Maximizing Efficiency with Insert Molding Techniques
By:Admin
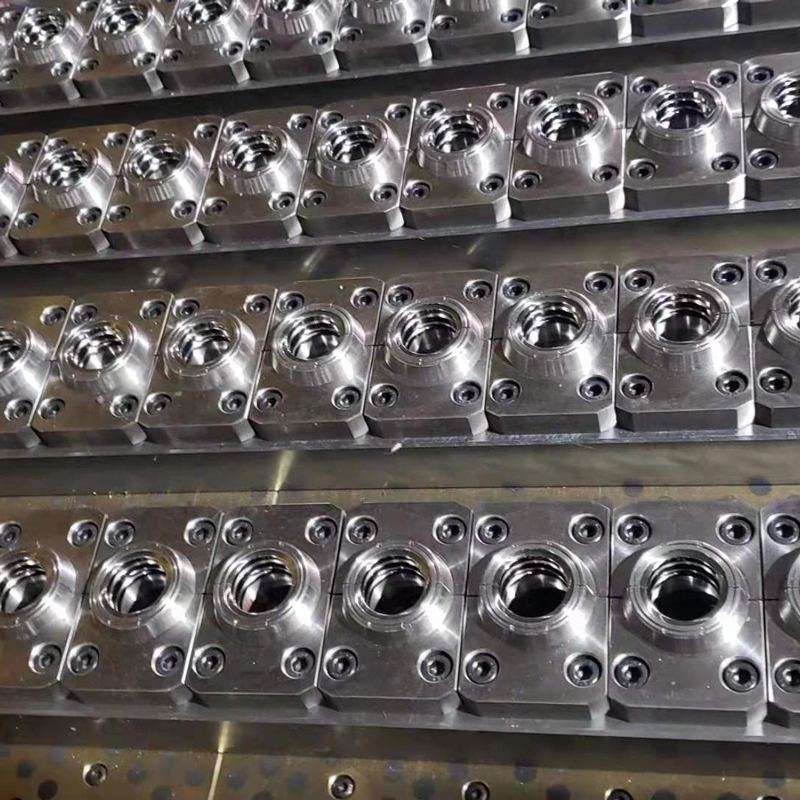
One company that specializes in insert molding is {Company}. {Company} has been a leader in the plastic injection molding industry for over 30 years. They have a state-of-the-art facility equipped with the latest technology and a team of experienced engineers and technicians who are dedicated to providing high-quality insert molding solutions to their clients.
The insert molding process begins with the design and fabrication of the mold. The mold is designed to accommodate the inserts and to allow for the flow of the molten plastic material. Once the mold is ready, the inserts are placed into the mold cavity and the plastic material is injected under high pressure. The plastic material then encapsulates the inserts, forming a strong and durable bond.
Insert molding offers several advantages over other conventional manufacturing processes. One of the main benefits is the ability to combine different materials in a single molded part, which can result in cost savings and improved product performance. Additionally, insert molding allows for the production of complex and intricate parts with consistent quality and dimensionally accurate features.
In the automotive industry, insert molding is commonly used for the production of components such as dashboard switches, electronic sensors, and interior trim pieces. By using insert molding, automotive manufacturers can reduce the number of parts and assembly steps, leading to lower production costs and improved overall vehicle quality.
In the electronics industry, insert molding is used for the production of connectors, terminals, and housings for electronic devices. The process allows for the integration of metal or plastic components into the molded parts, which can improve the overall durability and reliability of electronic products.
For consumer goods manufacturers, insert molding provides the opportunity to create innovative and aesthetically pleasing products. By incorporating different materials into the molded parts, designers can achieve unique and functional designs that stand out in the market.
{Company} has been at the forefront of insert molding technology, continuously investing in research and development to improve their process and capabilities. Their commitment to quality and innovation has earned them a reputation as a trusted partner for insert molding solutions.
The company's experienced engineering team works closely with their clients to understand their specific needs and requirements. From design and prototyping to production and assembly, {Company} provides full-service solutions to ensure that their clients receive the highest quality insert molded parts.
With a focus on precision and efficiency, {Company} utilizes advanced manufacturing techniques and quality control measures to deliver consistent and reliable products. Their dedication to excellence and customer satisfaction has allowed them to build long-term partnerships with leading companies in various industries.
