High-Quality ABS Pellets for Injection Molding: Everything You Need to Know
By:Admin
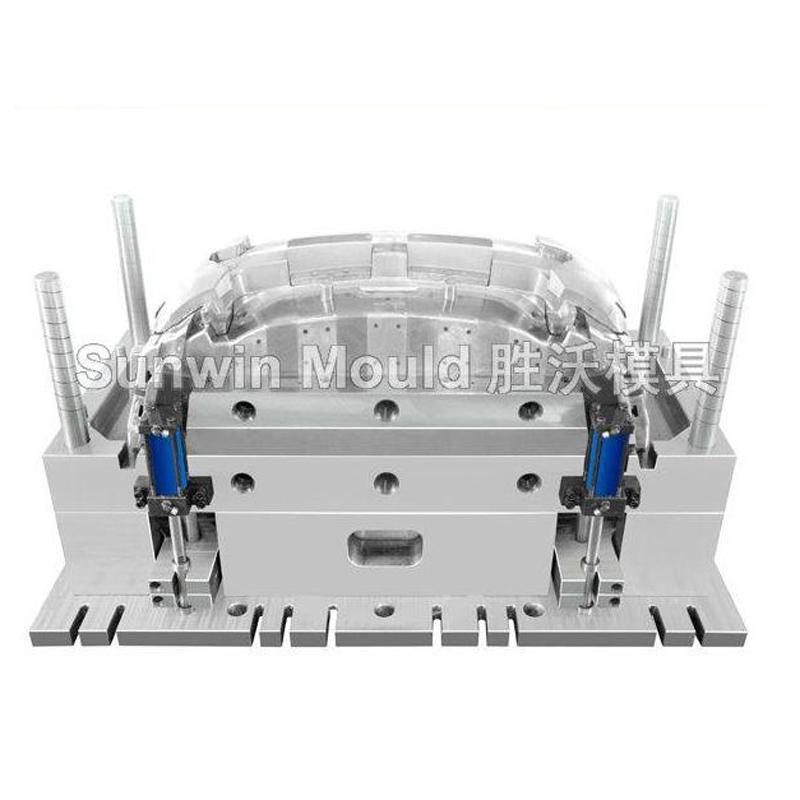
The market for injection molding is growing rapidly, and the demand for high-quality ABS pellets is higher than ever before. With the increasing need for durable and versatile plastics for a wide range of industries, companies are constantly on the lookout for reliable suppliers of ABS pellets for injection molding. This is where [Company Name] comes in, offering top-quality ABS pellets that meet the strictest industry standards.
[Company Name] is a leading supplier of ABS pellets for injection molding, with a reputation for delivering excellent quality products to customers around the world. The company has been in the business for over [number] years, and has a deep understanding of the unique requirements of the injection molding industry. This expertise allows the company to provide its customers with tailored solutions that meet their specific needs.
The ABS pellets offered by [Company Name] are highly versatile, making them suitable for a wide range of applications. Whether it's for automotive parts, electronic components, or consumer goods, these pellets are designed to deliver outstanding performance and durability. The company's ABS pellets are also available in a variety of grades and colors, allowing customers to choose the perfect material for their specific injection molding needs.
One of the key factors that sets [Company Name] apart from its competitors is its commitment to quality. The company has strict quality control measures in place throughout the production process, ensuring that its ABS pellets consistently meet the highest standards. From raw material sourcing to the final packaging and delivery, every step is carefully monitored to guarantee the quality and consistency of the products.
In addition to its dedication to quality, [Company Name] also prides itself on its excellent customer service. The company works closely with its customers to understand their individual requirements and provide them with the best possible solutions. This customer-centric approach has earned [Company Name] a solid reputation in the industry, with many long-standing relationships with satisfied clients.
As the demand for ABS pellets for injection molding continues to grow, [Company Name] is well-positioned to meet the needs of its customers. The company has a strong focus on innovation and constantly seeks to improve its products and services to stay ahead of the competition. With a team of highly skilled professionals and state-of-the-art manufacturing facilities, [Company Name] is able to consistently deliver high-quality ABS pellets that meet the evolving needs of the injection molding industry.
In conclusion, [Company Name] is a trusted supplier of ABS pellets for injection molding, with a strong track record of delivering exceptional products and services to its customers. With a commitment to quality, innovation, and customer satisfaction, the company is well-equipped to meet the growing demand for ABS pellets and continue to be a leader in the injection molding industry.
