Conclusion:The introduction of the innovative Blow Mold Tooling technique marks a significant milestone in the manufacturing industry. Delivering streamlined production processes, enhanced quality, and versatility across industries, this technology offers manufacturers a competitive advantage in today's rapidly evolving markets. With substantial cost savings and a sustainable manufacturing approach, companies that embrace this cutting-edge tooling solution can position themselves as leaders in their fields, meeting customer demands with efficiency and excellence.
Automotive Exterior Door Trim Market: Key Players, Trends, Size, Growth, Opportunities and Forecast
China Car Exterior Door Trim Manufacturer Leads Industry with Innovative Solutions(Beijing, China) - China Car Exterior Door Trim Manufacturer, a leading player in the automotive industry, has emerged as a pioneer in innovative solutions for car door trims. With a strong focus on quality and customer satisfaction, the company has become a trusted name among both domestic and international auto manufacturers.Established in (year), China Car Exterior Door Trim Manufacturer has steadily grown to become a prominent manufacturer and supplier of door trims for the automotive industry. The company's commitment to superior craftsmanship and continuous innovation has propelled it to the forefront of the market.One of the key factors driving China Car Exterior Door Trim Manufacturer's success is its dedication to research and development. The company consistently invests in advanced technology and machinery to ensure it remains at the cutting edge of the industry. By adopting innovative manufacturing techniques, China Car Exterior Door Trim Manufacturer has been able to deliver high-quality products that meet the ever-changing demands of the market.In addition to its focus on technological advancements, China Car Exterior Door Trim Manufacturer has also prioritized sustainable practices. The company has implemented eco-friendly manufacturing processes to minimize its environmental footprint. By leveraging renewable resources and reducing waste, China Car Exterior Door Trim Manufacturer aims to contribute to a greener and more sustainable automotive industry.Moreover, China Car Exterior Door Trim Manufacturer's commitment to quality and customer satisfaction has paved the way for strong partnerships with renowned car manufacturers globally. The company's reputation for delivering superior products has made it a preferred supplier for both domestic and international brands. Through collaborative efforts, China Car Exterior Door Trim Manufacturer continues to develop customized solutions that not only meet but exceed the expectations of its esteemed clients.China Car Exterior Door Trim Manufacturer's product range consists of a wide variety of door trims, catering to multiple car models and specifications. By leveraging its expertise and experience, the company ensures that each door trim is specifically designed to enhance the aesthetics and functionality of the vehicles it serves. With a comprehensive understanding of market trends and consumer preferences, China Car Exterior Door Trim Manufacturer constantly updates its product portfolio to remain in sync with industry standards.The company's state-of-the-art manufacturing facilities employ skilled craftsmen who meticulously assemble every door trim with utmost precision. Each product undergoes thorough quality checks and inspections to guarantee that it meets the highest standards. By adhering to stringent quality control measures, China Car Exterior Door Trim Manufacturer commands a strong presence in the market, renowned for its durablity and reliability.Looking towards the future, China Car Exterior Door Trim Manufacturer is committed to continued innovation and growth. The company envisions expanding its production capabilities to cater to the evolving demands of the global automotive industry. Through its unwavering dedication to research and development, China Car Exterior Door Trim Manufacturer aims to stay ahead of the curve and remain a reliable partner for car manufacturers worldwide.As the automotive industry continues to evolve, China Car Exterior Door Trim Manufacturer stands as a shining example of excellence and innovation. By delivering advanced and eco-friendly door trims that set new benchmarks in quality, the company has firmly established itself as a leader in the industry. With its position at the forefront of technological advancements and commitment to customer satisfaction, China Car Exterior Door Trim Manufacturer is poised to shape the future of car door trims on a global scale.
Experts predict a significant growth in the demand for high-quality industrial molds in the coming years.
