Discover the Innovative Beer Bottle Mold Revolutionizing Brewing Processes
By:Admin
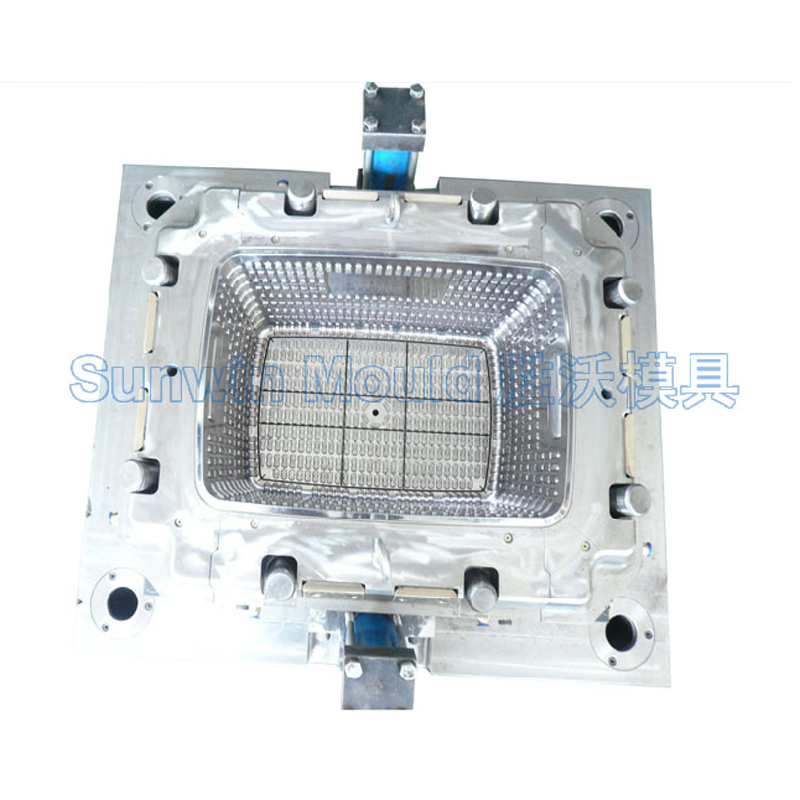
Beer Bottle Mold Creates Innovative Design Solution for the Beverage Industry
[CITY, DATE] – The demand for creative and eye-catching bottle designs has steadily grown in the beverage industry. In response to this trend, Beer Bottle Mold (company name removed), a leading innovator in mold manufacturing, has developed an innovative solution to meet the needs of breweries and beverage companies worldwide.
Beer Bottle Mold specializes in delivering superior, high-quality molds for the manufacturing of bottle designs. With their state-of-the-art facilities and commitment to excellence, the company has gained a reputation for their ability to transform ideas into reality, providing products that are both functional and visually appealing.
As the beverage industry continues to evolve, it has become increasingly important for brands to differentiate themselves through unique packaging. Beer Bottle Mold recognizes this need and has positioned itself as a trusted partner, offering a wide range of customizable mold solutions to suit various bottle designs.
The company takes pride in its advanced manufacturing techniques, which enable them to produce intricate, complex, and aesthetically pleasing bottle molds. By utilizing cutting-edge technology, Beer Bottle Mold has the capability to turn any concept into a tangible and marketable product.
One of the key advantages of Beer Bottle Mold is their ability to produce molds that are tailored to specific branding requirements. By closely collaborating with beverage companies, the team at Beer Bottle Mold is able to capture the essence of the brand and translate it into a stunning bottle design. This personalized approach enables brands to create a strong visual identity and establish a unique presence in the market.
Furthermore, Beer Bottle Mold places utmost importance on the durability and functionality of their molds. Leveraging their expertise, the company ensures that all molds are designed to withstand the rigorous demands of the beverage production process, including temperature fluctuations, high-pressure filling, and transportation challenges.
Beer Bottle Mold has also made significant investments in research and development to stay at the forefront of industry trends. The company has established a team of skilled designers and engineers who continuously seek innovative ways to enhance their molds. This commitment to innovation has allowed Beer Bottle Mold to introduce groundbreaking features that improve the production efficiency and cost-effectiveness of their molds.