As the demand for complex and multifunctional molded parts continues to grow, insert molding is expected to play a crucial role in the manufacturing industry. {Company} remains committed to staying at the forefront of insert molding technology, providing innovative solutions to meet the evolving needs of their clients.
In conclusion, insert molding is a versatile process that offers numerous benefits for a wide range of industries. When combined with the expertise and dedication of companies like {Company}, insert molding becomes a valuable tool for creating high-quality, cost-effective, and innovative products. As technology continues to advance, insert molding will continue to be a driving force in the manufacturing industry, shaping the future of product design and production.
Company News & Blog
How to Clean and Prevent Household Mold in Your Home
Household Mold Line Expands Its Services to Help Homeowners Prevent and Remove MoldAs the weather continues to shift from one extreme to the other, homeowners across the country are facing a growing problem: mold. Mold can cause a wide range of health problems, from allergies and asthma to respiratory infections and even cancer. And, because mold loves to grow in damp, humid areas, it can be very hard to prevent or get rid of it entirely.Fortunately, there is now a solution: Household Mold Line, a leading provider of mold prevention and removal services. Founded in 2012, the company has quickly become known for its effective, affordable solutions to household mold problems. And, with the recent expansion of its services, it is poised to become one of the most sought-after mold remediation companies in the industry.At its core, Household Mold Line is a family-owned and operated business that truly understands the importance of keeping homes safe and healthy. Unlike other mold remediation companies, which may use harsh chemicals or techniques that can damage your home, Household Mold Line uses only safe, environmentally-friendly products and tools to get rid of mold. This means that, not only will your home be free from mold, but you won’t have to worry about any harmful chemicals lingering behind.The company’s comprehensive services start with a thorough inspection of your home to identify any areas where mold may be hiding. From there, the team at Household Mold Line will work with you to create a customized plan to eliminate the mold and prevent it from coming back. Whether you need help with mold in your basement, bathroom, or elsewhere in your home, Household Mold Line has the expertise, tools, and resources to get the job done right.But that’s not all. In addition to its mold removal services, Household Mold Line also offers a range of preventative solutions to help keep your home mold-free. These include:- Humidity control: Humid environments are breeding grounds for mold, so Household Mold Line can install humidity control systems that will keep the air in your home dry and comfortable.- Insulation: Proper insulation can help prevent mold by reducing condensation and keeping your home’s temperature consistent. Household Mold Line can install new insulation or replace old, ineffective insulation to improve your home’s resistance to mold.- Waterproofing: If your home is prone to flooding or water damage, waterproofing can be a great way to protect your property from future mold growth. Household Mold Line can install waterproof barriers in your basement or crawlspace to prevent water intrusion and keep mold at bay.With these preventative solutions, you can rest assured that your home will be protected from mold growth for years to come.So, what sets Household Mold Line apart from other mold remediation companies? In addition to its commitment to eco-friendly solutions and high-quality workmanship, Household Mold Line is also dedicated to providing top-notch customer service. The company’s team of certified technicians will go above and beyond to ensure that you are completely satisfied with the results of their work. And, if you ever have any questions or concerns, they are always available to provide guidance and support.Overall, Household Mold Line is a company that truly cares about its customers and their well-being. Whether you are dealing with a current mold problem or simply want to prevent one from occurring, Household Mold Line has the solutions you need to keep your home healthy and safe. To learn more about the company’s services or to schedule a consultation, visit their website today.