[Introduction]In today's ever-evolving industrial landscape, the demand for high-quality molds is at an all-time high. Industrial Moulds, a renowned manufacturer in the industry, has been fulfilling this demand with its innovative and efficient solutions. With a rich history and a commitment to excellence, the company has successfully carved a niche for itself in the competitive mold manufacturing sector. This news article will delve into the various strengths, achievements, and future prospects of Industrial Moulds, shedding light on how it has become a key player in the global market.[Company Background]Founded in the early 1960s, Industrial Moulds has continuously strived for perfection in its line of work. With a strong focus on research and development, the company has consistently challenged traditional manufacturing practices and introduced cutting-edge technologies to optimize the mold production processes. Over the years, Industrial Moulds has expanded both in terms of infrastructure and expertise, investing heavily in state-of-the-art machinery and attracting top talent in the field. Today, it stands as a testament to the power of innovative thinking and a testament to the importance of adapting to change.[Industry Prowess]Industrial Moulds' relentless pursuit of excellence has earned it numerous accolades in the mold manufacturing industry. Its commitment to delivering superior products and providing exceptional customer service has garnered the trust and loyalty of clients across the globe. The company's diverse range of molds caters to various industries, including automotive, packaging, consumer electronics, and medical. With a comprehensive understanding of industry requirements and an ability to customize molds as per client specifications, Industrial Moulds has become a go-to choice for businesses seeking high-quality and reliable molds.[Technology and Innovation]One of the driving forces behind Industrial Moulds' success is its focus on technology and innovation. The company's dedicated research and development team continuously explore new materials, manufacturing techniques, and design methodologies. By leveraging the latest advancements in 3D modeling, computer-aided design (CAD), and simulation software, Industrial Moulds has been able to optimize mold designs, reduce production time, and enhance overall efficiency. This commitment to technological advancement has not only ensured the company's competitiveness but has also contributed to the overall advancement of the mold manufacturing industry.[Commitment to Sustainability]Industrial Moulds is acutely aware of its environmental footprint and actively takes steps to minimize it. The company adheres to strict sustainability practices by using eco-friendly materials and processes whenever possible. By adopting energy-efficient machinery and actively reducing waste throughout its operations, Industrial Moulds showcases its dedication to building a sustainable future. Such a commitment has not only resonated with clients but has also positioned the company as a responsible corporate citizen.[Future Outlook]As Industrial Moulds looks ahead, it aims to further expand its global presence and diversify its product offerings. With a strong foothold in traditional markets, the company has identified emerging markets that present substantial growth opportunities. By adding new product lines that cater to evolving industry demands, Industrial Moulds intends to stay ahead of the curve and continue delivering exceptional value to its customers. The company also plans to invest in automation and robotics to enhance productivity and maintain its competitive edge.[Conclusion]Industrial Moulds, with its rich history, commitment to excellence, and inclination towards innovation, stands as a beacon of success in the mold manufacturing industry. Its dedication to delivering high-quality molds, coupled with a focus on sustainability and growth, has solidified its position as a global leader. With a blueprint that fosters technological advancements and customer satisfaction, the future seems bright for Industrial Moulds as it continues to shape the industrial landscape with its molds, one innovation at a time.
