Ultimate Guide to Overmolding and Insert Molding for Manufacturing Processes
By:Admin
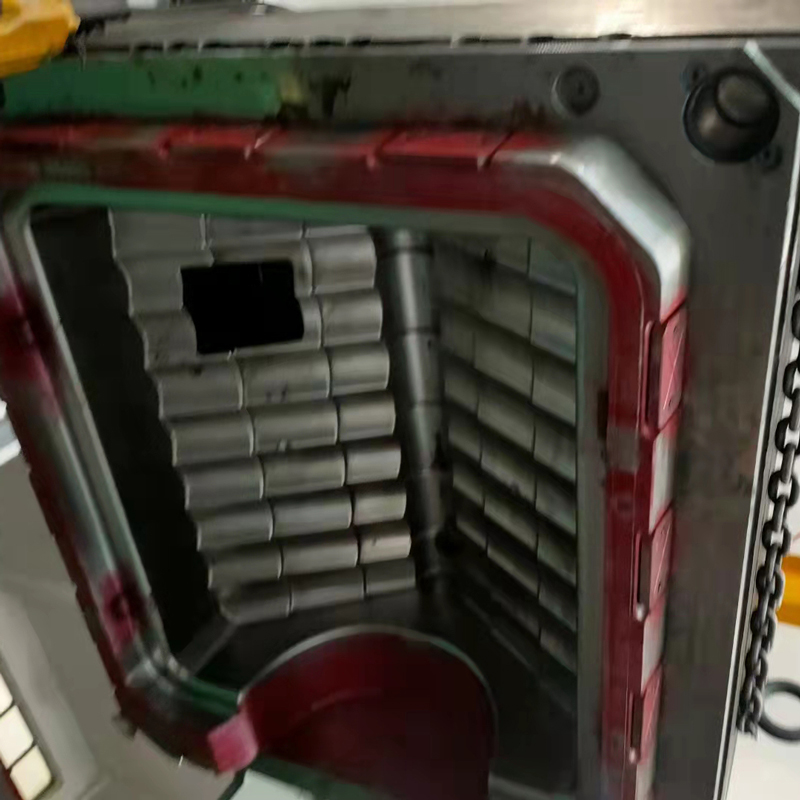
One of the leading companies at the forefront of Overmolding Insert Molding is {}. With a strong focus on innovation and precision engineering, the company has established itself as a key player in the manufacturing and production industry. By incorporating Overmolding Insert Molding into their operations, they have been able to offer a wide range of custom solutions to their clients across the globe.
This advanced manufacturing process allows {}. to create complex and intricate designs that were previously not possible with traditional molding techniques. By overmolding a variety of materials such as plastics, metals, and rubber, the company is able to produce components that are not only durable and reliable but also aesthetically pleasing. This level of versatility and flexibility has set them apart in the industry, allowing them to cater to a diverse clientele with varying needs and specifications.
One of the key advantages of Overmolding Insert Molding is the ability to incorporate multiple functions into a single component. This means that {}. can produce parts that serve a dual purpose, reducing the overall number of components required in a product and ultimately saving on manufacturing costs. Additionally, the overmolded parts are known for their superior strength and resilience, making them suitable for use in demanding applications across several industries.
Another benefit of Overmolding Insert Molding is its ability to create a seamless and integrated product. By fusing different materials together, the company can eliminate the need for additional assembly and welding processes, resulting in a more streamlined and efficient production cycle. This not only results in cost savings but also reduces the overall lead time for manufacturing, allowing for a quicker turnaround for their clients.
In terms of applications, Overmolding Insert Molding has been widely adopted in industries such as automotive, electronics, consumer goods, and medical devices. The ability to combine materials with varying properties has opened up new possibilities for product design and functionality, allowing companies to stay ahead of the curve in their respective markets. By leveraging this advanced manufacturing process, {}. has been able to stay at the forefront of innovation and offer their clients cutting-edge solutions that set them apart from the competition.
Looking ahead, the future of Overmolding Insert Molding looks promising, with advancements in materials and technology continuing to drive the evolution of this manufacturing process. As companies continue to demand high-performance components with complex designs, it is clear that Overmolding Insert Molding will play a pivotal role in meeting these requirements. {}. is well-positioned to lead the way in this space, leveraging their expertise and capabilities to continue delivering exceptional products to their clients.
