New Pre-Deformation Mold Technology Enhances Manufacturing Process
By:Admin
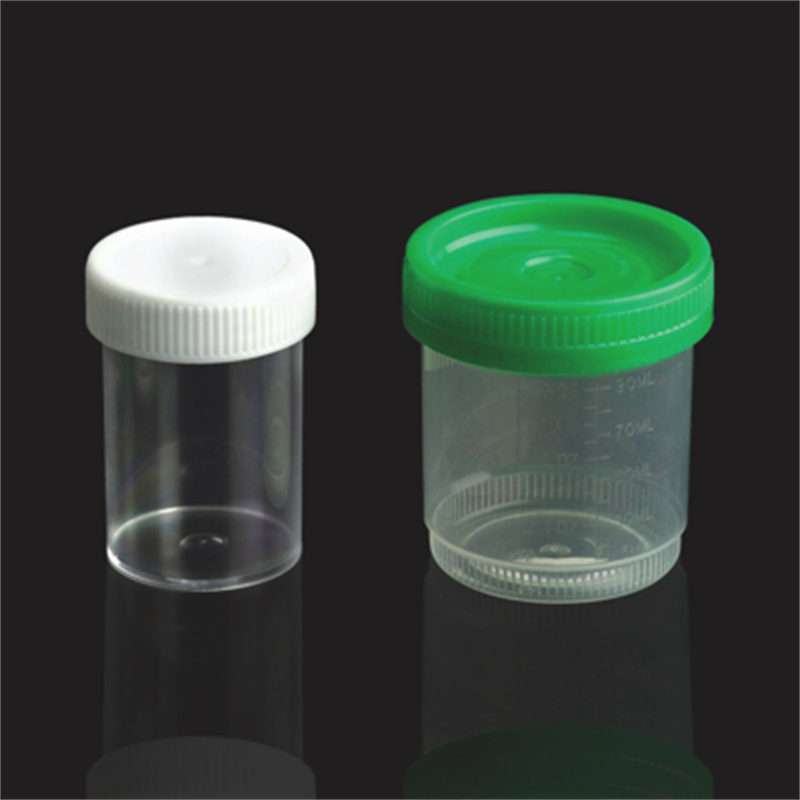
In the highly competitive manufacturing industry, staying ahead of the curve and constantly innovating is crucial for success. One company that is leading the way in this regard is Pre-Deformation Mold, who has recently unveiled a groundbreaking new technology that is set to revolutionize the industry.
Pre-Deformation Mold, a leading manufacturer of high-quality molds and tooling solutions, has long been known for their commitment to innovation and their ability to push the boundaries of what is possible in the industry. With their latest technological breakthrough, they are once again proving that they are at the forefront of manufacturing innovation.
The new technology, which the company has developed in collaboration with leading experts in the field, is based on a revolutionary pre-deformation process that allows for the creation of highly complex and precise molds and tooling solutions. By incorporating this innovative process into their manufacturing methods, Pre-Deformation Mold is able to produce molds and tooling solutions that are not only of the highest quality, but also far more efficient and cost-effective than traditional methods.
This cutting-edge technology represents a significant leap forward for the industry, and is set to have a major impact on a wide range of manufacturing applications. With the ability to create molds and tooling solutions that were previously thought to be impossible to achieve, manufacturers will now have the opportunity to bring even the most ambitious and complex designs to life. This will not only open up new possibilities for product development, but also allow for greater innovation and creativity across the board.
In addition to the benefits it offers in terms of design capabilities, the new technology from Pre-Deformation Mold also promises to deliver significant improvements in efficiency and cost-effectiveness. By streamlining the manufacturing process and reducing the need for expensive and time-consuming secondary operations, manufacturers will be able to produce high-quality molds and tooling solutions at a fraction of the cost and time it would have previously taken.
The unveiling of this new technology is a testament to Pre-Deformation Mold's commitment to innovation and their dedication to pushing the boundaries of what is possible in the manufacturing industry. By investing in research and development and working closely with industry experts, the company has once again demonstrated their ability to stay ahead of the curve and lead the way in driving innovation and progress within the industry.