Exploring the Advantages of Large Part Injection Molding for Industrial Needs
Large Part Injection Molding Takes the Industry by Storm: Introducing a Game-Changer in the Manufacturing BusinessThe manufacturing industry has been a vital sector in the global economy for decades. With the increasing competition across businesses, the industry has witnessed a significant shift in its operational strategies, most notable in the injection molding process. Thanks to large part injection molding, a new game-changer now establishes itself as one of the most efficient, cost-effective, and eco-friendly methods to produce high-quality plastic parts with precision and accuracy.Among the leading pioneers in the field of large part injection molding is (brand name removed). This company has been at the forefront of manufacturing excellence for years, providing its customers with the most innovative solutions in the field of plastic molding. Through cutting-edge technology and a team of highly skilled personnel, (brand name removed) has been able to harness the power of large part injection molding to create products with precision, speed, and quality.Large part injection molding, as its name suggests, is the process of producing large and complex parts using injection molding machines. It offers several advantages over traditional molding methods. For one, large part molding presents one of the most cost-effective alternatives to produce large plastic parts, even with low-volume runs. Additionally, it allows manufacturers to produce parts far more quickly than traditional molding methods.One of the key benefits distinguishable in large part injection molding is the level of precision it provides. The machines used in the process have sophisticated software that ensures the final product meets or exceeds the required specifications. As such, large part molded products are much more precise than other alternatives, making them ideal for use in industries such as automotive, medical, and aerospace.Another substantial advantage of large part injection molding is that it significantly reduces material waste. Because the process only uses an exact amount of material, there is minimal need for material trimming. As a result, it produces more parts with less waste, making it an environmentally-friendly manufacturing process.The wide range of benefits has contributed to the increasing popularity of large part injection molding, with a growing demand for the process in the manufacturing industry. As one of the leading companies providing large part injection molding services, (brand name removed) has been meeting industry needs by embracing the latest technologies and trends. As a result, the company can produce parts of varying sizes, up to an impressive 30 feet by 25 feet with a weight limit of 15,000 pounds.Besides its large capacity, (brand name removed) offers customers a comprehensive range of services that suits any unique need. These services include product design consultations, prototyping, and custom mold design, among others. They are designed to walk customers through the entire manufacturing process, from product conceptualization to the final product delivery, ensuring a successful outcome.As customers look for effective solutions that guarantee efficiency, quality, and cost-effectiveness in the industry, (brand name removed) stands out as a business partner of choice. The company has set a bar in large part injection molding, ensuring that it delivers products that meet the highest industry standards. Its exceptional customer service, coupled with expertise in large part injection molding, makes it a go-to solution for businesses seeking high-quality plastic parts.From its reliable manufacturing processes, world-class service delivery to impressive product quality, (brand name removed) has undoubtedly redefined the injection molding industry through large part injection molding. Its reputation, growth, and impact in the industry speak to its commitment to staying ahead of the curve and providing customers with the best solutions available. In conclusion, large part injection molding is a revolutionary manufacturing process that is taking the industry by storm, delivering quality plastic parts that exceed industry standards in terms of efficiency, precision, and cost-effectiveness. The success of (brand name removed) in this field demonstrates the vast potential of large part injection molding to produce high-quality parts that meet the demands of the modern manufacturing industry.
Understanding the Concept of Molding Over Molding for Enhanced Product Manufacturing
Title: Revolutionary Molding Over Molding Technology Pioneered by [Company Name]Introduction:[Company Name], a leading innovator in the manufacturing industry, has recently introduced a groundbreaking technology called Molding Over Molding (MOM). This cutting-edge technique revolutionizes the conventional manufacturing process, offering unparalleled advantages in terms of efficiency, cost-effectiveness, and product quality. MOM has already garnered widespread attention and is poised to disrupt the market, making [Company Name] a frontrunner in molding technology.Body:1. Understanding Molding Over Molding (MOM):Molding Over Molding is a sophisticated technology that involves the layering or combining of two or more materials during the molding process. The technique enables the integration of various materials such as elastomers, plastics, or metals to create highly functional and durable products. By fusing different materials together, MOM eliminates the need for multiple manufacturing steps, reducing costs and increasing overall efficiency.2. Advantages of Molding Over Molding:a) Enhanced Product Design and Functionality: MOM allows companies to design products with complex geometries, intricate patterns, and multiple functionalities. This technique facilitates customization, enabling the production of unique, innovative, and ergonomic products that meet the ever-evolving demands of consumers.b) Improved Durability and Aesthetics: By combining different materials, MOM creates products that are more resistant to wear, tear, and impact. The integration of hard and soft materials enhances the overall durability, while the smooth transition between materials results in visually appealing and seamless product finishes.c) Cost Efficiency: Molding Over Molding eliminates the need for additional assembly and bonding processes. By consolidating various manufacturing steps into a single procedure, the technology significantly reduces production costs, while maintaining superior product quality. Furthermore, MOM reduces material waste and minimizes the risk of errors or defects, further contributing to cost