In conclusion, Overmolding Insert Molding has revolutionized the manufacturing industry, offering a myriad of benefits that have redefined product design and production. {}. has been a driving force in embracing this advanced manufacturing process, and their commitment to innovation has solidified their position as a leader in the industry. With the continued evolution of Overmolding Insert Molding, there is no doubt that the company will continue to push the boundaries of what is possible in the realm of manufacturing.
Company News & Blog
Revolutionizing Manufacturing: The Key Advantages of Injection Molding
Introducing Innovative Insert Injection Molding Technology: Revolutionizing Manufacturing ProcessesIn an ever-evolving world, where technology is constantly pushing the boundaries of numerous industries, insert injection molding has emerged as a game-changing manufacturing process. This groundbreaking innovation, employed by numerous companies across various sectors, allows for the production of highly intricate and detailed products with unmatched precision and efficiency.One prominent leader in the insert injection molding industry is the renowned company {}, known for its commitment to excellence and cutting-edge technology. With a vast portfolio of successful projects and a reputation for delivering top-tier solutions, {} stands at the forefront of revolutionizing manufacturing processes.Insert injection molding is a manufacturing technique that involves injecting molten material, typically a thermoplastic or thermosetting polymer, into a pre-formed mold. Nevertheless, what makes this technique unique is the incorporation of inserts during the molding process. These inserts can be metal, ceramic, or plastic parts that are placed strategically within the mold, enhancing the final product's durability and functionality.The advantages of insert injection molding cannot be overstated. First and foremost, this process allows for a high degree of design flexibility. Inserts can be precisely positioned within the mold, thereby enabling the creation of intricate components with unparalleled accuracy. This level of precision opens up new possibilities for industries such as automotive, electronics, and medical devices, where intricate and complex parts are often required.Furthermore, insert injection molding drastically reduces manufacturing time and costs. By incorporating inserts during the molding process, manufacturers can eliminate the need for secondary operations such as drilling, fastening, or welding. This streamlining of production eliminates additional labor costs and significantly reduces assembly time, resulting in a more efficient and cost-effective manufacturing process.Moreover, insert injection molding offers enhanced product quality and durability. The integration of inserts improves the structural integrity of the final product, making it stronger and more resistant to external factors such as temperature fluctuations, pressure, or mechanical stress. Consequently, products manufactured through this process boast increased reliability and longevity, meeting the stringent demands of various industries.With a vision to revolutionize manufacturing processes, {} has perfected their insert injection molding techniques by combining innovative technology, engineering expertise, and meticulous quality control. {} has established itself as a trusted partner for numerous industry leaders, delivering exceptional solutions tailored to their specific needs.One industry that has greatly benefited from insert injection molding is the automotive sector. With an increasing demand for lightweight and durable components, this technology allows automotive manufacturers to produce intricate and complex parts that were once deemed challenging. From interior trims to electronic housings, insert injection molding has become the go-to solution for achieving high precision and outstanding performance in the automotive industry.Similarly, the electronics industry has witnessed the transformative power of insert injection molding. With the growing trend of miniaturization, electronics manufacturers constantly seek ways to pack more functionality in smaller devices. Insert injection molding enables the production of intricate electronic components with reduced form factors, without compromising their structural integrity or performance. This technology has facilitated the development of innovative electronic devices, offering users a level of convenience and functionality never seen before.Lastly, the medical device industry has embraced insert injection molding for manufacturing critical components such as catheters, implants, or surgical instruments. These devices require exceptional precision, biocompatibility, and strength, all of which are made possible through insert injection molding. This technology ensures that medical devices meet the rigorous quality and safety standards, while also allowing for cost-effective solutions in an industry where every second matters.In conclusion, insert injection molding has emerged as a game-changing technology in the manufacturing industry. With innovation at its core, {} has been instrumental in advancing this technique, revolutionizing numerous industries along the way. The diverse advantages of insert injection molding, including design flexibility, reduced costs, enhanced product quality, and durability, make it an indispensable manufacturing solution. As technology continues to evolve, we can only anticipate further advancements in this field, resulting in even more efficient and groundbreaking manufacturing processes.