With this groundbreaking technology now available, manufacturers can look forward to a future where the only limitation on what is possible is their imagination. Pre-Deformation Mold's innovative approach to manufacturing has once again set the bar for the industry, and their new technology is sure to shape the future of manufacturing for years to come.
As Pre-Deformation Mold continues to push the boundaries of what is possible in the industry, it is clear that they are a company to watch. With their commitment to innovation and their track record of delivering cutting-edge solutions, they are setting the stage for a future where anything is possible in the world of manufacturing.
Company News & Blog
Injection Molding: Key Information and Latest Updates
Smc Injection Molding Company announced today that they are merging with a leading injection molding company, further solidifying their position as a top player in the industry. The merger, which has been in the works for several months, is expected to create a powerhouse in the injection molding sector, with a combined market share that will be tough for competitors to beat.The newly merged company, which will operate under the name Smc Injection Molding, will bring together the best of both organizations, including their expertise, technology, and client base. With a track record of success and industry-leading expertise, the new entity is poised to lead the way in injection molding solutions for a wide range of industries.In a statement, the CEO of Smc Injection Molding remarked, "This merger represents a significant milestone for our company. By combining our resources, knowledge, and talent, we are positioning ourselves for continued success in the injection molding market. We are excited about the opportunities that lie ahead and are confident that this merger will bring tremendous value to our customers and stakeholders."The company, founded in 1998, has grown steadily over the years, gaining a reputation for delivering high-quality injection molding solutions to a diverse client base. Their state-of-the-art manufacturing facility is equipped with the latest technology and equipment, allowing them to meet the most demanding client requirements.Over the years, the company has established itself as a trusted partner for businesses in various industries, including automotive, consumer goods, electronics, and medical devices. Their commitment to quality, innovation, and customer satisfaction has earned them a loyal client base and has cemented their position as a leader in the injection molding space.The merger with the leading injection molding company represents a strategic move for Smc Injection Molding, enabling them to expand their capabilities and offer an even broader range of solutions to their clients. The combined expertise of the two companies will enable them to take on more complex projects, tackle new markets, and drive innovation in the injection molding industry.As part of the merger, the company will be integrating their operations, streamlining processes, and leveraging their collective resources to drive efficiency and maximize value for their clients. They will also be investing in research and development to stay at the forefront of industry trends and technological advancements.The newly merged company is committed to upholding the highest standards of quality, safety, and environmental responsibility in all aspects of their operations. They will continue to focus on delivering innovative solutions that meet the evolving needs of their customers while maintaining a strong commitment to sustainability and corporate social responsibility.In conclusion, the merger between Smc Injection Molding and the leading injection molding company represents an exciting new chapter for the company. With a combined wealth of expertise and resources, the newly merged entity is well-positioned to drive innovation, deliver exceptional value to its clients, and lead the way in the injection molding industry. This move is expected to further strengthen the company's position as a top player in the market and pave the way for continued growth and success in the years to come.