Company News & Blog
Injection Molding Process for Pet Plastic: A Complete Guide
**TO BE REMOVED BEFORE PUBLISHING**Pet Plastic Injection Molding is a leading technology in the field of plastic injection molding. The company has been providing high-quality, cost-effective plastic injection molding solutions for over 20 years and has gained a reputation for its innovation and dedication to customer satisfaction.Pet Plastic Injection Molding specializes in the manufacturing of precision plastic components for a wide range of industries, including automotive, electronics, medical, and consumer goods. The company's state-of-the-art facilities are equipped with the latest technology and machinery, allowing them to produce complex and intricate plastic parts with exceptional accuracy and efficiency.With a team of highly skilled engineers, designers, and technicians, Pet Plastic Injection Molding is able to provide end-to-end solutions, from design and prototyping to production and assembly. Their expertise and attention to detail ensure that every project is completed to the highest standards, meeting the exact specifications and requirements of their clients.One of the key advantages of Pet Plastic Injection Molding is their ability to work with a variety of materials, including PET, PP, PE, PVC, and more. This versatility allows them to cater to a diverse range of customer needs, whether it be for rigid containers, flexible packaging, automotive components, or medical devices.In addition to their technical capabilities, Pet Plastic Injection Molding is committed to sustainability and environmental responsibility. The company has implemented eco-friendly practices throughout their operations, from the efficient use of raw materials to the recycling and reuse of waste products. By prioritizing sustainability, they aim to minimize their environmental impact and contribute to a cleaner, greener future.Pet Plastic Injection Molding's dedication to quality and excellence has earned them the trust and loyalty of numerous clients worldwide. Their commitment to continuous improvement and innovation ensures that they stay at the forefront of the plastic injection molding industry, offering cutting-edge solutions that meet the evolving needs of the market.In line with their commitment to customer satisfaction, Pet Plastic Injection Molding offers personalized support and collaboration throughout every stage of the project. Their team works closely with clients to understand their needs, provide expert advice, and deliver customized solutions that exceed expectations. This customer-centric approach has earned them a reputation for reliability, responsiveness, and integrity.The company's success and reputation can be attributed to their unwavering dedication to quality, innovation, and customer satisfaction. They have consistently demonstrated their ability to meet the most demanding requirements of their clients, delivering exceptional results time and time again.In conclusion, Pet Plastic Injection Molding is a global leader in plastic injection molding, renowned for their technical expertise, commitment to sustainability, and customer-centric approach. With a track record of excellence spanning over two decades, they continue to set the standard for high-quality, precision plastic components. Whether it's for complex automotive parts or intricate medical devices, Pet Plastic Injection Molding is the go-to partner for reliable, cost-effective, and cutting-edge plastic injection molding solutions.
Discover Precision Injection Molding Techniques for High-Quality Plastic Parts
Title: Advancements in Plastic Molding Propels Manufacturing Industry ForwardIntroduction:The field of plastic molding has witnessed remarkable advancements over the years, resulting in a significant transformation of the manufacturing industry. One prominent player in this sector, referred to as "Prototype Plastic Molding" in this article, has emerged as a pioneer in delivering cutting-edge plastic molding solutions. Throughout this news article, we will explore the ongoing developments in plastic molding technology and delve into the capabilities of this leading company.1. The Evolution of Plastic Molding:The integration of advanced technologies has revolutionized the plastic molding industry, enhancing its efficiency, precision, and overall productivity. Traditional molding methods have been replaced by innovative techniques, with a strong focus on automation and computer-controlled processes. As a result, manufacturers are now able to produce complex and intricate plastic components with unmatched accuracy.2. Introduction to Prototype Plastic Molding:Prototype Plastic Molding, a globally recognized company, has been at the forefront of transforming the plastic molding landscape. With a strong emphasis on research and development, the company has consistently pushed the boundaries of manufacturing capabilities. They specialize in providing high-quality plastic parts to various industries such as automotive, electronics, medical, and consumer goods.3. Advanced Technologies:Prototype Plastic Molding has successfully adopted and integrated several advanced technologies within its manufacturing processes. The company utilizes computer-aided design (CAD) software to create precise digital models of the desired plastic components. These models are then translated into instructions for computer numerical control (CNC) machines, which enable the production of molds with extreme precision. Moreover, the company incorporates state-of-the-art 3D printing technologies to create prototypes before mass production, thereby ensuring the seamless development of new products.4. Enhanced Prototyping Capabilities:Through the utilization of their advanced CAD software and 3D printing technologies, Prototype Plastic Molding has elevated its prototyping capabilities. This enables their clients