savings.d) Streamlined Production Process: With Molding Over Molding, companies can achieve a streamlined and simplified manufacturing process, resulting in faster production cycles and increased productivity. The reduced number of steps involved in the manufacturing process allows for shorter lead times, facilitating quick response to market demands and gaining a competitive edge.3. Application Areas of Molding Over Molding:The versatility of Molding Over Molding makes it suitable for a wide range of industries and applications, including:a) Automotive Industry: MOM can be utilized in the production of vehicle components such as interior panels, instrument clusters, steering wheels, and gear shifters. The technology enables the integration of different materials, providing enhanced comfort, safety, and aesthetics.b) Electronics: Molding Over Molding is highly relevant in the electronics industry, where it can be employed in the manufacturing process of device casings, keypads, connectors, and cables. The technique ensures robustness, waterproofing, and longevity of electronic products.c) Medical Devices: MOM can play a vital role in the production of medical devices such as surgical instruments, drug delivery systems, hearing aids, and prosthetics. The ability to combine materials with varying properties enables the creation of innovative, patient-centric, and efficient healthcare solutions.d) Consumer Goods: Manufacturers of consumer goods can utilize Molding Over Molding to develop superior-quality products such as kitchenware, toys, and sporting equipment. The technique allows for the creation of aesthetically pleasing, durable, and ergonomic items that enhance user experience.4. [Company Name]'s Leadership in Molding Over Molding:[Company Name] has been at the forefront of manufacturing innovation for over [number of years] years. The introduction of Molding Over Molding technology underscores their commitment to providing industry-leading solutions to their clients. With a team of experienced engineers and state-of-the-art facilities, [Company Name] is positioned as a pioneer in the field of MOM, aiming to reshape manufacturing processes across industries.Conclusion:The advent of Molding Over Molding technology by [Company Name] presents a paradigm shift in the manufacturing industry. This cutting-edge technique offers unprecedented advantages in design flexibility, durability, cost-efficiency, and time-saving. As companies embrace this revolutionary technology, they can enhance their product offerings, improve customer satisfaction, and gain a competitive edge in today's dynamic market landscape. With [Company Name] leading the way, Molding Over Molding technology is set to transform the way products are manufactured globally.
Discover the Cost of Injection Moulding Dies: A Comprehensive Guide
Injection Moulding Die Cost: An Overview of the Factors InvolvedManufacturing companies all over the world use injection moulding as one of their primary manufacturing techniques. Whether it is automotive, medical, or consumer goods, injection moulding is widely used due to its high efficiency and precision. Injection moulding die is a key component of any injection moulding operation. It is the device that shapes plastic pellets or granules into a finished product.However, the cost of injection moulding dies can vary depending on several factors such as design, size, complexity, material, and finishing. In this article, we will discuss the various factors that impact injection moulding die costs.Factors that Impact Injection Moulding Die CostsDesignThe design of the injection moulding die is one of the primary factors that impacts the cost. A complicated and intricate design would require more engineering time, ultimately increasing the overall cost. On the other hand, a simple design would require less engineering time and would be more cost-effective.SizeThe size of the injection moulding die plays a significant role in determining its cost. Larger dies would require more material and energy during production, increasing the overall cost. The complexity of the design would also increase with the size of the die, ultimately impacting the final cost.ComplexityThe complexity of the injection moulding die determines the amount of detail required in the design and manufacturing process. A more intricate design requires more sophisticated manufacturing techniques, ultimately resulting in a higher cost.MaterialThe material used to manufacture the injection moulding die also impacts the final cost. Aluminium is a popular choice for injection moulding dies as it is cheaper, faster, and easier to manufacture. However, it is not as durable as steel and requires frequent replacement. Steel is a more expensive option, but it is more durable and can typically withstand higher temperature and pressure.FinishingThe finishing of the injection moulding die is also a factor that affects the cost. Depending on the desired finish, additional processes such as polishing or texturing may be required, ultimately increasing the overall cost.How to Reduce Injection Moulding Die Costs1. Simplify the DesignAs previously mentioned, the design of the injection moulding die plays a significant role in determining its cost. Simplifying the design can reduce the complexity of the manufacturing process and ultimately reduce the cost.2. Use the Right MaterialChoosing the right material for the injection moulding die can have a significant impact on the cost. Using aluminium instead of steel may be a better choice for simple products that require short production runs. On the other hand, using steel may be a better option for more complex products that require a higher degree of durability.3. Consider the Lifecycle of the DieConsider the lifecycle of the injection moulding die when making decisions about its production. The cost of the die is not just the upfront cost but also the cost of maintenance, repair, and replacement over its lifetime. A more expensive steel die may have a longer lifespan and require less frequent replacement, ultimately making it the more cost-effective option in the long run.ConclusionInjection moulding is a widely-used manufacturing technique that allows for high efficiency and precision. The cost of the injection moulding die can vary depending on several factors such as design, size, complexity, material, and finishing. However, by simplifying the design, using the right material, and considering the lifecycle of the die, manufacturers can reduce the overall cost and increase profitability. Ultimately, it is important to consider the cost-benefit analysis of the injection moulding die to ensure that the final product meets the required specifications at a cost-effective price.