Top Techniques for Custom Blow Molding That Will Blow You Away
[Source: Custom Blow Mold (brand name removed)]Custom Blow Mold, a leading manufacturer in the plastics industry, is renowned for its exceptional quality and innovative products. With its state-of-the-art manufacturing facilities and a highly skilled team, the company has been successfully meeting the needs of various industries for over two decades.Established in [Year], Custom Blow Mold has set itself apart from its competitors by providing tailored blow molding solutions to its diverse clientele. The company specializes in manufacturing custom-designed blow molds, ensuring that each product is specifically crafted to meet the unique requirements of its customers. From concept development to final production, Custom Blow Mold offers a comprehensive range of services, guaranteeing maximum satisfaction.At the core of Custom Blow Mold's success lies its commitment to quality. The company strictly adheres to the highest industry standards, utilizing advanced technology and cutting-edge machinery to deliver premium products. With a team of experienced engineers and designers, every mold undergoes meticulous testing and inspection, assuring superior functionality and durability. Custom Blow Mold understands the significance of precision and consistency in the plastics industry and strives to achieve excellence in every aspect of its manufacturing process.In addition to its dedication to quality, Custom Blow Mold takes pride in its ability to provide innovative solutions. The company continually invests in research and development, staying at the forefront of technological advancements in blow molding. This enables Custom Blow Mold to offer its customers cutting-edge products that help maximize efficiency and enhance productivity. Whether it's developing new molds or optimizing existing ones, the company's commitment to innovation is unwavering.Custom Blow Mold caters to a wide range of industries, including automotive, packaging, consumer goods, and more. By understanding the unique requirements and challenges faced by each sector, the company tailors its products to deliver exceptional results. From manufacturing complex automotive components to producing custom packaging solutions, Custom Blow Mold has the expertise and capabilities to handle diverse projects efficiently and effectively.The success of Custom Blow Mold can be attributed to its strong customer-centric approach. With a firm belief in building long-term partnerships, the company emphasizes clear and open communication with its clients. Custom Blow Mold takes the time to understand the specific needs and expectations of each customer, ensuring that their vision is transformed into a reality. The company's customer service is unparalleled, with a dedicated team committed to providing prompt assistance and support throughout the entire process.As a socially responsible corporate entity, Custom Blow Mold also prioritizes sustainability in its operations. The company employs environmentally friendly manufacturing processes and materials, minimizing its carbon footprint and contributing towards a greener future. Custom Blow Mold recognizes the importance of sustainability and actively seeks ways to incorporate eco-friendly practices into its production methods.Looking ahead, Custom Blow Mold aims to further expand its product offerings and geographical reach. The company plans to invest in advanced technologies to enhance its manufacturing capabilities and explore new markets. With its commitment to quality, innovation, and customer satisfaction, Custom Blow Mold is poised to continue its impressive growth trajectory and solidify its position as a global leader in the plastics industry.In conclusion, Custom Blow Mold sets a benchmark for excellence in the plastics industry with its exceptional quality, innovative solutions, and customer-centric approach. The company's commitment to precision, sustainability, and continuous improvement has propelled it to the forefront of the industry. Custom Blow Mold's relentless pursuit of excellence ensures that it remains a trusted partner for companies seeking top-notch blow molding solutions.