to visualize and assess the functionality, aesthetics, and ergonomics of their plastic components before final production begins. By streamlining the prototyping phase, the company diminishes the time and costs associated with product development, creating a competitive advantage for their clients.5. Emphasis on Sustainability:Prototype Plastic Molding maintains a strong commitment to sustainability, actively exploring ways to minimize waste and lower their environmental impact. The company utilizes recycled materials whenever possible, while also developing innovative solutions to optimize material usage. By implementing sustainable practices and adhering to stringent quality control measures, they ensure eco-friendly production while simultaneously meeting the evolving demands of the market.6. Cutting-edge Equipment and Expertise:Prototype Plastic Molding continuously invests in cutting-edge machinery and equipment to enhance their manufacturing capabilities. With a team of experienced professionals, they oversee every step of the production process, adhering to strict quality control standards. This holistic approach guarantees the delivery of excellent results while maintaining a rapid turnaround time for their customers.Conclusion:The advancements in plastic molding technology, spearheaded by companies like Prototype Plastic Molding, are revolutionizing the manufacturing sector. With their innovative techniques, commitment to sustainability, and expertise in delivering high-quality plastic components, Prototype Plastic Molding has earned a commendable reputation in the industry. As the manufacturing industry continues to evolve, plastic molding is expected to play an increasingly significant role, shaping the future of numerous sectors.
Innovative Basket Moulds Shaping the Manufacturing Scene in China
Title: Leading Chinese Mould Manufacturer Introduces High-Quality Basket MouldsIntroduction:China, renowned for its leading position in the manufacturing industry, continues to make remarkable strides in various sectors. Today, we highlight the exceptional work of China Basket Mould, a premier mould manufacturer that has gained international acclaim for its high-quality basket moulds. With a strong commitment to precision, innovation, and customer satisfaction, China Basket Mould has successfully carved a niche for itself in the highly competitive global market.Company Background:China Basket Mould, established in 2005, has emerged as a key player in the mould manufacturing industry. Headquartered in Shenzhen, China, the company boasts state-of-the-art facilities and a team of highly skilled engineers and designers. With years of experience and technical expertise, China Basket Mould has built a reputation for delivering superior moulds that meet the diverse needs of customers worldwide.Innovative Design and Engineering:1. Cutting-edge Technology:China Basket Mould prides itself on adopting the latest technologies and utilizing advanced equipment in its manufacturing processes. By staying at the forefront of technological advancements, the company is able to produce high-precision basket moulds that exhibit exceptional durability and efficiency.2. Design Excellence:The design team at China Basket Mould deserves commendation as they constantly strive to develop innovative and ergonomic designs. Understanding the evolving needs of the industry, the company ensures that its basket moulds are not only functional, but also aesthetically pleasing. This attention to detail sets China Basket Mould apart from its competitors.Quality Assurance:1. Rigorous Quality Control Standards:China Basket Mould adheres to stringent quality control measures throughout the manufacturing process. Every basket mould undergoes comprehensive testing, ensuring that it meets the highest industry standards. This commitment to quality has earned the company numerous certifications, cementing its reputation as a trustworthy and reliable supplier.2. Optimal Material Selection:The company's careful selection of top-grade materials plays a crucial role in the durability and performance of their basket moulds. China Basket Mould only sources materials from reputable suppliers, guaranteeing that their moulds can withstand prolonged usage without compromising quality.Global Reach and Customer Satisfaction:1. Expanding International Presence:With a strong global distribution network, China Basket Mould has successfully penetrated multiple markets worldwide. The company's commitment to timely delivery and exceptional customer service has enabled it to secure long-term partnerships with clients across various industries.2. Customized Solutions:Recognizing that every client has unique requirements, China Basket Mould offers customized solutions to cater to specific demands. Whether it be modifications to existing designs or developing moulds from scratch, the company's team of experts ensures prompt and tailored solutions, thereby maximizing customer satisfaction.Contributing to Sustainable Development:China Basket Mould understands the importance of sustainability and actively strives to reduce its environmental impact. By employing energy-efficient manufacturing processes and recycling materials, the company demonstrates a commitment to sustainability and corporate social responsibility.Conclusion:China Basket Mould's unwavering commitment to high-quality, innovative design, and customer satisfaction have positioned it as a leading player in the global mould manufacturing industry. With a dedication to precision, utilization of cutting-edge technologies, and an extensive distribution network, the company continues to expand its global reach while maintaining the highest standards of quality. Whether it is the basket moulds used in households, supermarkets, or other commercial applications, China Basket Mould remains a preferred choice for customers worldwide.