How to Make Your Own Potion Bottle Mold for Halloween Crafts and Decorations
A Potion Bottle Mold Invention Sparks Interest in the IndustryA new invention, a potion bottle mold, is set to revolutionize the cosmetics industry. This invention is a game-changer for the industry as the mold is capable of creating unique, intricate, and desirable glass bottles of any shape or size. With the cut-throat competition in the cosmetics industry, this innovation is considered a welcome and necessary advancement that provides a competitive edge to manufacturers.The new potion bottle mold has been developed by a leading company in the cosmetics industry, which has been producing high-quality packaging materials for the industry for several years. The company is renowned for their quality packaging materials and their ability to provide innovative and cost-effective solutions for their clients.According to the company's website, they specialize in designing and manufacturing packaging components for a wide range of industries, including cosmetics, skincare, and pharmaceuticals. Their attention to detail, professionalism, and commitment to quality have helped them establish a loyal customer base in the industry.The newly developed potion bottle mold is the latest in their line of innovative products that are aimed at improving the customer experience and driving sales growth for their clients.The mold is produced using state-of-the-art technology and is capable of creating glass bottles of any shape or size. This provides manufacturers with endless options when it comes to designing packaging that reflects their brand and resonates with consumers.The mold has a unique feature that allows for intricate designs to be created on the surface of the bottle. This means that the bottles can be embossed or engraved with designs that complement the brand's identity and helps their products to stand out on the shelves.The potion bottle mold has been met with enthusiasm in the industry, with industry experts praising the innovation for its ability to provide manufacturers with a robust and cost-effective solution to their packaging needs. This comes at a time when the industry is experiencing increased competition, making it difficult to differentiate one product from the other.Manufacturers can now leverage the mold to create unique packaging that not only sets their products apart from their competitors but also enhances the user experience. Consumers are increasingly looking for products that are aesthetically pleasing and offer value for their money. With the potion bottle mold, manufacturers can now offer products that tick all the boxes.The mold is also cost-effective, allowing manufacturers to produce quality packaging materials at an affordable price point. This is important as packaging costs can quickly add up, especially when producing large quantities of products.In conclusion, the new potion bottle mold is set to revolutionize the cosmetics industry, providing manufacturers with a robust and cost-effective solution to their packaging needs. The mold's ability to produce unique, intricate, and aesthetically pleasing packaging materials means that manufacturers can now offer products that resonate with consumers and stand out from their competitors. With the increasing demand for quality packaging materials in the industry, the potion bottle mold is a timely innovation that is set to spark further interest in the industry.