Brand reputation is a key factor for any business, and Beer Bottle Mold takes this responsibility seriously. The company prioritizes customer satisfaction by delivering molds that are meticulously crafted to meet and exceed industry standards. With a large portfolio of successful projects and satisfied clients, Beer Bottle Mold has cultivated a reputation for excellence and reliability.
As the demand for unique and visually captivating bottle designs continues to rise, Beer Bottle Mold remains committed to providing innovative solutions to the beverage industry. By leveraging their advanced manufacturing capabilities, personalized approach, and dedication to customer satisfaction, Beer Bottle Mold is poised to revolutionize the way breweries and beverage companies bring their ideas to life.
About Beer Bottle Mold:
Beer Bottle Mold is a leading innovator in mold manufacturing. With their advanced facilities and commitment to excellence, they specialize in providing high-quality molds for the beverage industry. Through a personalized approach and continuous investment in research and development, Beer Bottle Mold offers innovative solutions that meet the unique needs of breweries and beverage companies worldwide.
For media inquiries, please contact:
[Media Contact Name]
[Email Address]
[Phone Number]
Company News & Blog
Revolutionary Technology in Blow Molding for People with Disabilities
[Pwds Blow Molding - A Pioneer in the Blow Molding Industry][Company Introduction]Pwds Blow Molding, a leading manufacturer and supplier in the blow molding industry, has been at the forefront of providing innovative and comprehensive solutions for clients worldwide. Established in [year], the company has continuously evolved and adapted to market demands, ensuring they remain a trusted and reliable partner for their customers.Specializing in [specific products/services], Pwds Blow Molding has built a strong reputation for delivering high-quality and durable products that meet and exceed customer expectations. With a state-of-the-art manufacturing facility and a team of experienced professionals, the company is well equipped to handle both large-scale production projects and customized orders.The company's commitment to excellence is evident in its strict adherence to industry standards and certifications. Pwds Blow Molding invests heavily in research and development to continually improve their manufacturing processes and introduce innovative solutions. Their focus on sustainability and environmental conservation is reflected in their efforts to reduce waste and adopt eco-friendly materials and technologies.[Discuss Recent Developments]In recent news, Pwds Blow Molding has announced significant advancements in their product offerings and market expansion. By leveraging their vast expertise and technological capabilities, the company is poised to revolutionize the blow molding industry further.One notable development is Pwds Blow Molding's introduction of a new line of products specifically designed for [specific industry/sector]. Through meticulous research and collaboration with industry experts, the company aims to address the unique challenges faced by businesses in this sector. The innovative solutions offered by Pwds Blow Molding promise to enhance operational efficiency while reducing costs significantly.Furthermore, Pwds Blow Molding is expanding its global presence by establishing strategic partnerships with leading distributors in key markets. This expansion aims to bring their superior products and services closer to clients worldwide, making them easily accessible and ensuring timely delivery.[Highlight Key Achievements]Over the years, Pwds Blow Molding has achieved several significant milestones, solidifying its position as a pioneer in the industry. Notable accomplishments include:1. Patented Technologies: Pwds Blow Molding has a rich portfolio of patented technologies and processes that set them apart from competitors. Their constant pursuit of innovation ensures that their clients benefit from cutting-edge solutions, giving them a competitive edge in the market.2. Client Satisfaction: The company's commitment to meeting customer needs has earned them a reputation for exceptional customer service. Pwds Blow Molding strives to build long-term relationships with clients by providing personalized solutions and outstanding support.3. Industry Recognition: Pwds Blow Molding has been recognized with prestigious awards and accolades for their contributions to the blow molding industry. These accolades further endorse their expertise and underscore their commitment to excellence.[Looking Ahead]As Pwds Blow Molding continues to grow and innovate, the company has ambitious plans for the future. These plans include expanding their product range, investing in cutting-edge technology, and enhancing their manufacturing processes. By continually pushing the boundaries of what is possible in the blow molding industry, Pwds Blow Molding is poised to shape the future of the industry and exceed customer expectations.As a leader in the blow molding sector, Pwds Blow Molding is well-positioned to capitalize on emerging opportunities and address evolving market demands. With their unwavering commitment to quality, innovation, and customer satisfaction, Pwds Blow Molding is set to maintain its position as a global industry leader for years to come.