Discover the Cost of Injection Moulding Dies: A Comprehensive Guide
Injection Moulding Die Cost: An Overview of the Factors InvolvedManufacturing companies all over the world use injection moulding as one of their primary manufacturing techniques. Whether it is automotive, medical, or consumer goods, injection moulding is widely used due to its high efficiency and precision. Injection moulding die is a key component of any injection moulding operation. It is the device that shapes plastic pellets or granules into a finished product.However, the cost of injection moulding dies can vary depending on several factors such as design, size, complexity, material, and finishing. In this article, we will discuss the various factors that impact injection moulding die costs.Factors that Impact Injection Moulding Die CostsDesignThe design of the injection moulding die is one of the primary factors that impacts the cost. A complicated and intricate design would require more engineering time, ultimately increasing the overall cost. On the other hand, a simple design would require less engineering time and would be more cost-effective.SizeThe size of the injection moulding die plays a significant role in determining its cost. Larger dies would require more material and energy during production, increasing the overall cost. The complexity of the design would also increase with the size of the die, ultimately impacting the final cost.ComplexityThe complexity of the injection moulding die determines the amount of detail required in the design and manufacturing process. A more intricate design requires more sophisticated manufacturing techniques, ultimately resulting in a higher cost.MaterialThe material used to manufacture the injection moulding die also impacts the final cost. Aluminium is a popular choice for injection moulding dies as it is cheaper, faster, and easier to manufacture. However, it is not as durable as steel and requires frequent replacement. Steel is a more expensive option, but it is more durable and can typically withstand higher temperature and pressure.FinishingThe finishing of the injection moulding die is also a factor that affects the cost. Depending on the desired finish, additional processes such as polishing or texturing may be required, ultimately increasing the overall cost.How to Reduce Injection Moulding Die Costs1. Simplify the DesignAs previously mentioned, the design of the injection moulding die plays a significant role in determining its cost. Simplifying the design can reduce the complexity of the manufacturing process and ultimately reduce the cost.2. Use the Right MaterialChoosing the right material for the injection moulding die can have a significant impact on the cost. Using aluminium instead of steel may be a better choice for simple products that require short production runs. On the other hand, using steel may be a better option for more complex products that require a higher degree of durability.3. Consider the Lifecycle of the DieConsider the lifecycle of the injection moulding die when making decisions about its production. The cost of the die is not just the upfront cost but also the cost of maintenance, repair, and replacement over its lifetime. A more expensive steel die may have a longer lifespan and require less frequent replacement, ultimately making it the more cost-effective option in the long run.ConclusionInjection moulding is a widely-used manufacturing technique that allows for high efficiency and precision. The cost of the injection moulding die can vary depending on several factors such as design, size, complexity, material, and finishing. However, by simplifying the design, using the right material, and considering the lifecycle of the die, manufacturers can reduce the overall cost and increase profitability. Ultimately, it is important to consider the cost-benefit analysis of the injection moulding die to ensure that the final product meets the required specifications at a cost-effective price.
High-Quality ABS Pellets for Injection Molding: Everything You Need to Know
Abs Pellets For Injection Molding Combined With The Company IntroductionThe market for injection molding is growing rapidly, and the demand for high-quality ABS pellets is higher than ever before. With the increasing need for durable and versatile plastics for a wide range of industries, companies are constantly on the lookout for reliable suppliers of ABS pellets for injection molding. This is where [Company Name] comes in, offering top-quality ABS pellets that meet the strictest industry standards.[Company Name] is a leading supplier of ABS pellets for injection molding, with a reputation for delivering excellent quality products to customers around the world. The company has been in the business for over [number] years, and has a deep understanding of the unique requirements of the injection molding industry. This expertise allows the company to provide its customers with tailored solutions that meet their specific needs.The ABS pellets offered by [Company Name] are highly versatile, making them suitable for a wide range of applications. Whether it's for automotive parts, electronic components, or consumer goods, these pellets are designed to deliver outstanding performance and durability. The company's ABS pellets are also available in a variety of grades and colors, allowing customers to choose the perfect material for their specific injection molding needs.One of the key factors that sets [Company Name] apart from its competitors is its commitment to quality. The company has strict quality control measures in place throughout the production process, ensuring that its ABS pellets consistently meet the highest standards. From raw material sourcing to the final packaging and delivery, every step is carefully monitored to guarantee the quality and consistency of the products.In addition to its dedication to quality, [Company Name] also prides itself on its excellent customer service. The company works closely with its customers to understand their individual requirements and provide them with the best possible solutions. This customer-centric approach has earned [Company Name] a solid reputation in the industry, with many long-standing relationships with satisfied clients.As the demand for ABS pellets for injection molding continues to grow, [Company Name] is well-positioned to meet the needs of its customers. The company has a strong focus on innovation and constantly seeks to improve its products and services to stay ahead of the competition. With a team of highly skilled professionals and state-of-the-art manufacturing facilities, [Company Name] is able to consistently deliver high-quality ABS pellets that meet the evolving needs of the injection molding industry.In conclusion, [Company Name] is a trusted supplier of ABS pellets for injection molding, with a strong track record of delivering exceptional products and services to its customers. With a commitment to quality, innovation, and customer satisfaction, the company is well-equipped to meet the growing demand for ABS pellets and continue to be a leader in the injection molding industry.