Understanding the Benefits of Short Shot Injection Molding
Short shot injection molding is a manufacturing process that is used to create plastic parts. This process involves injecting a material, typically plastic, into a mold cavity that is not completely filled. This results in a partially filled mold, which is then allowed to cool and solidify, resulting in a part with specific properties and characteristics.The process of short shot injection molding offers several advantages. For one, it allows for the creation of parts with complex geometries and precise dimensions. This makes it an ideal process for creating intricate and detailed plastic parts, such as those used in automotive, consumer electronics, and medical devices. Additionally, short shot injection molding is a cost-effective manufacturing process, as it can produce parts in high volumes at a relatively low cost per unit.One company that has been at the forefront of short shot injection molding is {}. With a strong emphasis on innovation and quality, {} has established itself as a leader in the field of plastic injection molding. The company has a state-of-the-art manufacturing facility equipped with the latest technology and machinery, allowing them to produce high-quality plastic parts with precision and efficiency.{} has a team of experienced engineers and technicians who work closely with clients to develop custom solutions for their specific manufacturing needs. Whether it's creating prototypes, producing large volumes of parts, or optimizing the design and production process, {} is committed to delivering top-notch results that meet or exceed their clients' expectations.The company's short shot injection molding capabilities are particularly impressive, as they are able to produce parts with complex geometries and tight tolerances. Their advanced molding equipment and expertise allow them to consistently create parts with high precision and repeatability. This level of quality and reliability has earned {} a reputation for being a trusted partner in the plastic injection molding industry.In addition to their technical expertise, {} also places a strong emphasis on sustainability and environmental responsibility. They have implemented various measures to minimize waste and reduce their environmental impact, such as using recycled materials and optimizing their production processes for efficiency.Another aspect that sets {} apart is their commitment to customer satisfaction. They have a dedicated team that provides exceptional customer service and support throughout the entire manufacturing process. This includes helping clients with design and material selection, providing regular updates on production progress, and ensuring that all parts meet the highest quality standards.With their extensive experience, cutting-edge technology, and a customer-centric approach, {} continues to be a preferred choice for companies in need of short shot injection molding services. Whether it's for automotive, aerospace, medical, or consumer electronics applications, {} has the expertise and capabilities to deliver outstanding results.In conclusion, short shot injection molding is a versatile manufacturing process that offers numerous benefits, and {} has proven to be a leader in this field. With their strong focus on innovation, quality, sustainability, and customer satisfaction, {} is well-positioned to meet the growing demand for high-quality plastic parts in various industries.
Maximizing Efficiency and Quality in Injection Molding Technique
Title: Advanced TPO Injection Molding Innovations Revolutionize Manufacturing IndustryIntroduction:Leading the charge in delivering cutting-edge solutions for the manufacturing industry, [Company Name] has unveiled its latest breakthrough in TPO injection molding technology. By harnessing their expertise in engineering excellence, [Company Name] has ushered in a new era of manufacturing that promises increased efficiency, enhanced product quality, and sustainable production practices.Body:1. What is TPO Injection Molding?TPO (Thermoplastic Olefin) injection molding is a manufacturing process that utilizes advanced thermoplastic materials to create a wide range of products. It involves injecting molten TPO material into a mold cavity, which is then cooled and solidified to produce the desired product.2. Increasing Efficiency through Innovative Design:[Company Name] has successfully developed and implemented innovative designs to optimize the efficiency of TPO injection molding. By employing advanced computer-aided design and simulation software, their engineers have created molds that minimize material waste, reduce cycle times, and enhance overall production efficiency. These innovations ensure faster turnaround times and improved productivity for manufacturers.3. Enhancing Product Quality and Durability:With a strong focus on producing high-quality products, [Company Name] has pioneered the use of specialized TPO formulations, ensuring superior durability and enhanced performance. These advanced TPO materials exhibit excellent resistance to UV radiation, chemical exposure, and impact strength, making them ideal for manufacturing a diverse range of products across various industries, including automotive, aerospace, and consumer goods.4. Sustainability and Environmental Awareness:In keeping with the growing need for environmentally friendly solutions, [Company Name] has made significant efforts to incorporate sustainable manufacturing practices into their TPO injection molding processes. By sourcing TPO materials from eco-friendly suppliers and implementing recycling programs, they minimize waste and the ecological impact associated with production. This commitment to sustainability aligns with global efforts to reduce the carbon footprint of the manufacturing industry.5. Collaborative Approach to Customization:Recognizing the unique needs of each customer, [Company Name] embraces a collaborative approach to customization. Through close collaboration with clients, their team of experts assists in designing and optimizing molds specific to product requirements. This tailored approach allows manufacturers to obtain superior products that align with their vision while benefiting from [Company Name]'s technical expertise and manufacturing prowess.6. Industry-Leading Technologies and Equipment:At the heart of [Company Name]'s success lies their state-of-the-art facility, equipped with cutting-edge TPO injection molding machines. These advanced machines are designed to accommodate various product sizes, complexities, and volumes, enabling the manufacturing of both small and large-scale projects. By leveraging such advanced technologies, [Company Name] ensures high precision, accuracy, and repeatability throughout the production process.7. Continuous Innovation and Research & Development:Recognizing the importance of staying ahead in a dynamic industry, [Company Name] continually invests in research and development initiatives. Their team of skilled engineers and technicians work diligently to explore new TPO materials, refine manufacturing techniques, and develop innovative solutions that further advance the capabilities of TPO injection molding. This commitment to innovation solidifies [Company Name]'s position as a leader in the industry.Conclusion:With their groundbreaking TPO injection molding technology, [Company Name] has revolutionized manufacturing, spearheading a wave of efficiency, quality, and sustainability. By leveraging advanced design techniques, specialized materials, and cutting-edge machinery, [Company Name] drives product innovation while addressing the escalating demands of the industry. As a pioneer in TPO injection molding, they continue to push boundaries, cementing their position as a trusted partner for manufacturers worldwide.