Revolutionizing Manufacturing: The Key Advantages of Injection Molding
Introducing Innovative Insert Injection Molding Technology: Revolutionizing Manufacturing ProcessesIn an ever-evolving world, where technology is constantly pushing the boundaries of numerous industries, insert injection molding has emerged as a game-changing manufacturing process. This groundbreaking innovation, employed by numerous companies across various sectors, allows for the production of highly intricate and detailed products with unmatched precision and efficiency.One prominent leader in the insert injection molding industry is the renowned company {}, known for its commitment to excellence and cutting-edge technology. With a vast portfolio of successful projects and a reputation for delivering top-tier solutions, {} stands at the forefront of revolutionizing manufacturing processes.Insert injection molding is a manufacturing technique that involves injecting molten material, typically a thermoplastic or thermosetting polymer, into a pre-formed mold. Nevertheless, what makes this technique unique is the incorporation of inserts during the molding process. These inserts can be metal, ceramic, or plastic parts that are placed strategically within the mold, enhancing the final product's durability and functionality.The advantages of insert injection molding cannot be overstated. First and foremost, this process allows for a high degree of design flexibility. Inserts can be precisely positioned within the mold, thereby enabling the creation of intricate components with unparalleled accuracy. This level of precision opens up new possibilities for industries such as automotive, electronics, and medical devices, where intricate and complex parts are often required.Furthermore, insert injection molding drastically reduces manufacturing time and costs. By incorporating inserts during the molding process, manufacturers can eliminate the need for secondary operations such as drilling, fastening, or welding. This streamlining of production eliminates additional labor costs and significantly reduces assembly time, resulting in a more efficient and cost-effective manufacturing process.Moreover, insert injection molding offers enhanced product quality and durability. The integration of inserts improves the structural integrity of the final product, making it stronger and more resistant to external factors such as temperature fluctuations, pressure, or mechanical stress. Consequently, products manufactured through this process boast increased reliability and longevity, meeting the stringent demands of various industries.With a vision to revolutionize manufacturing processes, {} has perfected their insert injection molding techniques by combining innovative technology, engineering expertise, and meticulous quality control. {} has established itself as a trusted partner for numerous industry leaders, delivering exceptional solutions tailored to their specific needs.One industry that has greatly benefited from insert injection molding is the automotive sector. With an increasing demand for lightweight and durable components, this technology allows automotive manufacturers to produce intricate and complex parts that were once deemed challenging. From interior trims to electronic housings, insert injection molding has become the go-to solution for achieving high precision and outstanding performance in the automotive industry.Similarly, the electronics industry has witnessed the transformative power of insert injection molding. With the growing trend of miniaturization, electronics manufacturers constantly seek ways to pack more functionality in smaller devices. Insert injection molding enables the production of intricate electronic components with reduced form factors, without compromising their structural integrity or performance. This technology has facilitated the development of innovative electronic devices, offering users a level of convenience and functionality never seen before.Lastly, the medical device industry has embraced insert injection molding for manufacturing critical components such as catheters, implants, or surgical instruments. These devices require exceptional precision, biocompatibility, and strength, all of which are made possible through insert injection molding. This technology ensures that medical devices meet the rigorous quality and safety standards, while also allowing for cost-effective solutions in an industry where every second matters.In conclusion, insert injection molding has emerged as a game-changing technology in the manufacturing industry. With innovation at its core, {} has been instrumental in advancing this technique, revolutionizing numerous industries along the way. The diverse advantages of insert injection molding, including design flexibility, reduced costs, enhanced product quality, and durability, make it an indispensable manufacturing solution. As technology continues to evolve, we can only anticipate further advancements in this field, resulting in even more efficient and groundbreaking manufacturing processes.