Discover the Latest Innovation in Cavity Pet Blowing Machines
Introducing the New and Efficient 2 Cavity Pet Blowing Machine for Enhanced Manufacturing ProcessesThe manufacturing industry is constantly evolving, with machines becoming more advanced to meet the growing demands of the market. In line with this, we are excited to introduce our latest innovation, the 2 Cavity Pet Blowing Machine, designed to revolutionize the production of PET bottles.This cutting-edge machine is unlike any other, boasting a formidable range of features that make it a game-changer within the industry. Its efficient design allows for the simultaneous production of two PET bottles, significantly increasing output and saving valuable time during the manufacturing process. With this machine, manufacturers can effectively double their production capacity, leading to improved profitability and customer satisfaction.One of the main benefits of our 2 Cavity Pet Blowing Machine is its ability to produce bottles of varying sizes and shapes without compromising on quality. Its versatility means that manufacturers can cater to the diverse needs and preferences of consumers, expanding their product offerings and staying ahead of their competitors. Whether it's small or large bottles, round or square containers, this machine can handle it all with ease.In addition to its versatility, our 2 Cavity Pet Blowing Machine is also renowned for its efficiency and precision. Equipped with advanced technology, it ensures that each bottle is perfectly shaped and durable. The machine's automated design streamlines the production process, reducing the need for manual labor and minimizing human error. This not only saves time but also cuts down on production costs, ultimately increasing the overall profitability of manufacturing operations.Furthermore, we have placed great emphasis on the sustainability aspect of our 2 Cavity Pet Blowing Machine. With increasing global concerns over environmental issues, manufacturers are seeking solutions that align with their green objectives. Our machine is designed to reduce energy consumption, resulting in lower carbon emissions and a reduced environmental footprint. By investing in this machine, manufacturers can demonstrate their commitment to sustainable manufacturing practices and gain a competitive edge in the market.To ensure our customers receive the full benefits of our 2 Cavity Pet Blowing Machine, we offer comprehensive after-sales support and maintenance services. Our team of highly skilled technicians is available to provide training and assistance, ensuring smooth and trouble-free operations. Additionally, our customer service representatives are always ready to answer inquiries and address any concerns that may arise.As a leading player in the manufacturing industry, we are committed to delivering exceptional quality and innovative solutions. Our 2 Cavity Pet Blowing Machine is a testament to our dedication to meeting the evolving needs of our customers. With its advanced features, efficiency, precision, and sustainability, this machine is set to revolutionize the PET bottle manufacturing process.In conclusion, the introduction of our 2 Cavity Pet Blowing Machine brings a new level of efficiency, versatility, and sustainability to the manufacturing industry. With its ability to simultaneously produce two high-quality PET bottles of varying sizes and shapes, this machine represents a significant advancement for manufacturers. Emphasizing precision and energy efficiency, it sets a new industry standard. By investing in our 2 Cavity Pet Blowing Machine, manufacturers can accelerate their production capacity, reduce costs, and demonstrate their commitment to sustainable manufacturing practices. We are excited to collaborate with manufacturers in achieving their production goals and staying ahead in this ever-evolving industry.