Understanding the Process of Polyethylene Moulding
Polyethylene Moulding has been making waves in the manufacturing industry with its innovative and high-quality products. As a leading provider of polyethylene molding solutions, the company has been at the forefront of delivering innovative and sustainable solutions to its customers.With a strong focus on research and development, Polyethylene Moulding has continuously invested in cutting-edge technology and equipment to meet the evolving needs of its customers. The company's state-of-the-art manufacturing facilities allow it to produce a wide range of polyethylene products, including containers, bottles, and other custom solutions.Polyethylene Moulding takes pride in its commitment to sustainability and environmental responsibility. The company's dedication to reducing its carbon footprint has led to the development of eco-friendly products and processes. By utilizing recyclable materials and energy-efficient practices, Polyethylene Moulding has set itself apart as a leader in sustainable manufacturing.One of the key strengths of Polyethylene Moulding is its ability to provide customized solutions to its clients. The company works closely with its customers to understand their unique requirements and deliver tailored products that meet their specific needs. Whether it's a small batch of specialized containers or a large-scale production run, Polyethylene Moulding has the expertise and flexibility to handle any project.In addition to its commitment to quality and customization, Polyethylene Moulding places a strong emphasis on customer satisfaction. The company's dedicated team of professionals is always ready to assist clients with any inquiries or concerns, ensuring a smooth and hassle-free experience from start to finish.Recently, Polyethylene Moulding made headlines with the launch of its latest product line, which includes a range of innovative and sustainable packaging solutions. This new line is designed to meet the growing demand for eco-friendly packaging options, catering to businesses and consumers who are increasingly conscious of their environmental impact.The company's investment in research and development has led to the creation of cutting-edge technologies that enable the production of lightweight yet durable packaging solutions. The new product line is expected to bring about a significant shift in the market, offering customers a more sustainable alternative to traditional packaging options.“As the demand for sustainable packaging continues to grow, we are proud to introduce our latest product line that sets a new standard for eco-friendly packaging solutions,” said [Company spokesperson]. “Our goal is to provide our clients with innovative and sustainable options that not only meet their packaging needs but also contribute to a healthier planet. We believe that our new product line will be a game-changer in the industry, and we are excited to see the positive impact it will have.”Polyethylene Moulding's commitment to sustainability and innovation has not gone unnoticed, as the company has received recognition and accolades for its efforts. Its dedication to delivering high-quality, customized, and eco-friendly solutions has positioned Polyethylene Moulding as a trusted partner for businesses across various industries.Looking ahead, Polyethylene Moulding remains committed to pushing the boundaries of manufacturing excellence and sustainability. With a strong focus on research and development, the company continues to explore new opportunities to create innovative and eco-friendly products that meet the evolving needs of its clients.As the industry continues to evolve, Polyethylene Moulding stands ready to lead the way with its dedication to quality, customization, and sustainability. With a proven track record of delivering cutting-edge solutions, the company looks forward to shaping the future of the manufacturing industry and making a positive impact on the planet.
