Gas-assisted injection cycle table

gas assisted plastic injection mold case show
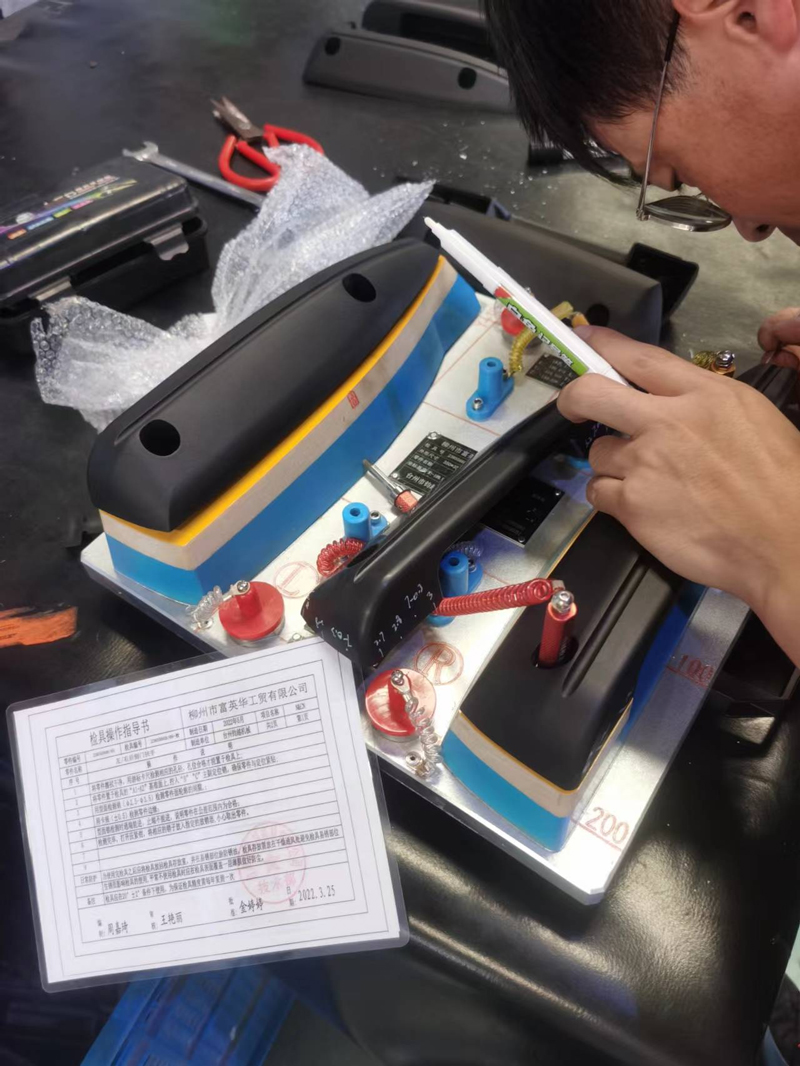
Gas-Assisted Injection Molding Process
Gas-assisted injection molding is roughly divided into 4 stages: plastic injection, gas injection, pressure-holding cooling, and gas discharge. 1. First, the plastic melt is injected into the mold cavity until the melt fills from 70% to 90% of the mold cavity. The temperature of the melt is lower, and the