High-Quality Non-Recycled Case Moulds: A Sustainable Solution for Manufacturing
Non-Recycled Case Mould Revolutionizing Plastic Moulding IndustryWith the increasing awareness of environmental protection and sustainable development, the plastic moulding industry is striving to reduce its carbon footprint. This is where the Non-Recycled Case Mould, developed by [Company Name], comes into play. This innovative moulding technology is setting new standards in the industry by offering a sustainable and eco-friendly alternative to traditional plastic moulding processes.[Company Name] is a leading manufacturer of plastic moulds, with a successful track record of delivering high-quality products to a global customer base. The company's commitment to innovation and sustainability has led to the development of the Non-Recycled Case Mould, a breakthrough technology that is revolutionizing the way plastic products are manufactured.The Non-Recycled Case Mould is a game-changer in the industry, as it eliminates the need for using recycled plastic materials in the moulding process. Traditional plastic moulding often relies on recycled plastics, which can compromise the quality and durability of the final product. With the Non-Recycled Case Mould, [Company Name] is able to produce high-quality plastic products using virgin materials, resulting in products that are stronger, more durable, and of higher quality.In addition to delivering superior quality products, the Non-Recycled Case Mould also has a positive impact on the environment. By using virgin materials, the moulding process reduces the reliance on recycled plastics, which can be energy-intensive and produce harmful emissions. This innovative approach not only ensures the production of high-quality, durable products but also minimizes the environmental impact of the manufacturing process.Furthermore, the Non-Recycled Case Mould is designed to be highly efficient, offering faster cycle times and reduced waste in the production process. This not only improves the overall productivity and cost-effectiveness of the manufacturing process but also contributes to a more sustainable and eco-friendly operation.[Company Name] is dedicated to promoting sustainability and environmental responsibility, and the development of the Non-Recycled Case Mould is a testament to this commitment. By offering a solution that reduces the reliance on recycled plastics, the company is contributing to the global effort to minimize the environmental impact of plastic manufacturing.The Non-Recycled Case Mould is a testament to [Company Name]'s dedication to innovation and sustainability. By offering a sustainable alternative to traditional plastic moulding processes, the company is setting new standards in the industry and leading the way towards a more sustainable future for plastic manufacturing.In conclusion, the Non-Recycled Case Mould developed by [Company Name] is a groundbreaking technology that is revolutionizing the plastic moulding industry. By offering a sustainable and eco-friendly alternative to traditional plastic moulding processes, the company is setting new standards in the industry and leading the way towards a more sustainable future for plastic manufacturing. With its commitment to innovation and sustainability, [Company Name] is making a significant impact on the industry, and the Non-Recycled Case Mould is a testament to the company's dedication to environmental responsibility.
Understanding the Process of Manifold Injection Molding
Manifold Injection Molding Technology Revolutionizes Manufacturing ProcessesIn recent years, the manufacturing industry has been revolutionized by the introduction of innovative technologies and processes, and one of the most significant advancements has been the development of manifold injection molding technology. This cutting-edge manufacturing technique has enabled companies to produce high-quality, complex plastic parts with greater efficiency and precision than ever before.Manifold injection molding is a process that involves the use of a specially designed manifold system to inject plastic material into a mold cavity. This technology allows for the simultaneous injection of multiple materials, colors, or components, resulting in the production of intricate and integrated parts. The manifold system ensures a uniform distribution of materials, leading to improved product quality and consistency.One company that has been at the forefront of this technological advancement is {}. With decades of experience in the plastic injection molding industry, {} has been a pioneer in the development and implementation of manifold injection molding technology. Their state-of-the-art facilities and dedicated team of engineers have allowed them to deliver innovative manufacturing solutions to a wide range of industries, including automotive, consumer electronics, and medical devices.{}'s manifold injection molding technology has set new standards for quality, efficiency, and cost-effectiveness in plastic part production. By leveraging the capabilities of their advanced machinery and proprietary processes, they have been able to achieve remarkable results for their clients, including reduced lead times, lower production costs, and improved product performance.One of the key advantages of manifold injection molding is its ability to streamline the manufacturing process by combining multiple steps into a single operation. This not only results in time and cost savings but also enhances the overall design flexibility and functionality of the final product. By integrating different materials or components in a single mold, manufacturers can create parts with unique features and properties that were previously unattainable with traditional molding processes.Another significant benefit of manifold injection molding is its ability to minimize material waste and optimize production efficiency. With the precise control and distribution of materials provided by the manifold system, manufacturers can reduce scrap and improve the overall yield of usable parts. This level of efficiency is particularly valuable in high-volume production scenarios, where small improvements in material utilization can lead to substantial cost savings over time.In addition to its technical advantages, manifold injection molding offers environmental benefits by reducing the overall carbon footprint of manufacturing operations. By optimizing the use of raw materials and energy, this technology contributes to sustainable and eco-friendly production practices, aligning with the growing global demand for environmentally responsible manufacturing solutions.As the demand for high-quality, complex plastic parts continues to grow across various industries, manifold injection molding is expected to play a pivotal role in shaping the future of manufacturing. Its ability to deliver superior product quality, cost efficiency, and design flexibility makes it a compelling choice for businesses seeking to stay ahead in the competitive global market.With a proven track record of success and a dedication to continuous innovation, {} is well-positioned to lead the way in advancing manifold injection molding technology and delivering exceptional value to its clients. As the industry continues to evolve, it is evident that manifold injection molding will remain a driving force in the ongoing transformation of manufacturing processes, setting new standards for performance and reliability in the production of plastic parts.