Discover the Latest Innovations in Plastic Box Molds for Improved Efficiency and Longevity
Plastic Boxes Molds - Innovating the Plastic Industry, One Mold at a TimeIn today's fast-moving world, plastic products have become an essential part of our daily lives. From packaging to storage, plastics have become the go-to material for a variety of needs. While plastic products have made our lives easier, the manufacturing process of these products is complex and requires a lot of effort. Amongst the various manufacturing processes of plastic products, plastic injection molding is one of the most popular ones. And when it comes to molds for these products, Plastic Boxes Molds has become one of the premium names in the industry.Established in the year 2010, Plastic Boxes Molds, a privately owned company based in China, has been a frontrunner in the plastic injection molding industry. The company has been making great strides over the years by serving a myriad of industries, including automotive, defense, and consumer goods. The company prides itself on being one of the best in the plastic injection molding business, with a state-of-the-art production facility spanning over 6000 square meters.Plastic Boxes Molds has made a name for itself in the industry by manufacturing a wide variety of molds, including but not limited to custom thermoplastic molds and injection molds. The company has made its mark by providing high-quality molds that are tailored to the specific needs of each client. Plastic Boxes Molds believes that the key to success is to continually innovate and evolve with the changing industry trends. As a result, Plastic Boxes Molds has made significant investments in R&D to keep up with the latest developments in the industry.The company prides itself on its ability to provide end-to-end services to its clients. The services provided by Plastic Boxes Molds cover every aspect of the plastic injection molding process, from design and engineering to the final product. The company's expertise in designing and engineering molds has made it one of the most sought-after companies in the industry.Plastic Boxes Molds has a team of highly skilled professionals who are passionate about their work. The team takes a hands-on approach to every project they undertake, ensuring that every detail is taken care of to deliver the best results. The company's commitment to excellence has garnered a loyal customer base, who have come to rely upon the expertise and quality of the molds provided by Plastic Boxes Molds.Apart from its commitment to excellence, another aspect that sets Plastic Boxes Molds apart from its competition is its use of cutting-edge technology. The company has made significant investments in machinery and equipment, ensuring that the molds created are of the highest quality. The use of advanced technology has also allowed Plastic Boxes Molds to provide faster turnaround times to its clients, ensuring that projects are completed on time.In conclusion, Plastic Boxes Molds has become a prominent name in the plastic injection molding industry owing to its commitment to innovation, excellence, and use of advanced technology. The company's dedication to providing end-to-end services has made it a one-stop-shop for clients looking for custom molds. With its skilled team, state-of-the-art production facility, and ability to keep up with the latest developments in the industry, Plastic Boxes Molds is poised to continue its success story and innovate the plastic industry, one mold at a time.
Ultimate Guide to Overmolding and Insert Molding for Manufacturing Processes
Overmolding Insert Molding is a cutting-edge manufacturing process that has been gaining significant attention in various industries. This process involves combining two different materials to create a single product with enhanced functionality and durability. By utilizing this advanced technique, companies are able to produce high-quality parts and components that meet the specific requirements of their customers.One of the leading companies at the forefront of Overmolding Insert Molding is {}. With a strong focus on innovation and precision engineering, the company has established itself as a key player in the manufacturing and production industry. By incorporating Overmolding Insert Molding into their operations, they have been able to offer a wide range of custom solutions to their clients across the globe.This advanced manufacturing process allows {}. to create complex and intricate designs that were previously not possible with traditional molding techniques. By overmolding a variety of materials such as plastics, metals, and rubber, the company is able to produce components that are not only durable and reliable but also aesthetically pleasing. This level of versatility and flexibility has set them apart in the industry, allowing them to cater to a diverse clientele with varying needs and specifications.One of the key advantages of Overmolding Insert Molding is the ability to incorporate multiple functions into a single component. This means that {}. can produce parts that serve a dual purpose, reducing the overall number of components required in a product and ultimately saving on manufacturing costs. Additionally, the overmolded parts are known for their superior strength and resilience, making them suitable for use in demanding applications across several industries.Another benefit of Overmolding Insert Molding is its ability to create a seamless and integrated product. By fusing different materials together, the company can eliminate the need for additional assembly and welding processes, resulting in a more streamlined and efficient production cycle. This not only results in cost savings but also reduces the overall lead time for manufacturing, allowing for a quicker turnaround for their clients.In terms of applications, Overmolding Insert Molding has been widely adopted in industries such as automotive, electronics, consumer goods, and medical devices. The ability to combine materials with varying properties has opened up new possibilities for product design and functionality, allowing companies to stay ahead of the curve in their respective markets. By leveraging this advanced manufacturing process, {}. has been able to stay at the forefront of innovation and offer their clients cutting-edge solutions that set them apart from the competition.Looking ahead, the future of Overmolding Insert Molding looks promising, with advancements in materials and technology continuing to drive the evolution of this manufacturing process. As companies continue to demand high-performance components with complex designs, it is clear that Overmolding Insert Molding will play a pivotal role in meeting these requirements. {}. is well-positioned to lead the way in this space, leveraging their expertise and capabilities to continue delivering exceptional products to their clients.In conclusion, Overmolding Insert Molding has revolutionized the manufacturing industry, offering a myriad of benefits that have redefined product design and production. {}. has been a driving force in embracing this advanced manufacturing process, and their commitment to innovation has solidified their position as a leader in the industry. With the continued evolution of Overmolding Insert Molding, there is no doubt that the company will continue to push the boundaries of what is possible in the realm of manufacturing.