cavity walls form a thinner curing layer. Compared to the conventional molding process, the required molding pressure is low because the cavity is only partially filled, and the air channel in the mold also facilitates the flow of the melt. If the molding pressure is too high and too much material is used, it is easy to cause melt accumulation and sink marks in places with too much material; if the material is too little, it will cause blow through. 2. Gas injection: A gas with a certain volume or pressure (generally nitrogen gas) is injected into the chamber. In this stage, the switching time to switch from melt to nitrogen injection, and correctly determine the gas pressure, related to the product quality, this stage may appear many gas injection product defects, the short delay switch is to control the thickness of the condensate layer, adjust the gas flow space, cooling the gate plastic to prevent gas flow (gas flow from the gate system rather than the preset air channel 3. Pressure-holding cooling: After the cavity and gas must be filled with a certain gas pressure, from inside to outside, to ensure that the outer surface of the product is close to the mold wall; and through the second penetration of the gas (the gas continues into the plastic interior), to make up for the internal cooling contraction of the product, pressure protection generally includes high pressure holding and low pressure holding two stages. 4. Air discharge: After the product is firmly cooled and formed, the gas in the cavity and the core can be discharged through the exhaust needle or spray, and then open the mold to remove the product. It should be noted that the injection gas in the gas-assisted injection molding process must be discharged before the mold is opened. If the pressure gas is not discharged in time, the product will expand or even break.Water assisted plastic injection mold case show