Injection Molding: How It Works and Its Benefits
Iml Injection Molding, a leading manufacturer in the plastic injection molding industry, has recently made significant advancements in their technology, positioning themselves as a key player in the industry. Founded in 1995, the company has grown to become a well-established manufacturer of high-quality plastic products. Their state-of-the-art facilities and experienced team have enabled them to provide top-notch solutions to their clients, both locally and internationally.Iml Injection Molding has always been at the forefront of innovation and has continuously invested in the latest technologies to enhance their manufacturing processes. Their recent advancement in injection molding technology has further solidified their position as an industry leader.The company's innovative IML (In-Mold Labeling) technology allows for the incorporation of complex and detailed designs directly into the molded plastic products. This process involves the placement of a pre-printed label into the mold, where it fuses with the molten plastic, resulting in a seamless and durable finish. This technology has revolutionized the way in which branding and labeling are integrated into plastic products. With IML, the labels are an integral part of the product, eliminating the need for additional labeling processes and ensuring a high level of durability and resistance to wear and tear.In addition to providing superior aesthetic appeal, Iml Injection Molding's IML technology offers a range of functional benefits. The labels are highly resistant to moisture, chemicals, and scratches, making them ideal for a wide range of applications, including food packaging, household products, and automotive components. Furthermore, the in-mold labeling process allows for faster production cycles and reduced labor costs, resulting in a more efficient and cost-effective manufacturing solution."We are thrilled to introduce our advanced IML technology to the market," says the CEO of Iml Injection Molding. "This innovation represents a significant milestone for our company and for the plastic injection molding industry as a whole. We believe that our IML technology will set a new standard for product labeling and branding, providing our clients with unparalleled design possibilities and functional advantages."The company's commitment to innovation and excellence has garnered them a strong reputation in the industry. Their IML technology has already received positive feedback from clients and has been met with enthusiasm from various sectors, including the food and beverage, consumer goods, and automotive industries. With this latest advancement, Iml Injection Molding has enhanced their capabilities and strengthened their position as a preferred partner for high-quality plastic products.In conclusion, Iml Injection Molding's IML technology represents a significant leap forward for the plastic injection molding industry. The company's dedication to innovation and their commitment to providing top-quality solutions have positioned them as a leader in the industry. With their advanced IML technology, Iml Injection Molding is well-equipped to meet the diverse needs of their clients and to continue driving advancements in the plastic manufacturing sector.
Discover the Cost of Injection Moulding Dies: A Comprehensive Guide
Injection Moulding Die Cost: An Overview of the Factors InvolvedManufacturing companies all over the world use injection moulding as one of their primary manufacturing techniques. Whether it is automotive, medical, or consumer goods, injection moulding is widely used due to its high efficiency and precision. Injection moulding die is a key component of any injection moulding operation. It is the device that shapes plastic pellets or granules into a finished product.However, the cost of injection moulding dies can vary depending on several factors such as design, size, complexity, material, and finishing. In this article, we will discuss the various factors that impact injection moulding die costs.Factors that Impact Injection Moulding Die CostsDesignThe design of the injection moulding die is one of the primary factors that impacts the cost. A complicated and intricate design would require more engineering time, ultimately increasing the overall cost. On the other hand, a simple design would require less engineering time and would be more cost-effective.SizeThe size of the injection moulding die plays a significant role in determining its cost. Larger dies would require more material and energy during production, increasing the overall cost. The complexity of the design would also increase with the size of the die, ultimately impacting the final cost.ComplexityThe complexity of the injection moulding die determines the amount of detail required in the design and manufacturing process. A more intricate design requires more sophisticated manufacturing techniques, ultimately resulting in a higher cost.MaterialThe material used to manufacture the injection moulding die also impacts the final cost. Aluminium is a popular choice for injection moulding dies as it is cheaper, faster, and easier to manufacture. However, it is not as durable as steel and requires frequent replacement. Steel is a more expensive option, but it is more durable and can typically withstand higher temperature and pressure.FinishingThe finishing of the injection moulding die is also a factor that affects the cost. Depending on the desired finish, additional processes such as polishing or texturing may be required, ultimately increasing the overall cost.How to Reduce Injection Moulding Die Costs1. Simplify the DesignAs previously mentioned, the design of the injection moulding die plays a significant role in determining its cost. Simplifying the design can reduce the complexity of the manufacturing process and ultimately reduce the cost.2. Use the Right MaterialChoosing the right material for the injection moulding die can have a significant impact on the cost. Using aluminium instead of steel may be a better choice for simple products that require short production runs. On the other hand, using steel may be a better option for more complex products that require a higher degree of durability.3. Consider the Lifecycle of the DieConsider the lifecycle of the injection moulding die when making decisions about its production. The cost of the die is not just the upfront cost but also the cost of maintenance, repair, and replacement over its lifetime. A more expensive steel die may have a longer lifespan and require less frequent replacement, ultimately making it the more cost-effective option in the long run.ConclusionInjection moulding is a widely-used manufacturing technique that allows for high efficiency and precision. The cost of the injection moulding die can vary depending on several factors such as design, size, complexity, material, and finishing. However, by simplifying the design, using the right material, and considering the lifecycle of the die, manufacturers can reduce the overall cost and increase profitability. Ultimately, it is important to consider the cost-benefit analysis of the injection moulding die to ensure that the final product meets the required specifications at a cost-effective price.