Durable and efficient hot runner mold for precision injection molding
Hot Runner Mold, a leader in the plastic injection molding industry, is proud to announce the launch of their latest innovative product. With over 20 years of experience in the industry, Hot Runner Mold has become a trusted name for high-quality, reliable products. The company has a strong focus on research and development, and their team of experts are constantly working to improve their products and introduce new, cutting-edge solutions to the market.The latest product from Hot Runner Mold is a hot runner system that is designed to deliver superior performance and precision in plastic injection molding. This new system offers a range of benefits, including faster cycle times, reduced waste, and improved mold quality. It is built with state-of-the-art technology and is compatible with a wide range of plastic materials, making it an ideal choice for a variety of molding applications.One of the key features of the new hot runner system is its advanced temperature control capabilities. This allows for precise control of the temperature in each individual nozzle, ensuring that the plastic material is heated and cooled at the optimal rate for excellent molding results. In addition, the system also offers improved flow control, allowing for more efficient filling of the mold cavities and reducing the likelihood of defects in the finished products.The new hot runner system from Hot Runner Mold also boasts a user-friendly design, making it easy to install and operate. It is equipped with intuitive controls and a user-friendly interface, allowing for quick and easy setup and adjustment. This design also makes it simple to maintain and service, reducing downtime and increasing productivity for plastic injection molding operations.In addition to the launch of their new hot runner system, Hot Runner Mold also offers a range of other products and services to support the plastic injection molding industry. These include a comprehensive range of hot runner components, such as nozzles, manifolds, and heaters, as well as a variety of mold maintenance and repair services. The company also provides expert technical support and consultation to help customers get the most out of their molding operations.Hot Runner Mold has built a solid reputation based on their unwavering commitment to quality, reliability, and customer satisfaction. They strive to exceed the expectations of their customers by delivering products and services that meet the highest standards of performance and durability. The company has a strong focus on fostering long-term relationships with their customers, working closely with them to understand their specific needs and provide tailored solutions that address their unique challenges.With the launch of their new hot runner system, Hot Runner Mold continues to demonstrate their leadership and innovation in the plastic injection molding industry. They are dedicated to pushing the boundaries of technology and delivering products that empower their customers to achieve new levels of excellence in their molding operations. For businesses looking to improve their molding processes and achieve superior results, Hot Runner Mold is the trusted partner for innovative solutions and unmatched expertise.