Discover the Benefits of Multi-Cavity Spoon Molds for Efficient Production
Multi-Cavity Spoon Molds Revolutionize Spoon Production for the Food IndustryThe demand for efficient and cost-effective production of food-grade spoons has been on the rise, and plastic injection molding has provided a reliable solution to this demand. Rather than using traditional cutlery, many consumers opt for disposable spoon options that are both hygienic and convenient. As such, the production of spoons that meet the high standards of the food industry has become a crucial aspect of many manufacturing companies.Enter the Multi-Cavity Spoon Molds, a product that has revolutionized spoon production for the food industry. In an industry where efficiency, reliability, and compliance are essential, these molds provide the perfect solution by streamlining the spoon production process.Multi-Cavity Spoon Molds are, as the name suggests, molds that allow multiple spoons to be produced at once, thus increasing production efficiency. They come in different variations depending on design specifications, with the molds allowing for the production of spoons with varying lengths, widths, and shapes. By incorporating multiple cavities in a single mold, manufacturers can increase their production output, reduce lead times, and ultimately save on costs.The use of multi-cavity spoon molds has been widely accepted by the food industry, with numerous companies now using the molds to produce millions of spoons daily. One such company that has taken advantage of this technology is *** (brand name removed), which specializes in the manufacturing of food-grade plastic spoons. The company boasts of being one of the leading plastic injection molding companies in the world, with years of experience in the production of high-quality disposable plastic products.*** (brand name removed) prides itself on using the latest technology to produce high-quality plastic spoons for various food industries, from fast-food chains to the hospitality industry. The company is constantly looking for innovative solutions to improve its production processes, and the multi-cavity spoon molds have been one of the key technologies that have helped the company achieve this goal.The multi-cavity spoon molds used by *** (brand name removed) are designed using high-quality materials to ensure they can withstand the harsh environment of the food industry. They are designed to be easy to use, with simple-to-follow procedures that allow machines to produce large quantities of spoons with minimal human intervention. The molds have also proven to be user-friendly, with companies being able to easily adapt them to their specific manufacturing needs.The benefits of using multi-cavity spoon molds are many. One of the most significant benefits is the increase in production efficiency. The molds have enabled manufacturers to produce large quantities of spoons daily, thus reducing lead times and ultimately increasing productivity. This has resulted in a significant reduction in production costs for companies such as *** (brand name removed), making them more competitive and profitable.Another significant benefit is the increase in the consistency and quality of produced spoons. Multi-cavity spoon molds have allowed for the production of spoons that are uniform in shape, size, and thickness, meeting the high standards of the food industry. These molds also enable manufacturers to produce spoons that meet specific design specifications, making them ideal for use in food packaging and dispensing systems.The use of multi-cavity spoon molds has also contributed to the reduction of waste materials in the plastic injection molding process. By producing multiple spoons at once, the number of failed pieces is significantly reduced, thus minimizing the amount of plastic waste generated in the production process. This makes the process more environmentally friendly and cost-effective.In conclusion, the use of multi-cavity spoon molds has revolutionized spoon production in the food industry. It has enabled manufacturers such as *** (brand name removed) to increase their production output, improve the quality and consistency of their products, reduce waste materials, and ultimately save on costs. With this technology, it is safe to say that the production of high-quality, food-grade spoons has never been easier, cost-effective, or more efficient.