How to Make Your Own Potion Bottle Mold for Halloween Crafts and Decorations
A Potion Bottle Mold Invention Sparks Interest in the IndustryA new invention, a potion bottle mold, is set to revolutionize the cosmetics industry. This invention is a game-changer for the industry as the mold is capable of creating unique, intricate, and desirable glass bottles of any shape or size. With the cut-throat competition in the cosmetics industry, this innovation is considered a welcome and necessary advancement that provides a competitive edge to manufacturers.The new potion bottle mold has been developed by a leading company in the cosmetics industry, which has been producing high-quality packaging materials for the industry for several years. The company is renowned for their quality packaging materials and their ability to provide innovative and cost-effective solutions for their clients.According to the company's website, they specialize in designing and manufacturing packaging components for a wide range of industries, including cosmetics, skincare, and pharmaceuticals. Their attention to detail, professionalism, and commitment to quality have helped them establish a loyal customer base in the industry.The newly developed potion bottle mold is the latest in their line of innovative products that are aimed at improving the customer experience and driving sales growth for their clients.The mold is produced using state-of-the-art technology and is capable of creating glass bottles of any shape or size. This provides manufacturers with endless options when it comes to designing packaging that reflects their brand and resonates with consumers.The mold has a unique feature that allows for intricate designs to be created on the surface of the bottle. This means that the bottles can be embossed or engraved with designs that complement the brand's identity and helps their products to stand out on the shelves.The potion bottle mold has been met with enthusiasm in the industry, with industry experts praising the innovation for its ability to provide manufacturers with a robust and cost-effective solution to their packaging needs. This comes at a time when the industry is experiencing increased competition, making it difficult to differentiate one product from the other.Manufacturers can now leverage the mold to create unique packaging that not only sets their products apart from their competitors but also enhances the user experience. Consumers are increasingly looking for products that are aesthetically pleasing and offer value for their money. With the potion bottle mold, manufacturers can now offer products that tick all the boxes.The mold is also cost-effective, allowing manufacturers to produce quality packaging materials at an affordable price point. This is important as packaging costs can quickly add up, especially when producing large quantities of products.In conclusion, the new potion bottle mold is set to revolutionize the cosmetics industry, providing manufacturers with a robust and cost-effective solution to their packaging needs. The mold's ability to produce unique, intricate, and aesthetically pleasing packaging materials means that manufacturers can now offer products that resonate with consumers and stand out from their competitors. With the increasing demand for quality packaging materials in the industry, the potion bottle mold is a timely innovation that is set to spark further interest in the industry.
Experts Discuss the Future of Plastic Injection Molding
Custom Molds Plastics: Pioneering Innovation in the Plastics IndustryIn today's rapidly evolving world, there is an increasing demand for innovative and efficient solutions across various industries. Custom Molds Plastics, a leading name in the plastics industry, has been at the forefront of providing cutting-edge custom plastic solutions to meet the ever-changing needs of its clients. With a strong focus on technology, quality, and customer satisfaction, Custom Molds Plastics continues to pave the way for the future of plastics manufacturing.As a trailblazer in the industry, Custom Molds Plastics has been an industry leader since its establishment in [year]. With a diverse range of products and services, the company caters to the needs of multiple sectors, including automotive, aerospace, medical, and consumer goods. Their comprehensive portfolio includes injection molding, blow molding, rapid prototyping, and product design. Custom Molds Plastics has developed a reputation for its engineering expertise, state-of-the-art facilities, and commitment to delivering exceptional customer service.Custom Molds Plastics prides itself on its ability to adapt and respond quickly to market changes. By staying at the forefront of technological advancements, the company has been able to meet the evolving demands of its clients. With a dedicated team of experienced engineers and designers, coupled with advanced manufacturing processes, Custom Molds Plastics has been able to provide innovative solutions for complex projects.One of the key factors that sets Custom Molds Plastics apart from its competitors is its emphasis on quality. The company follows stringent quality control measures at every stage of the manufacturing process to ensure that the final products meet the highest industry standards. By investing in advanced quality control systems and conducting rigorous inspections, Custom Molds Plastics guarantees the durability, functionality, and reliability of its plastic components.Moreover, Custom Molds Plastics places a strong emphasis on sustainability and environmental responsibility. The company recognizes the importance of reducing its environmental footprint and strives to minimize waste, energy consumption, and emissions. By implementing eco-friendly practices and utilizing recyclable materials, Custom Molds Plastics not only helps its clients achieve their sustainability goals but also contributes to a greener future.With a customer-centric approach, Custom Molds Plastics takes pride in building long-term relationships with its clients. The company understands that each project is unique and works closely with its customers to provide customized solutions that perfectly meet their requirements. From initial design discussions to final product delivery, Custom Molds Plastics ensures open and transparent communication, providing clients with regular updates and maintaining a collaborative environment.To further enhance its capabilities and meet the growing demands of the industry, Custom Molds Plastics continually invests in research and development. The company actively collaborates with leading universities and research institutions to stay ahead of emerging trends and technologies. This commitment to innovation has enabled Custom Molds Plastics to develop new materials, processes, and manufacturing techniques that push the boundaries of what is possible in the plastics industry.Looking ahead, Custom Molds Plastics remains dedicated to providing its clients with innovative and sustainable solutions. By embracing new technologies, fostering a culture of continuous improvement, and prioritizing customer satisfaction, the company is poised to lead the way in the ever-evolving plastics industry.In conclusion, Custom Molds Plastics stands as a shining example of a company that combines technological innovation, quality manufacturing, and customer-centricity. With its pioneering spirit, commitment to sustainability, and dedication to excellence, Custom Molds Plastics continues to shape the plastics industry and provide its clients with the best solutions for their needs.