The Advantages and Process of Two Color Injection Molding
Two Color Injection Molding Creates Exciting New Possibilities for Companies Across IndustriesInjection molding is a widely used process, whereby a molten material is injected into a mold to create a solid product. Traditionally, single color injection molding had been used to produce products, but with the advancements in technology, two-color injection molding has become increasingly popular in recent years. These innovative machines allow manufacturers to produce products with two distinct colors, textures, or even materials all in one efficient process.One company at the forefront of this technology is **insert brand**. The company prides itself on manufacturing high-quality two-color injection molding machines that help businesses from a range of industries create innovative products with multiple colors and intricate designs.**Insert brand** is a reputable company with years of experience in the injection molding industry. They have revolutionized this process with their specialization in two-color injection molding.In an interview with **insert spokesman name**, he explained the advantages of two-color injection molding over the traditional single-color process. "Two-color injection molding has been widely applied in various industries. This technology enables manufacturers to achieve improved product functionality and aesthetics while reducing production costs and delivery time. It opens up opportunities for intricate designs and textures, as well as the ability to combine different materials like soft and hard plastics."In addition to offering manufacturers the freedom to combine different materials and colors, **insert brand**’s two-color injection molding machines boast features like high precision, low waste, and high efficiency. Furthermore, this method can also decrease the probability of errors, providing a better end product with superior quality.Moreover, **insert brand**’s two-color injection molding machines have a wide range of applications across various industries. For example, in the automotive industry, two-color injection molding can be used to produce car accessories, such as gear shift knobs and dashboard components, which can stand out from the rest of the interior. In the consumer product market, two-color injection molding is used to manufacture quirky and innovative items ranging from toys to kitchenware, from headphones to phone cases. It is even used in the accessory market for producing fashionable and stylish pieces.**Insert brand**’s two-color injection molding process is also highly eco-friendly. Unlike traditional manufacturing methods, where dyed parts need to be painted or coated, creating two-color injection molded parts does not produce additional waste material. That means less waste is generated, and fewer chemicals are required during the production process.In addition to being environmentally friendly, two-color injection molding also offers many benefits to companies aiming to streamline their production process. The use of two-color injection molding reduces the time and effort it takes to design and assemble products with two or more colors.**Insert spokesman name** added that "The machines are equipped with an automatic process that provides the optimal solution to the manufacturing process, resulting in less time required, increased efficiency, and improved repeatability of certain parts."**Insert brand** also provides post-sales services, ensuring that customers' machines always produce high quality and efficient output. A range of troubleshooting support, training sessions, and maintenance guidelines are provided to help workers understand how the machines work, and how to best maintain and service them.Two-color injection molding can create aesthetically pleasing and high-functioning items that appeal to a broad range of clients. The possibilities of this type of molding are endless, and companies can take advantage of technological advancements to stand out from their competitors. **Insert brand**, with its high-quality two-color injection molding machines, provides an exciting opportunity for businesses to create unique and high-quality products that are both practical and visually appealing.