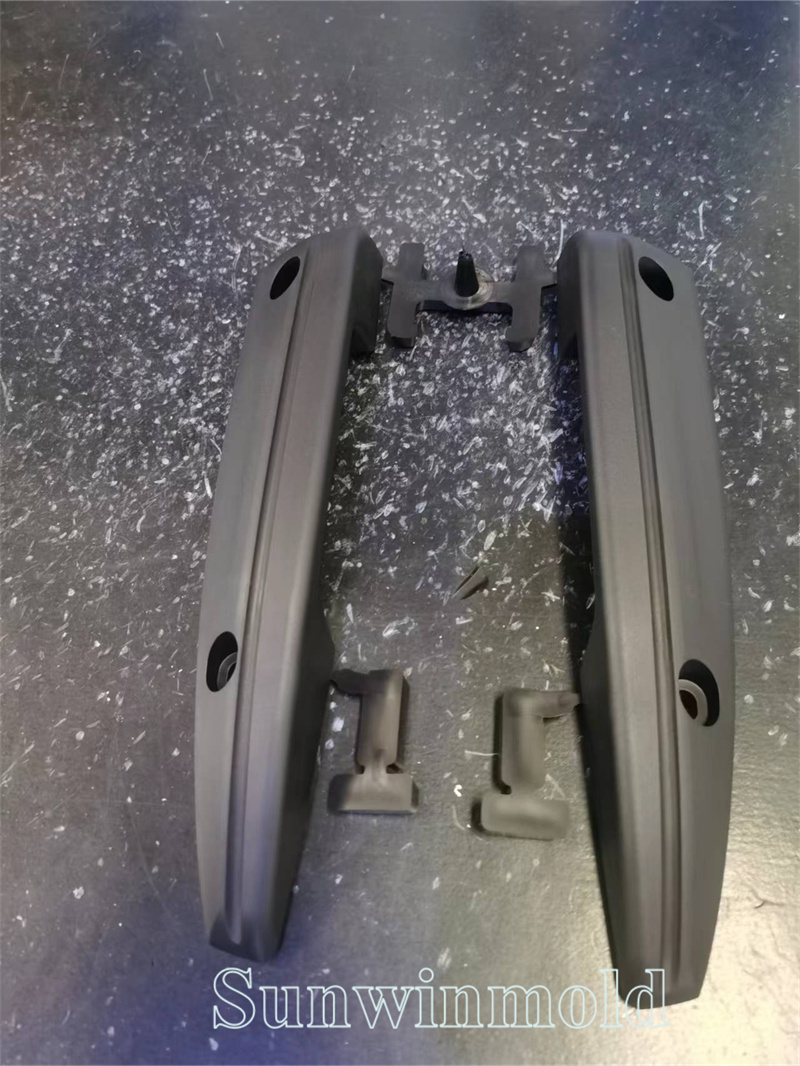
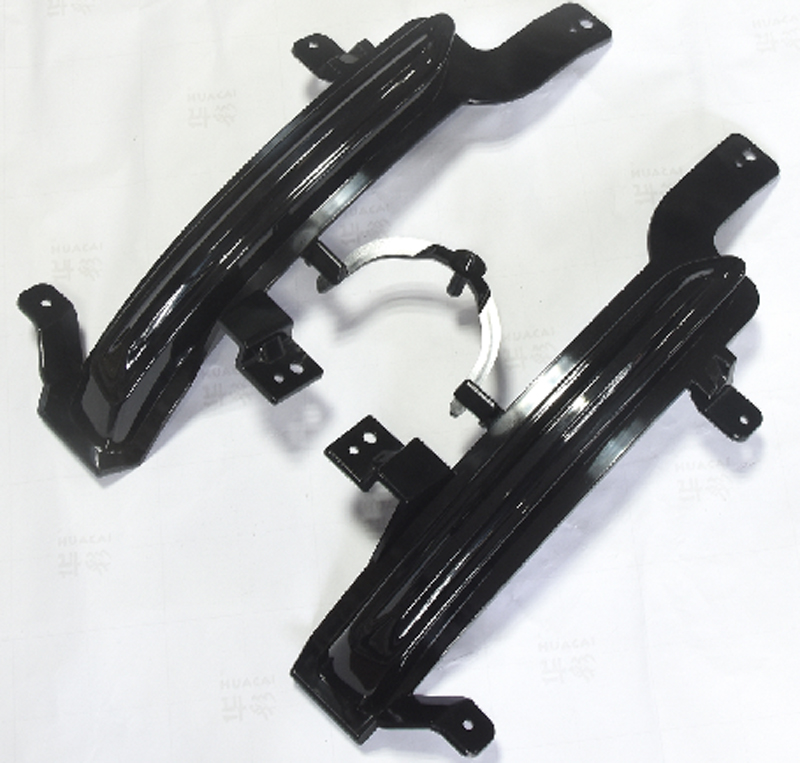
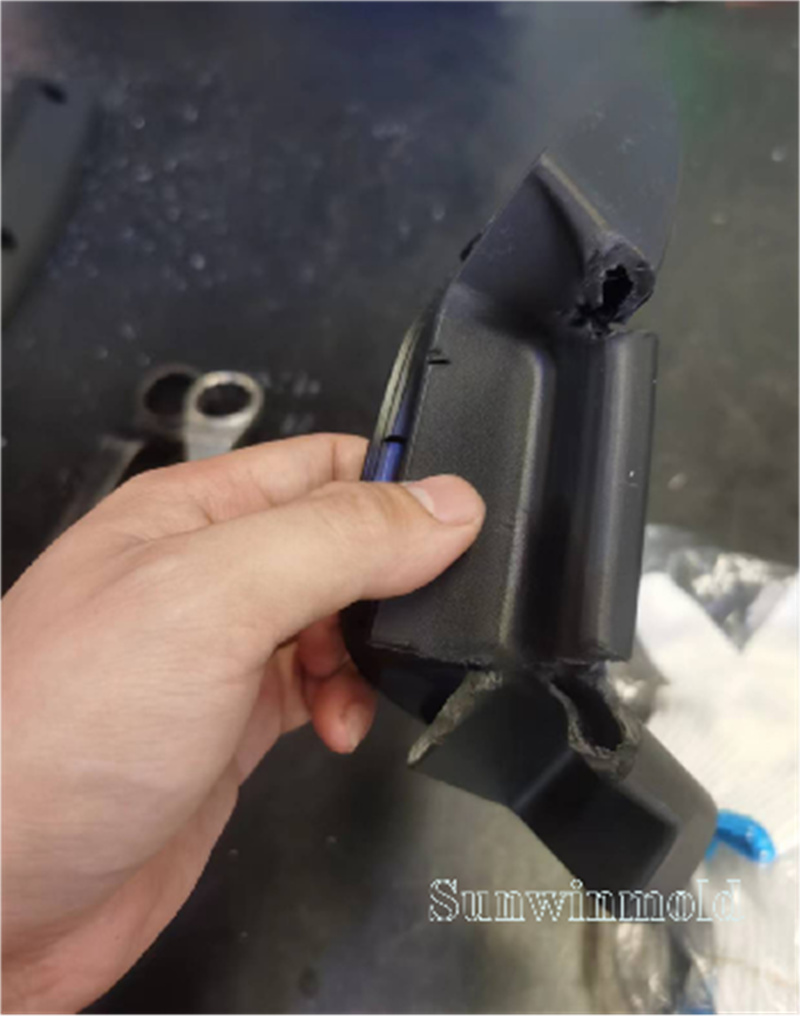
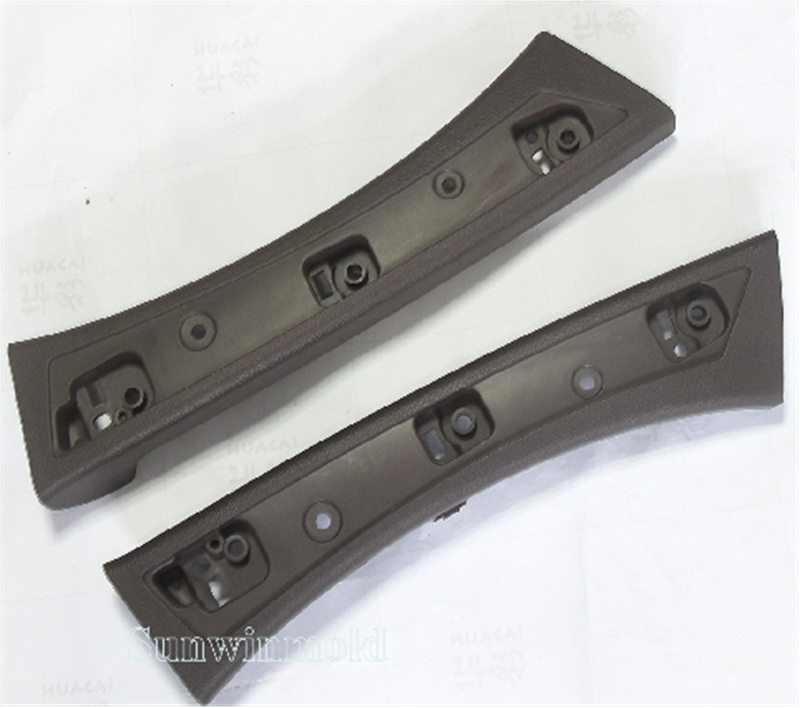
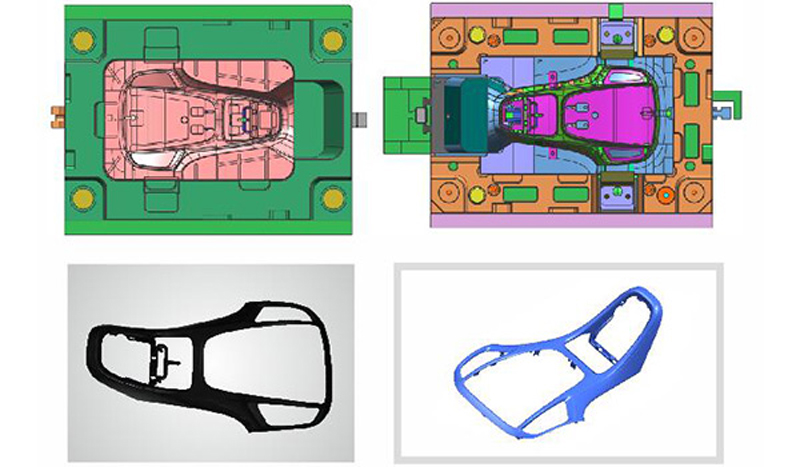
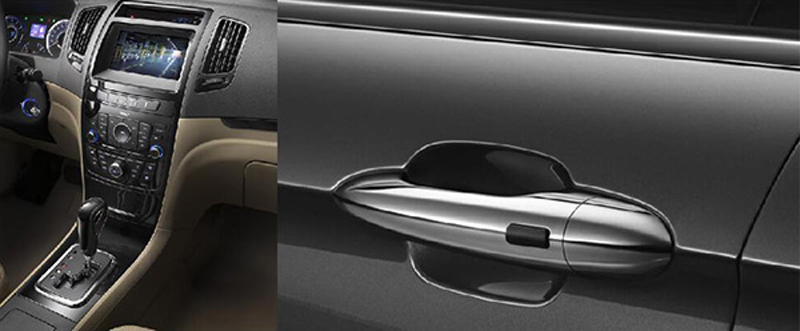
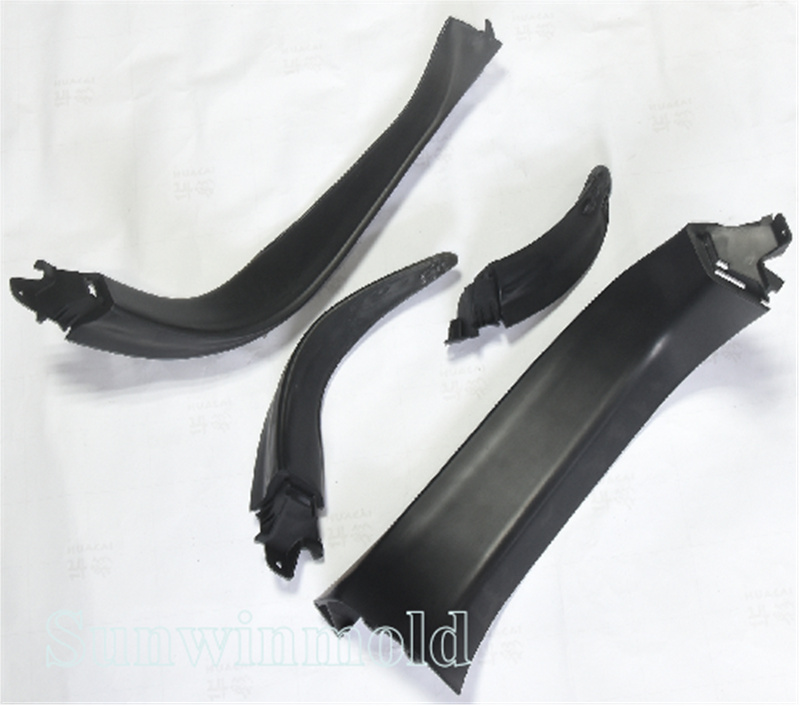
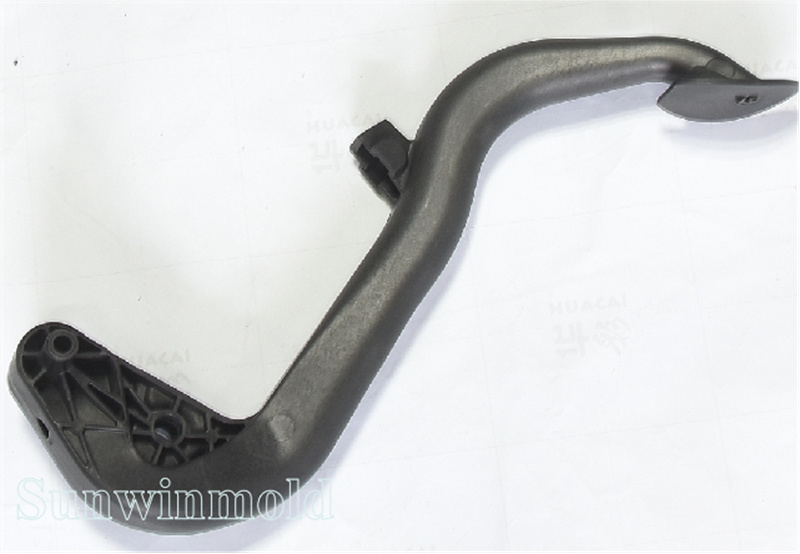
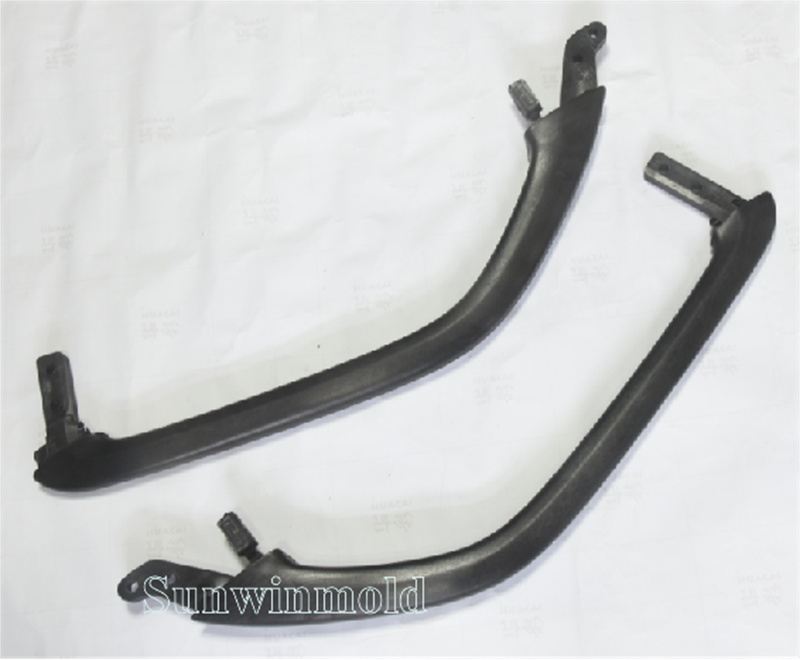
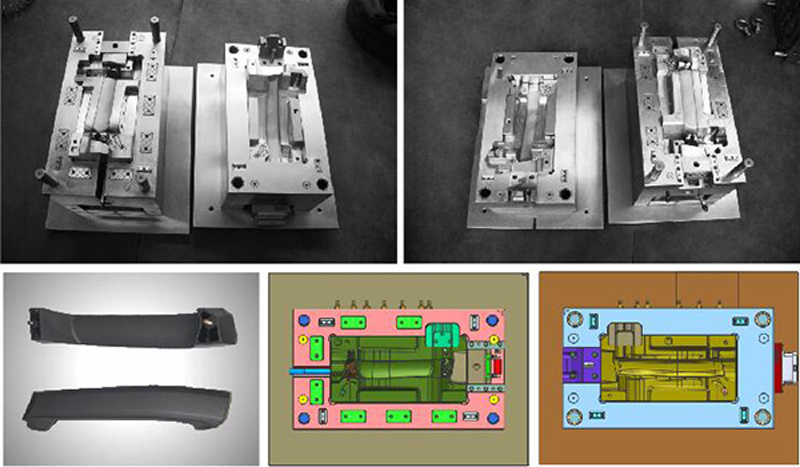
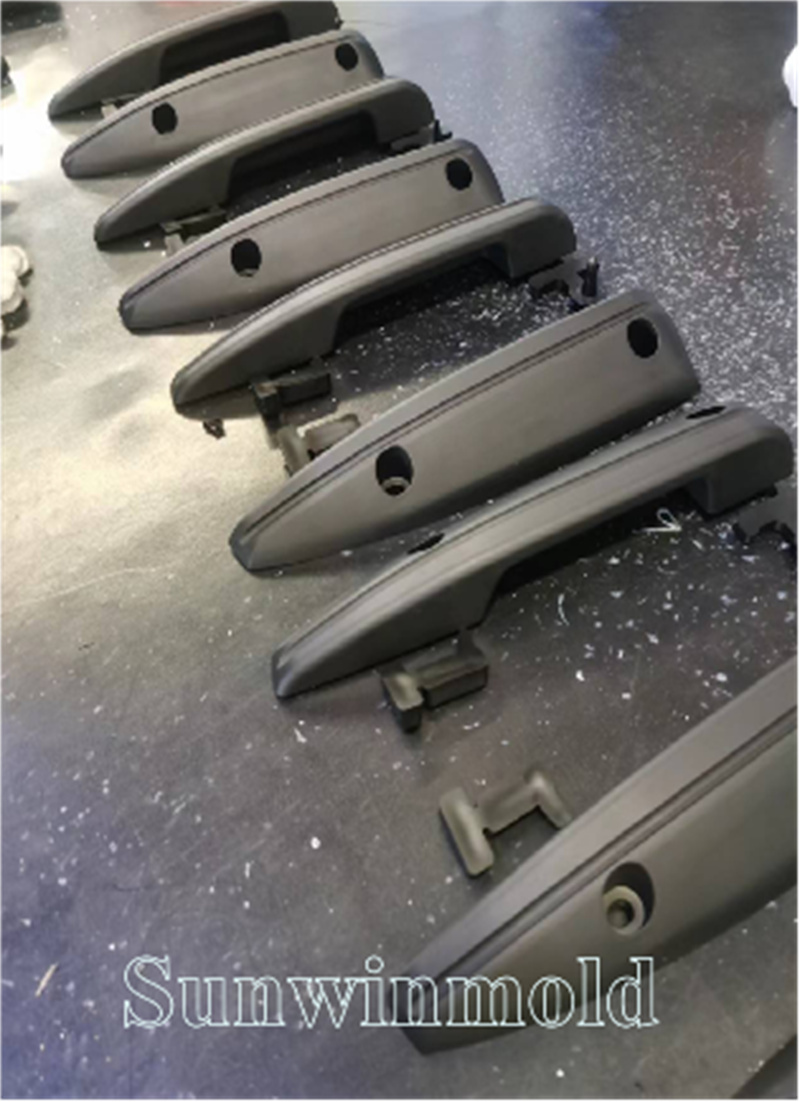