Top Plastic Molding Pellets Manufacturers in China
China Plastic Molding Pellets Manufacturers has recently announced their latest advancements in the manufacturing and production of high-quality plastic molding pellets. With a focus on innovation and sustainability, the company has become a leading player in the global market, providing top-notch products to a wide range of industries.As a leading manufacturer of plastic molding pellets, China Plastic Molding Pellets Manufacturers takes great pride in their ability to produce superior products that meet the highest standards of quality and performance. The company's state-of-the-art production facilities are equipped with the latest technology and machinery, allowing them to produce a wide range of plastic molding pellets with precision and efficiency.One of the key factors that sets China Plastic Molding Pellets Manufacturers apart from other manufacturers is their commitment to sustainability. The company places a strong emphasis on environmental responsibility, ensuring that their manufacturing processes are as eco-friendly as possible. This includes the use of recycled materials and implementing energy-efficient practices to minimize their carbon footprint.In addition to their dedication to sustainability, China Plastic Molding Pellets Manufacturers also prioritizes innovation and technological advancement. The company continuously invests in research and development to improve their products and processes, staying ahead of the curve in an ever-evolving industry. This commitment to innovation has allowed them to develop cutting-edge plastic molding pellets that meet the diverse needs of their customers.Furthermore, China Plastic Molding Pellets Manufacturers has built a strong reputation for reliability and customer satisfaction. With a focus on customer-centric values, the company strives to provide exceptional service and support to their clients, ensuring that their needs are met with professionalism and expertise. This has cemented their position as a trusted partner for businesses across various industries.The plastic molding pellets manufactured by China Plastic Molding Pellets Manufacturers are utilized in a wide range of applications, from automotive and consumer goods to packaging and construction. The versatility and high performance of their products have made them a preferred choice for businesses looking for reliable and cost-effective solutions for their plastic molding needs.Looking towards the future, China Plastic Molding Pellets Manufacturers remains committed to pushing the boundaries of innovation and sustainability in the manufacturing industry. With a focus on quality, reliability, and customer satisfaction, the company is poised to continue leading the way in the global market for plastic molding pellets.In conclusion, China Plastic Molding Pellets Manufacturers has established itself as a premier manufacturer of high-quality plastic molding pellets, with a strong focus on innovation, sustainability, and customer satisfaction. With their cutting-edge production facilities and a commitment to excellence, the company is well-equipped to meet the evolving needs of industries worldwide. As they continue to push the boundaries of what is possible, China Plastic Molding Pellets Manufacturers is set to maintain their position as a leading player in the global market for plastic molding pellets.
High-Quality PET Preform Molds for Efficient Production Processes
PET Preform Molds are vital tools in the production of PET preforms, which are used in the manufacturing of plastic bottles, containers, and other packaging materials. These molds play a crucial role in shaping the preforms into the desired form before they are blown into the final product.One company that has been at the forefront of producing high-quality PET Preform Molds is {}. With years of experience and expertise in the industry, they have established themselves as a leading manufacturer of molds for the PET packaging industry.Founded in {}, the company has consistently strived to innovate and develop advanced molding solutions to meet the growing demand for PET packaging products. Their state-of-the-art manufacturing facilities and cutting-edge technology have enabled them to deliver molds that are not only of superior quality but also highly efficient and durable.The company's PET Preform Molds are designed to ensure precision and consistency in the molding process, resulting in preforms that meet the highest standards of quality and performance. Their molds are customizable to cater to the specific requirements of their clients, allowing for flexibility in design and production.In addition to their standard mold designs, the company also offers custom mold development services, working closely with clients to create molds that are tailored to their unique specifications. This dedication to meeting the individual needs of their customers sets them apart in the industry and has earned them a reputation for excellence and reliability.Furthermore, {} places great emphasis on the use of high-quality materials in the production of their molds. They understand the importance of durability and longevity in the molds used for PET preform production, and as such, they ensure that only the best materials are utilized in their manufacturing process.The company also prides itself on its commitment to continuous improvement and innovation. They have a dedicated team of engineers and technicians who are constantly researching and developing new technologies and techniques to enhance their mold design and production processes. This dedication to innovation has allowed them to stay ahead of the competition and provide their clients with cutting-edge molding solutions.In addition to their technical expertise, the company also places a strong emphasis on customer service. They understand the fast-paced and demanding nature of the PET packaging industry and, therefore, strive to provide their clients with prompt and efficient service. Their team is always ready to provide support and assistance to ensure that their clients' production processes run smoothly and efficiently.As awareness of environmental issues continues to grow, the demand for sustainable packaging solutions has increased. In response to this, {} has also developed molds that are compatible with the production of eco-friendly PET packaging products. By offering molds that can be used in the production of recyclable and biodegradable packaging materials, they are contributing to the global effort to reduce plastic waste and promote sustainability.In conclusion, {} has established itself as a leading manufacturer of PET Preform Molds, delivering high-quality, customizable, and innovative solutions to meet the diverse needs of the PET packaging industry. With a commitment to excellence, sustainability, and customer satisfaction, they continue to be a trusted partner for companies looking to enhance their PET preform production processes.