Top Injection Molding Companies: Transforming the Manufacturing Industry
[Assistant]Title: Injection Molding Companies Fostering Innovation and Sustainability in Manufacturing SectorIntroduction:Injection molding has emerged as a key process in the manufacturing industry, allowing companies to produce high-quality, complex plastic components at scale. In this segment, we explore the growth and impact of injection molding companies operating in the global market, with a particular focus on the innovative practices and sustainability initiatives of one prominent industry leader: {}.(Paragraph 1)With the increasing demand for precise and efficient manufacturing techniques, injection molding companies have witnessed significant growth and their importance within the industry has surged. This expansion is primarily driven by the rising adoption of injection molding techniques in various sectors, including automotive, consumer goods, electronics, healthcare, and packaging, among others. The industry has witnessed remarkable advancements in terms of machinery, materials, and processing techniques, all of which have contributed to improved manufacturing processes.(Paragraph 2)Among these injection molding companies, {} has established itself as a frontrunner due to its commitment to delivering innovative solutions to its clients. {} has been at the forefront of introducing cutting-edge technologies and machinery, offering a range of services that meet the diverse needs of its clientele. The company's expertise lies in producing intricate plastic parts with high precision, using advanced molding techniques such as multi-cavity, insert, and overmolding.(Paragraph 3)One of the key strengths of {} lies in its capability to provide comprehensive design and engineering support to its customers from the initial concept stage to final production. This integrated approach allows the injection molding company to work closely with its clients, facilitating faster time-to-market for new products. By leveraging its extensive experience and expertise, {} helps its customers optimize design for manufacturability, reducing costs and ensuring maximum efficiency throughout the production process.(Paragraph 4)In addition to its commitment to innovation, {} has also prioritized sustainability in its operations. The company has recognized the importance of environmentally friendly manufacturing practices and has taken significant steps to minimize its carbon footprint. {} utilizes advanced materials and processes that are more sustainable, such as bio-based resins and recycling programs for waste reduction. By adopting these initiatives, {} plays a pivotal role in promoting sustainable manufacturing practices within the injection molding industry.(Paragraph 5)Another noteworthy aspect of {} is its emphasis on continuous improvement through research and development. The company invests significantly in R&D to explore emerging materials, processing techniques, and industry trends. This commitment ensures that {} remains at the forefront of technological advancements, offering its clients the most innovative and efficient solutions available.(Paragraph 6)Looking toward the future, {} aims to further expand its global presence by capitalizing on the increasing demand for injection molding services across diverse industries. With its strong focus on innovation and sustainability, the company is well-positioned to stay ahead of the competition and collaborate with clients to drive mutually beneficial growth.(Conclusion)The injection molding industry continues to flourish, propelled by advancements in technology and an increasing focus on sustainability. {} exemplifies the best practices of injection molding companies, boasting a strong commitment to innovation, sustainability, and customer satisfaction. As the industry continues to evolve, it is companies like {} that will shape the future of injection molding, shaping a more innovative, sustainable, and efficient manufacturing sector.
Enhance Production Efficiency with Tailored Graphite Molds
Custom Graphite Molds Boost Manufacturing Efficiency and PrecisionCustom graphite molds have revolutionized manufacturing industries, fuelling innovation and increasing efficiency. With high thermal conductivity, electrical conductivity, and low coefficient of thermal expansion, graphite is an excellent material for mold manufacturing. Custom graphite molds are either machined from solid blocks or fabricated by joining smaller pieces through bonding or coating.A leading supplier of custom graphite molds, located in (omitted brand name), offers a range of tailored options to suit various manufacturing needs. The company prides itself on delivering top-quality graphite products that align with customer requirements.Their skilled and experienced technicians use advanced techniques and machinery to design and manufacture highly precise and complex molds. With a commitment to quality, timeliness, and cost-effectiveness, this company has remained a leader in the graphite mold industry.Custom graphite molds are ideal for manufacturing a wide variety of products, ranging from semiconductors, electronic components, and solar cells to glass, metals, and ceramics. They are also widely used in the aerospace, medical, automotive, and defense industries.The use of custom graphite molds in such industries has resulted in increased efficiency and precision, boosting overall production output. Graphite's unique properties allow for high heat transfer, ensuring that molds remain at an optimal temperature to produce products with consistent quality.Moreover, custom graphite molds can withstand high temperatures, making them ideal for applications where other materials may fail. This property has proved especially useful in aerospace, where high-temperature and high-pressure conditions are common.Custom graphite molds also offer better surface finishes, reduce the need for complex machining, and alleviate stress on the molds and machines. Their durability reduces downtime and maintenance costs, leading to higher productivity and profitability.