Discover the Latest Innovations in Plastic Box Molds for Improved Efficiency and Longevity
Plastic Boxes Molds - Innovating the Plastic Industry, One Mold at a TimeIn today's fast-moving world, plastic products have become an essential part of our daily lives. From packaging to storage, plastics have become the go-to material for a variety of needs. While plastic products have made our lives easier, the manufacturing process of these products is complex and requires a lot of effort. Amongst the various manufacturing processes of plastic products, plastic injection molding is one of the most popular ones. And when it comes to molds for these products, Plastic Boxes Molds has become one of the premium names in the industry.Established in the year 2010, Plastic Boxes Molds, a privately owned company based in China, has been a frontrunner in the plastic injection molding industry. The company has been making great strides over the years by serving a myriad of industries, including automotive, defense, and consumer goods. The company prides itself on being one of the best in the plastic injection molding business, with a state-of-the-art production facility spanning over 6000 square meters.Plastic Boxes Molds has made a name for itself in the industry by manufacturing a wide variety of molds, including but not limited to custom thermoplastic molds and injection molds. The company has made its mark by providing high-quality molds that are tailored to the specific needs of each client. Plastic Boxes Molds believes that the key to success is to continually innovate and evolve with the changing industry trends. As a result, Plastic Boxes Molds has made significant investments in R&D to keep up with the latest developments in the industry.The company prides itself on its ability to provide end-to-end services to its clients. The services provided by Plastic Boxes Molds cover every aspect of the plastic injection molding process, from design and engineering to the final product. The company's expertise in designing and engineering molds has made it one of the most sought-after companies in the industry.Plastic Boxes Molds has a team of highly skilled professionals who are passionate about their work. The team takes a hands-on approach to every project they undertake, ensuring that every detail is taken care of to deliver the best results. The company's commitment to excellence has garnered a loyal customer base, who have come to rely upon the expertise and quality of the molds provided by Plastic Boxes Molds.Apart from its commitment to excellence, another aspect that sets Plastic Boxes Molds apart from its competition is its use of cutting-edge technology. The company has made significant investments in machinery and equipment, ensuring that the molds created are of the highest quality. The use of advanced technology has also allowed Plastic Boxes Molds to provide faster turnaround times to its clients, ensuring that projects are completed on time.In conclusion, Plastic Boxes Molds has become a prominent name in the plastic injection molding industry owing to its commitment to innovation, excellence, and use of advanced technology. The company's dedication to providing end-to-end services has made it a one-stop-shop for clients looking for custom molds. With its skilled team, state-of-the-art production facility, and ability to keep up with the latest developments in the industry, Plastic Boxes Molds is poised to continue its success story and innovate the plastic industry, one mold at a time.