Growing Demand and Opportunities in the Injection Molding Industry Revealed by Latest News
[News Title]Injection Molding Industry Experiences Robust Growth Amid Technological Advancements[News Content]The injection molding industry has witnessed tremendous growth in recent years, thanks to the continuous advancements in technology. With the ability to produce complex and intricate parts with high precision and efficiency, injection molding has become a cornerstone in various sectors, ranging from automotive and packaging to electronics and healthcare.One of the leading players in this industry is a renowned company () that has been at the forefront of manufacturing top-quality injection molding machines. With its commitment to innovation and customer satisfaction, the company has revolutionized the industry and has played a pivotal role in its expansion.Established over two decades ago, () has carved a niche for itself by providing state-of-the-art injection molding machines tailored to meet diverse customer needs. Their machines offer exceptional durability and reliability while providing excellent performance and productivity. () has earned a stellar reputation for delivering top-notch products and exceptional customer service.Furthermore, the company's dedication to research and development has empowered them to continuously enhance their machinery's capabilities. By investing in the latest technologies and incorporating advanced features, () has been able to offer cutting-edge solutions that meet the ever-evolving demands of the injection molding industry.The injection molding industry has seen a surge in demand due to its ability to manufacture complex components with precision, reduce production costs, and streamline processes. () has played a critical role in this growth by providing manufacturers with high-quality and efficient machinery that ensures accurate and consistent production.The automotive industry has been a significant contributor to the expansion of the injection molding sector. With the growing demand for lightweight and eco-friendly vehicles, manufacturers are increasingly relying on injection molding techniques to produce various interior and exterior components. The machines provided by () have been instrumental in helping automotive manufacturers meet these demands, thanks to their precision, speed, and energy efficiency.Moreover, the packaging industry has also experienced a boost from the injection molding advancements. The ability to manufacture intricate and customized packaging solutions has bolstered the growth of this sector. Companies in the packaging industry are now able to produce durable, lightweight, and appealing packaging solutions using injection molding techniques. ()'s machines have played a vital role in enhancing the productivity and efficiency of packaging manufacturers, enabling them to cater to the evolving consumer preferences.The electronics industry has also relied heavily on injection molding to produce intricate and precise components required for various electronic devices. The miniaturization of electronic devices has necessitated the production of smaller and more intricate parts, making injection molding a preferred choice. () has provided manufacturers in the electronics industry with machines capable of producing high-precision components efficiently, creating a positive impact on their production capabilities.Furthermore, the healthcare sector has benefited immensely from injection molding techniques. The ability to produce sterile and high-quality medical devices and equipment has improved patient care and safety. ()'s state-of-the-art injection molding machines have been pivotal in facilitating the production of medical components while adhering to stringent quality control measures.The growing demand for quality goods coupled with the continuous advancements in the injection molding industry has positioned () as a leading player in the global market. With strong customer focus, technological expertise, and a commitment to innovation, () is set to empower manufacturers in different industries to achieve their production goals efficiently and sustainably.In conclusion, the injection molding industry is experiencing significant growth due to the continuous advancements in technology. Companies like () have played a vital role in revolutionizing the industry by providing innovative and high-quality machinery. With the ability to produce complex and precise components, injection molding has become an integral part of various sectors, including automotive, packaging, electronics, and healthcare. ()'s commitment to research and development, along with their exceptional customer service, has solidified their position as a prominent player in the global injection molding market.
Understanding the Process of Injection Blow Molding
Injection Blow Molding (IBM) is a manufacturing process used to produce hollow plastic parts. It is widely utilized in various industries such as packaging, automotive, and medical devices. The process involves injecting melted thermoplastic resin into a mold cavity to form a parison. Then, a blow pin is inserted into the parison to inflate and form the hollow part.In recent years, the demand for high-quality plastic products has been on the rise, driving the adoption of advanced manufacturing technologies like Injection Blow Molding. One company that has been at the forefront of IBM technology is {}. With state-of-the-art facilities and a team of experienced professionals, they have established themselves as a leading provider of Injection Blow Molding solutions.{} has a proven track record of delivering innovative and reliable IBM products to their clients. They offer a wide range of services including designing, prototyping, and production of custom molds for various applications. The company's commitment to quality and customer satisfaction has earned them a loyal customer base and a solid reputation in the industry.One of the key advantages of Injection Blow Molding is its ability to produce complex and precise parts with high accuracy and repeatability. With the use of advanced technology and extensive expertise, {} is able to meet the strictest tolerances and quality standards required by their customers. This allows them to cater to the diverse needs of different industries, including pharmaceutical packaging, personal care products, and automotive components.Furthermore, {}. has been investing in continuous research and development to enhance their IBM capabilities. By staying ahead of the curve, they are able to offer cutting-edge solutions to their clients, enabling them to stay competitive in their respective markets. The company's commitment to innovation and technological advancement has been a driving force behind their success.Another strength of {} lies in their focus on sustainability and environmental responsibility. They have implemented eco-friendly practices in their manufacturing processes, such as using recycled materials and optimizing energy efficiency. By doing so, they are able to minimize their impact on the environment while providing sustainable solutions to their customers.In addition to their impressive technical capabilities, {}. takes pride in their commitment to exceptional customer service. Their team of experts works closely with clients throughout the entire manufacturing process, from initial concept to final product delivery. They understand the importance of clear communication and collaboration to ensure that the end result meets or exceeds the client's expectations.Looking ahead, {}. is poised for continued growth and success in the field of Injection Blow Molding. With a strong focus on quality, innovation, and customer satisfaction, they are well-positioned to capitalize on the growing demand for high-quality plastic products. Their dedication to excellence and continuous improvement sets them apart as a top-tier provider of IBM solutions.In conclusion, Injection Blow Molding is a crucial manufacturing process that plays a pivotal role in the production of various plastic parts. {}. has demonstrated leadership in this field, delivering superior IBM solutions to a diverse range of industries. With their technical expertise, commitment to sustainability, and dedication to customer service, they are well-equipped to meet the evolving needs of the market and continue their success in the years to come.