Discover the Latest Innovations in Plastic Box Molds for Improved Efficiency and Longevity
Plastic Boxes Molds - Innovating the Plastic Industry, One Mold at a TimeIn today's fast-moving world, plastic products have become an essential part of our daily lives. From packaging to storage, plastics have become the go-to material for a variety of needs. While plastic products have made our lives easier, the manufacturing process of these products is complex and requires a lot of effort. Amongst the various manufacturing processes of plastic products, plastic injection molding is one of the most popular ones. And when it comes to molds for these products, Plastic Boxes Molds has become one of the premium names in the industry.Established in the year 2010, Plastic Boxes Molds, a privately owned company based in China, has been a frontrunner in the plastic injection molding industry. The company has been making great strides over the years by serving a myriad of industries, including automotive, defense, and consumer goods. The company prides itself on being one of the best in the plastic injection molding business, with a state-of-the-art production facility spanning over 6000 square meters.Plastic Boxes Molds has made a name for itself in the industry by manufacturing a wide variety of molds, including but not limited to custom thermoplastic molds and injection molds. The company has made its mark by providing high-quality molds that are tailored to the specific needs of each client. Plastic Boxes Molds believes that the key to success is to continually innovate and evolve with the changing industry trends. As a result, Plastic Boxes Molds has made significant investments in R&D to keep up with the latest developments in the industry.The company prides itself on its ability to provide end-to-end services to its clients. The services provided by Plastic Boxes Molds cover every aspect of the plastic injection molding process, from design and engineering to the final product. The company's expertise in designing and engineering molds has made it one of the most sought-after companies in the industry.Plastic Boxes Molds has a team of highly skilled professionals who are passionate about their work. The team takes a hands-on approach to every project they undertake, ensuring that every detail is taken care of to deliver the best results. The company's commitment to excellence has garnered a loyal customer base, who have come to rely upon the expertise and quality of the molds provided by Plastic Boxes Molds.Apart from its commitment to excellence, another aspect that sets Plastic Boxes Molds apart from its competition is its use of cutting-edge technology. The company has made significant investments in machinery and equipment, ensuring that the molds created are of the highest quality. The use of advanced technology has also allowed Plastic Boxes Molds to provide faster turnaround times to its clients, ensuring that projects are completed on time.In conclusion, Plastic Boxes Molds has become a prominent name in the plastic injection molding industry owing to its commitment to innovation, excellence, and use of advanced technology. The company's dedication to providing end-to-end services has made it a one-stop-shop for clients looking for custom molds. With its skilled team, state-of-the-art production facility, and ability to keep up with the latest developments in the industry, Plastic Boxes Molds is poised to continue its success story and innovate the plastic industry, one mold at a time.