Discover the Benefits of Injection Molded Pallets for Your Business
Injection Molded Pallets Revolutionizing the Supply Chain IndustryIn today's fast-paced and highly competitive industry, companies are constantly looking for innovative ways to streamline their operations and improve efficiency. One company at the forefront of this push for innovation is {Company Name}, a leading provider of injection molded pallets. With their cutting-edge technology and commitment to sustainability, {Company Name} is revolutionizing the supply chain industry.{Company Name} is a global leader in the manufacturing of injection molded pallets. Their pallets are designed to be lightweight, durable, and sustainable, making them the perfect solution for companies looking to improve their supply chain operations. {Company Name} has a strong focus on sustainability and is dedicated to minimizing their environmental impact. They use recycled materials in their manufacturing process and their pallets are 100% recyclable, making them an eco-friendly choice for companies looking to reduce their carbon footprint.One of the key advantages of {Company Name}'s injection molded pallets is their durability. Unlike traditional wooden pallets, which are prone to splintering, cracking, and warping, {Company Name}'s pallets are designed to withstand the rigors of the supply chain industry. They are also resistant to moisture, mold, and mildew, making them the ideal choice for companies that require clean and hygienic transportation solutions.{Company Name} offers a wide range of pallets to suit the needs of different industries. Their pallets come in various sizes and configurations, allowing companies to choose the best option for their specific requirements. {Company Name} also offers custom design services, allowing companies to create pallets that are tailored to their unique needs. This commitment to customization and flexibility has made {Company Name} a trusted partner for companies across the globe.In addition to their commitment to sustainability and durability, {Company Name}'s injection molded pallets offer significant cost savings for companies. Their pallets are lightweight, making them cheaper to transport than traditional wooden pallets. This can result in lower shipping costs and reduced fuel consumption, making {Company Name}'s pallets a cost-effective choice for companies looking to improve their bottom line.{Company Name} also excels in providing exceptional customer service. Their team of experts is dedicated to providing personalized assistance to their clients, ensuring that they receive the best possible solutions for their supply chain needs. {Company Name} is committed to building long-lasting relationships with their clients, and their dedication to customer satisfaction sets them apart in the industry.With their focus on sustainability, durability, cost savings, and exceptional customer service, {Company Name} is leading the way in revolutionizing the supply chain industry. Their injection molded pallets offer a sustainable, cost-effective, and flexible solution for companies looking to improve their operations. As the industry continues to evolve, {Company Name} remains at the forefront, driving innovation and setting new standards in the supply chain sector.
Top Benefits of Vertical Injection Molding for Manufacturing Applications
Vertical Injection Molding Machines Market Growing at a CAGR of 4.70% During 2021-2026The global market for vertical injection molding machines is anticipated to experience considerable growth over the forecast period from 2021 to 2026. The market is expected to grow at a CAGR of 4.70% during the forecast period.Vertical injection molding machines are used to produce various plastic products, including automotive parts, electronic components, and medical devices. These machines are known for their high efficiency, precision, and versatility in manufacturing a wide range of products.The vertical injection molding machines market is driven by several factors, including the growing demand for plastic products across various industries, technological advancements in injection molding machines, and the increasing adoption of automation in manufacturing processes.One of the key players in the vertical injection molding machines market is {}, a leading manufacturer of injection molding machines. The company offers a wide range of vertical injection molding machines that are known for their high performance, reliability, and precision. With a strong focus on innovation and quality, {} has established a strong presence in the global market and has built a strong reputation for delivering cutting-edge solutions to its customers.With a comprehensive product portfolio and a strong focus on research and development, {} is well-positioned to capitalize on the growing demand for vertical injection molding machines. The company's commitment to innovation and quality has enabled it to maintain a strong competitive position in the market and establish itself as a trusted partner for its customers.In addition to its strong product offerings, {} is also known for its excellent customer service and support. The company has a global network of sales and service professionals who are dedicated to providing the highest level of support to its customers. Whether it's technical assistance, spare parts, or training, {} is committed to ensuring that its customers receive the support they need to maximize the performance of their injection molding machines.In terms of geographical presence, {} has a strong global footprint with a presence in key regions such as North America, Europe, Asia Pacific, and Latin America. The company's global presence enables it to cater to the diverse needs of its customer base and provide localized support and services to its customers.With a strong focus on sustainability, {} is also committed to developing environmentally friendly solutions that help reduce the environmental impact of plastic manufacturing processes. The company's efforts in sustainability have been recognized by industry experts and have helped it to differentiate itself in the market.Looking ahead, the global market for vertical injection molding machines is expected to continue to grow at a steady pace, driven by the increasing demand for plastic products across various industries. With its strong product portfolio, commitment to innovation, and excellent customer support, {} is well-positioned to capitalize on the growing opportunities in the market and further strengthen its position as a leading player in the global vertical injection molding machines market.