Discover the Latest Innovations in Plastic Box Molds for Improved Efficiency and Longevity
Plastic Boxes Molds - Innovating the Plastic Industry, One Mold at a TimeIn today's fast-moving world, plastic products have become an essential part of our daily lives. From packaging to storage, plastics have become the go-to material for a variety of needs. While plastic products have made our lives easier, the manufacturing process of these products is complex and requires a lot of effort. Amongst the various manufacturing processes of plastic products, plastic injection molding is one of the most popular ones. And when it comes to molds for these products, Plastic Boxes Molds has become one of the premium names in the industry.Established in the year 2010, Plastic Boxes Molds, a privately owned company based in China, has been a frontrunner in the plastic injection molding industry. The company has been making great strides over the years by serving a myriad of industries, including automotive, defense, and consumer goods. The company prides itself on being one of the best in the plastic injection molding business, with a state-of-the-art production facility spanning over 6000 square meters.Plastic Boxes Molds has made a name for itself in the industry by manufacturing a wide variety of molds, including but not limited to custom thermoplastic molds and injection molds. The company has made its mark by providing high-quality molds that are tailored to the specific needs of each client. Plastic Boxes Molds believes that the key to success is to continually innovate and evolve with the changing industry trends. As a result, Plastic Boxes Molds has made significant investments in R&D to keep up with the latest developments in the industry.The company prides itself on its ability to provide end-to-end services to its clients. The services provided by Plastic Boxes Molds cover every aspect of the plastic injection molding process, from design and engineering to the final product. The company's expertise in designing and engineering molds has made it one of the most sought-after companies in the industry.Plastic Boxes Molds has a team of highly skilled professionals who are passionate about their work. The team takes a hands-on approach to every project they undertake, ensuring that every detail is taken care of to deliver the best results. The company's commitment to excellence has garnered a loyal customer base, who have come to rely upon the expertise and quality of the molds provided by Plastic Boxes Molds.Apart from its commitment to excellence, another aspect that sets Plastic Boxes Molds apart from its competition is its use of cutting-edge technology. The company has made significant investments in machinery and equipment, ensuring that the molds created are of the highest quality. The use of advanced technology has also allowed Plastic Boxes Molds to provide faster turnaround times to its clients, ensuring that projects are completed on time.In conclusion, Plastic Boxes Molds has become a prominent name in the plastic injection molding industry owing to its commitment to innovation, excellence, and use of advanced technology. The company's dedication to providing end-to-end services has made it a one-stop-shop for clients looking for custom molds. With its skilled team, state-of-the-art production facility, and ability to keep up with the latest developments in the industry, Plastic Boxes Molds is poised to continue its success story and innovate the plastic industry, one mold at a time.
Guide to Finding High-Quality Vegetable Crate Molds
In today's world, the demand for eco-friendly and sustainable products has been on the rise. This is because people are becoming aware of the impact they have on the environment and are taking steps to reduce their carbon footprint. One company that has been at the forefront of this trend is a vegetable crate mould supplier. The company is dedicated to creating sustainable products that are not only environmentally friendly but also durable and cost-effective.The company was founded with a mission to create products that make a difference in the world. Their focus is to develop sustainable solutions for agriculture, food, and beverage industries. They do this by utilizing advanced design, engineering, and tooling techniques to create products that are lightweight, durable, and highly functional.As a result of their innovative approach, the company has become a leading supplier of vegetable crate moulds. Their products are used by farmers, distributors, and retailers across the globe. They offer a comprehensive range of vegetable crate moulds that are designed to meet the needs of every customer. Whether you are looking for a large or small crate, they have the perfect solution for you.One of the key features of their products is their durability. The vegetable crate moulds are made from high-quality materials that are designed to withstand the toughest conditions. This means that they can be used for years without any deterioration in quality or performance. Additionally, the products are designed to be stackable, which makes them ideal for transportation and storage.Another great feature of their products is their eco-friendliness. The company is committed to reducing the impact that their products have on the environment. To achieve this, they use sustainable materials in the production process. Their vegetable crate moulds are made from recycled plastics, which not only reduces waste but also conserves energy.Moreover, their products are designed to be reusable. This means that they can be used again and again, reducing the need for new products to be manufactured and reducing the carbon footprint of the industry. Furthermore, the products are easy to clean and maintain, which means that they can be used for a long time without needing to be replaced.One of the unique aspects of the company is their commitment to innovation. They are constantly exploring new techniques and technologies to improve the functionality and durability of their products. They invest heavily in research and development to ensure that they stay ahead of the competition in terms of product quality, performance, and eco-friendliness.Their dedication to innovation has resulted in several breakthroughs in the vegetable crate mould industry. For instance, they have developed products that are lighter, stronger, and more durable than their competitors. This has helped them to become a preferred supplier for many customers.The company's success is also driven by their excellent customer service. They are always available to answer any questions that customers may have and to provide support and guidance throughout the buying process. They are committed to ensuring that their customers are satisfied with their purchases and offer a money-back guarantee if customers are not satisfied with their products.In conclusion, the vegetable crate mould supplier is a company that is leading the way in sustainable and eco-friendly products. Their commitment to innovation, quality, and customer service has made them a preferred supplier for many customers. They are dedicated to creating products that are durable, functional, and easy to use while also protecting the environment. With their focus on sustainability, the company is set to become a leader in the industry for years to come.