Optimizing Part Production with Gas Assisted Injection Molding
Gas Assisted Molding Technology Takes the Automotive Industry by StormThe global automotive industry has been revolutionized by research and development of innovative production technologies that are not only efficient but also cost-effective. One of the most significant breakthroughs in the industry is Gas Assisted Molding Technology (GAM), which has enabled manufacturing processes to produce lighter and stronger parts for vehicles. GAM technology has been widely accepted by leading automakers to create cost-effective, high-quality, and innovative products.As an active player in the automotive industry, a leading Chinese automotive gas-assisted molding technology provider (need to remove the brand name), has taken the forefront in developing advanced technologies to help automakers create cost-effective and high-quality products. Gas Assisted Molding Technology is a new way of manufacturing hollow parts, which uses gas pressure to create the required geometry. The technology molds the plastic parts by injecting molten plastic into a hollow mold cavity and then introducing inert nitrogen gas into the core of the melted plastic.The inserted gas displaces the plastic from the position of the free surface, reduces flow resistance, and controls the plastic flow. As the cavity fills with plastic, the gas pressure pushes the molten material to the far reaches of the mold cavity. This results in an even wall thickness that translates into superior product strength and quality.Over the years, the technology has increasingly become popular among automakers, due to its ability to produce high-quality products with fewer raw materials, making it more cost-effective than traditional molding technologies. GAM technology has been widely adopted to improve the quality of plastic components used in the automotive industry. The lighter and stronger parts produced by GAM technology result in a reduction in weight and enhanced fuel efficiency, which is ideal for electric and hybrid vehicles.A key feature of the technology is that it allows designers and engineers to create complex shapes, which are popular among automakers. The unique shapes are essential in creating modern designs, which are not only aesthetically pleasing but also functional.The use of GAM technology in manufacturing has increased rapidly due to the many benefits it offers. One of the main benefits of the technology is that it enables faster cycle times, leading to an increase in productivity and reduced manufacturing costs. The technology also eliminates the need for welding or gluing, which is costly and time-consuming, making it the most cost-effective method for manufacturing large complex parts.GAM technology is also vital in achieving consistent product quality, which is essential in the automotive industry. The process provides better dimensional accuracy, thus reducing the chances of defects arising in the final product. The result is a higher quality and defect-free product that meets the high expectations of the automotive consumers.The widespread use of GAM technology in the automotive industry has led to a significant reduction in environmental footprint. The technology uses fewer raw materials, resulting in less waste, and lower greenhouse gas emissions.The high demand for GAS technology in the automotive sector has led to its adoption in other industries, such as medical device manufacturing, furniture, and sports equipment. This is because the technology allows for the creation of hollow parts with complex geometries that are lightweight, strong and aesthetically pleasing. The versatility of the technology makes it ideal for any industry that requires high-quality plastic products.In conclusion, Gas Assisted Molding Technology has rapidly transformed the way the automotive industry operates. GAM technology provides designers and engineers with a unique tool that enables them to create high-quality products with complex geometries. This technology offers numerous benefits, including cost-effectiveness, faster cycle times, improved quality, and reduced environmental footprint. As the industry continues to evolve, it is expected that GAM technology will become an even more vital tool for manufacturing innovative and efficient products.
Understanding the Process of Plastic Injection Molding
Mold Plastic Injection, a leading manufacturer in the plastic injection molding industry, has recently announced the introduction of a new and innovative product line. The company, known for its cutting-edge technology and state-of-the-art manufacturing processes, continues to push the boundaries of what is possible in the field of plastic injection molding.With a strong focus on quality and precision, Mold Plastic Injection has established itself as a trusted partner for companies in a wide range of industries, including automotive, aerospace, medical, and consumer goods. The company's commitment to excellence is evident in its rigorous quality control measures and dedication to continuous improvement.One of the key factors that sets Mold Plastic Injection apart from its competitors is its investment in the latest manufacturing technologies. The company's facilities are equipped with advanced machinery and tools, allowing for the production of highly complex and intricate plastic components. This level of sophistication enables Mold Plastic Injection to meet the diverse needs of its customers, from small, intricate parts to large, structural components.In addition to its focus on technology and manufacturing processes, Mold Plastic Injection places a strong emphasis on sustainability and environmental responsibility. The company has implemented eco-friendly practices throughout its operations, from sourcing materials to waste management. By