(omitted brand name) graphite molds come in a range of shapes, sizes, and designs, depending on the client's specifications. They can be made to produce single components or series of products. The company offers custom-designed molds for niche applications, ensuring that clients get molds tailored to their specific needs.The mold-making process comprises several stages, including prototype design, material selection, and mold creation. The company has a project team that works closely with the clients to ensure that they get the best possible molds at the most competitive rates.The team of experts uses advanced software and engineering tools to design molds that meet exact customer specifications. This process ensures that the molds are accurate and reliable, reducing waste and saving time.Furthermore, the company focuses on cost optimization, ensuring that clients get high-quality molds at the most competitive prices. They offer an excellent after-sales service, including mold repair, maintenance, and replacement.Custom graphite molds are an essential component of the manufacturing process in many industries, delivering precision and efficiency. The use of high-quality graphite molds enhances product consistency, reduces waste, and improves output. These molds provide an effective and durable solution for complex and specialized manufacturing needs.(omitted brand name) is a leading supplier of custom graphite molds, working with companies across a wide range of industries to provide bespoke solutions. Their commitment to quality, innovation, and customer satisfaction sets them apart in the graphite mold industry.
Cutting-Edge Mold Technologies Set to Revolutionize Precision Manufacturing
Precision Mold Technologies, a leading provider of mold making and engineering solutions, has announced the expansion of its services to meet the growing demand for their high-quality products. The company is committed to providing specialized services to its customers, with a focus on meeting and exceeding their expectations in terms of quality, efficiency, and cost-effectiveness. With over thirty years of experience in the industry, Precision Mold Technologies has gained a reputation for its dedication to quality and its innovative approach to mold making. The company has invested in state-of-the-art equipment and technology to ensure that it remains at the forefront of the industry and can provide the most advanced and effective solutions to its customers. The company specializes in designing and manufacturing molds for a wide range of industries, including automotive, medical, consumer products, and electronics. By using advanced software and precision equipment, the team at Precision Mold Technologies can create complex and intricate designs that meet the exact specifications of their customers. In addition to mold making, the company also provides a range of engineering solutions, including product design, prototyping, and production. Their team of experienced engineers works closely with clients to understand their requirements and provide tailored solutions that meet their specific needs. As part of their commitment to quality, Precision Mold Technologies has implemented a rigorous quality control process to ensure that every product meets the highest standards. This includes thorough testing and inspection of every mold before it is delivered to the customer. The company is also committed to sustainability and has implemented a number of measures to reduce their environmental impact. This includes using environmentally friendly materials in their molds and ensuring that their manufacturing processes are as efficient as possible. According to Precision Mold Technologies CEO, "We are excited to announce the expansion of our services to meet the growing demand for our products. Our team is dedicated to providing the highest quality solutions to our customers, and we are confident that our expanded services will further enhance our ability to meet their needs." He further added, "We are proud of our reputation as one of the leading providers of mold making and engineering solutions in the industry, and we believe that our continued investment in technology and innovation will help us maintain this position well into the future." Customers of Precision Mold Technologies have expressed their satisfaction with the company's products and services. One customer said, "Precision Mold Technologies has been our go-to provider for mold making and engineering solutions for several years. We have always been impressed with their attention to detail and their commitment to quality. We are excited to see their continued growth and expansion, and we look forward to working with them on future projects." Another customer said, "We have been working with Precision Mold Technologies for several years, and we have always been impressed with their ability to provide customized solutions that meet our specific requirements. Their team is knowledgeable and professional, and they always go above and beyond to ensure that our needs are met. We highly recommend them to anyone looking for high-quality mold making and engineering solutions." In conclusion, Precision Mold Technologies is a company that is committed to providing high-quality mold making and engineering solutions. Their dedication to quality, innovation, and sustainability has helped them become one of the leading providers in the industry. With the expansion of their services, the company is poised to continue its growth and success well into the future. Their commitment to their customers is evident in the testimonials from satisfied customers, and their investment in technology and innovation ensures that they remain at the forefront of the industry.