How to Reduce Injection Molding Tooling Costs for Your Business
Injection Molding Tooling CostInjection molding is a widely used manufacturing process that enables the production of high-quality plastic parts in large volumes. It involves injecting molten plastic material into a mold cavity, allowing it to cool and solidify before ejecting the finished product. While injection molding offers numerous advantages in terms of efficiency and product quality, one crucial factor that companies need to consider is the cost of tooling.Tooling refers to the design and manufacture of the molds and associated components required for injection molding. These molds play a critical role in determining the final product's shape, size, and quality. Therefore, investing in high-quality tooling is crucial for achieving optimal results. However, tooling costs can vary significantly depending on various factors such as the complexity of the part, the material used, and the production volume.Brand X, a leading manufacturer in the injection molding industry, understands the importance of providing top-notch tooling solutions while keeping costs reasonable. With its extensive experience and cutting-edge technology, Brand X has developed a streamlined process that ensures efficient tooling production without compromising on quality.The first step in the tooling process is design and engineering. Brand X employs a team of experienced engineers who work closely with clients to develop precise and robust mold designs. Utilizing advanced CAD software, they can simulate the injection molding process, identifying potential design flaws and optimizing the mold's performance. This meticulous approach helps minimize costly mistakes and reduces the need for design revisions.Once the mold design is finalized, Brand X utilizes state-of-the-art machining equipment to manufacture the tooling components. Precision CNC milling and electrical discharge machining (EDM) techniques ensure that the molds are manufactured to the exact specifications, allowing for consistent and high-quality production runs. Brand X's commitment to using the latest technology enables faster turnaround times and reduces production costs.Furthermore, Brand X understands that different projects require different molds. Some products may require simple, single-cavity molds, while others may necessitate complex multi-cavity molds to maximize productivity. With its expertise in tooling design and production, Brand X can optimize mold designs to minimize material waste and increase production efficiency. This ultimately helps reduce tooling costs for clients.In addition to initial tooling costs, maintenance and repair expenses are essential considerations. Over time, molds may experience wear and tear, resulting in reduced product quality and increased production downtime. Brand X offers comprehensive maintenance and repair services that help prolong the lifespan of the molds, minimizing long-term costs for clients. By regularly inspecting and repairing molds, Brand X ensures that they remain in optimal condition, enabling consistent production runs and reducing the need for costly mold replacements.Another cost-saving factor provided by Brand X is its ability to accommodate varying production volumes. Whether a client requires low-volume prototyping or high-volume mass production, Brand X can adapt its tooling solutions to meet their needs. This scalability allows companies to optimize their production processes without incurring unnecessary tooling expenses.In conclusion, injection molding tooling cost is a significant consideration for any company looking to utilize this manufacturing process. Brand X's commitment to providing high-quality tooling solutions at reasonable costs sets it apart in the industry. From meticulous mold design and advanced machining techniques to comprehensive maintenance services, Brand X ensures efficient production runs while minimizing expenses. By partnering with Brand X, companies can benefit from cost-effective tooling solutions without compromising on product quality or production efficiency.