prioritizing sustainability, Mold Plastic Injection not only reduces its environmental impact but also helps its customers meet their own sustainability goals.The newly introduced product line by Mold Plastic Injection represents the culmination of years of research, development, and innovation. The company's team of experienced engineers and designers have worked tirelessly to create a range of products that meet the highest standards of performance and reliability. From prototype development to final production, Mold Plastic Injection applies a rigorous and thorough approach to ensure the quality and consistency of its products.One of the standout features of the new product line is its versatility. Mold Plastic Injection has developed a range of products that are suitable for a multitude of applications, from automotive and aerospace components to medical devices and consumer products. This flexibility makes the new product line an attractive option for companies across various industries.Furthermore, the new product line is designed to meet the strictest industry standards and regulations. Mold Plastic Injection has invested significant resources in ensuring that its products comply with the requirements of different markets and industries. This commitment to compliance and certification demonstrates the company's dedication to delivering high-quality and reliable products to its customers.As part of the launch of the new product line, Mold Plastic Injection has also introduced a range of customization options. The company recognizes that every customer has unique needs and requirements, and as such, offers the ability to tailor its products to specific specifications. This level of customization sets Mold Plastic Injection apart from other manufacturers in the industry, providing customers with the flexibility to create products that meet their exact needs."We are excited to introduce our new product line, which represents a significant milestone for Mold Plastic Injection," said the company's CEO. "We have worked tirelessly to develop a range of products that meet the demands of modern industry, and we are confident that our customers will be impressed by the quality and versatility of these offerings."As Mold Plastic Injection continues to expand its capabilities and product offerings, the company remains committed to its core values of innovation, quality, and sustainability. With a strong focus on customer satisfaction and a dedication to pushing the boundaries of what is possible in the plastic injection molding industry, Mold Plastic Injection is poised to remain a leader in its field for years to come.
New technology in the Pet Preform Blowing Machine industry revolutionizes production process
Pet Preform Blowing Machine has revolutionized the way pet preforms are manufactured. This advanced machine uses the latest technology to produce high-quality pet preforms that are used in the production of PET bottles for a variety of products including water, soda, juice, and more. The machine is designed to be efficient, reliable, and easy to use, making it a valuable asset for companies in the beverage and packaging industries.The company behind this innovative machine is a leading manufacturer of packaging machinery with a commitment to providing top-quality equipment for their clients. With a strong focus on research and development, the company is constantly striving to improve their products and stay ahead of industry trends. Their dedication to excellence has earned them a reputation for delivering reliable and high-performance machinery that meets the needs of their customers.The Pet Preform Blowing Machine is a prime example of the company's commitment to innovation. It is designed to streamline the production process, reducing the time and labor required to manufacture pet preforms. The machine is capable of producing a wide range of preform sizes and shapes, allowing for greater flexibility in bottle design and production. This versatility is a major advantage for companies looking to stay competitive in the ever-evolving beverage market.In addition to its advanced technology, the Pet Preform Blowing Machine is also designed with user-friendly features that make it easy to operate and maintain. This includes an intuitive control panel and a modular design that allows for easy access to key components for maintenance and repairs. The machine is also equipped with safety features to ensure the protection of operators and prevent accidents in the workplace.The company's dedication to customer satisfaction is evident in their comprehensive customer support services. They provide training and technical assistance for customers who purchase their machinery, ensuring that operators are well-equipped to maximize the efficiency and performance of the Pet Preform Blowing Machine. Furthermore, they offer prompt and reliable after-sales service, including spare parts and maintenance services to keep their machines running smoothly for years to come.As sustainability becomes an increasingly important factor in the packaging industry, the Pet Preform Blowing Machine is also designed with energy efficiency in mind. It is engineered to minimize energy consumption without sacrificing production output, making it an environmentally responsible choice for companies seeking to reduce their carbon footprint.Overall, the Pet Preform Blowing Machine is a valuable asset for companies in the beverage and packaging industries. Its advanced technology, user-friendly features, and commitment to sustainability make it a reliable and efficient solution for the production of high-quality pet preforms. With the backing of a reputable and customer-focused company, this machine is set to make a significant impact on the industry and help companies stay ahead of the competition.