Discover the Cost of Injection Moulding Dies: A Comprehensive Guide
Injection Moulding Die Cost: An Overview of the Factors InvolvedManufacturing companies all over the world use injection moulding as one of their primary manufacturing techniques. Whether it is automotive, medical, or consumer goods, injection moulding is widely used due to its high efficiency and precision. Injection moulding die is a key component of any injection moulding operation. It is the device that shapes plastic pellets or granules into a finished product.However, the cost of injection moulding dies can vary depending on several factors such as design, size, complexity, material, and finishing. In this article, we will discuss the various factors that impact injection moulding die costs.Factors that Impact Injection Moulding Die CostsDesignThe design of the injection moulding die is one of the primary factors that impacts the cost. A complicated and intricate design would require more engineering time, ultimately increasing the overall cost. On the other hand, a simple design would require less engineering time and would be more cost-effective.SizeThe size of the injection moulding die plays a significant role in determining its cost. Larger dies would require more material and energy during production, increasing the overall cost. The complexity of the design would also increase with the size of the die, ultimately impacting the final cost.ComplexityThe complexity of the injection moulding die determines the amount of detail required in the design and manufacturing process. A more intricate design requires more sophisticated manufacturing techniques, ultimately resulting in a higher cost.MaterialThe material used to manufacture the injection moulding die also impacts the final cost. Aluminium is a popular choice for injection moulding dies as it is cheaper, faster, and easier to manufacture. However, it is not as durable as steel and requires frequent replacement. Steel is a more expensive option, but it is more durable and can typically withstand higher temperature and pressure.FinishingThe finishing of the injection moulding die is also a factor that affects the cost. Depending on the desired finish, additional processes such as polishing or texturing may be required, ultimately increasing the overall cost.How to Reduce Injection Moulding Die Costs1. Simplify the DesignAs previously mentioned, the design of the injection moulding die plays a significant role in determining its cost. Simplifying the design can reduce the complexity of the manufacturing process and ultimately reduce the cost.2. Use the Right MaterialChoosing the right material for the injection moulding die can have a significant impact on the cost. Using aluminium instead of steel may be a better choice for simple products that require short production runs. On the other hand, using steel may be a better option for more complex products that require a higher degree of durability.3. Consider the Lifecycle of the DieConsider the lifecycle of the injection moulding die when making decisions about its production. The cost of the die is not just the upfront cost but also the cost of maintenance, repair, and replacement over its lifetime. A more expensive steel die may have a longer lifespan and require less frequent replacement, ultimately making it the more cost-effective option in the long run.ConclusionInjection moulding is a widely-used manufacturing technique that allows for high efficiency and precision. The cost of the injection moulding die can vary depending on several factors such as design, size, complexity, material, and finishing. However, by simplifying the design, using the right material, and considering the lifecycle of the die, manufacturers can reduce the overall cost and increase profitability. Ultimately, it is important to consider the cost-benefit analysis of the injection moulding die to ensure that the final product meets the required specifications at a cost-effective price.