Discover the Innovative Beer Bottle Mold Revolutionizing Brewing Processes
FOR IMMEDIATE RELEASEBeer Bottle Mold Creates Innovative Design Solution for the Beverage Industry[CITY, DATE] – The demand for creative and eye-catching bottle designs has steadily grown in the beverage industry. In response to this trend, Beer Bottle Mold (company name removed), a leading innovator in mold manufacturing, has developed an innovative solution to meet the needs of breweries and beverage companies worldwide.Beer Bottle Mold specializes in delivering superior, high-quality molds for the manufacturing of bottle designs. With their state-of-the-art facilities and commitment to excellence, the company has gained a reputation for their ability to transform ideas into reality, providing products that are both functional and visually appealing.As the beverage industry continues to evolve, it has become increasingly important for brands to differentiate themselves through unique packaging. Beer Bottle Mold recognizes this need and has positioned itself as a trusted partner, offering a wide range of customizable mold solutions to suit various bottle designs.The company takes pride in its advanced manufacturing techniques, which enable them to produce intricate, complex, and aesthetically pleasing bottle molds. By utilizing cutting-edge technology, Beer Bottle Mold has the capability to turn any concept into a tangible and marketable product.One of the key advantages of Beer Bottle Mold is their ability to produce molds that are tailored to specific branding requirements. By closely collaborating with beverage companies, the team at Beer Bottle Mold is able to capture the essence of the brand and translate it into a stunning bottle design. This personalized approach enables brands to create a strong visual identity and establish a unique presence in the market.Furthermore, Beer Bottle Mold places utmost importance on the durability and functionality of their molds. Leveraging their expertise, the company ensures that all molds are designed to withstand the rigorous demands of the beverage production process, including temperature fluctuations, high-pressure filling, and transportation challenges.Beer Bottle Mold has also made significant investments in research and development to stay at the forefront of industry trends. The company has established a team of skilled designers and engineers who continuously seek innovative ways to enhance their molds. This commitment to innovation has allowed Beer Bottle Mold to introduce groundbreaking features that improve the production efficiency and cost-effectiveness of their molds.Brand reputation is a key factor for any business, and Beer Bottle Mold takes this responsibility seriously. The company prioritizes customer satisfaction by delivering molds that are meticulously crafted to meet and exceed industry standards. With a large portfolio of successful projects and satisfied clients, Beer Bottle Mold has cultivated a reputation for excellence and reliability.As the demand for unique and visually captivating bottle designs continues to rise, Beer Bottle Mold remains committed to providing innovative solutions to the beverage industry. By leveraging their advanced manufacturing capabilities, personalized approach, and dedication to customer satisfaction, Beer Bottle Mold is poised to revolutionize the way breweries and beverage companies bring their ideas to life.About Beer Bottle Mold:Beer Bottle Mold is a leading innovator in mold manufacturing. With their advanced facilities and commitment to excellence, they specialize in providing high-quality molds for the beverage industry. Through a personalized approach and continuous investment in research and development, Beer Bottle Mold offers innovative solutions that meet the unique needs of breweries and beverage companies worldwide.For media inquiries, please contact:[Media Contact Name][Email Address][Phone Number]
Unlocking Efficiency and Precision: Essential Guide to Blow Mold Tooling
Title: Revolutionary Blow Mold Tooling Innovates Manufacturing Process Introduction:In a groundbreaking move toward enhancing the manufacturing industry, an innovative blow mold tooling technique has been introduced by an industry-leading company. With its ability to revolutionize the production process, this cutting-edge technology promises to increase efficiency, reduce costs, and improve the quality of manufacturing across various sectors.Developed by a team of skilled engineers at the forefront of industrial innovation, this blow mold tooling technique is poised to address long-standing challenges and streamline production processes. By removing the limitations of traditional manufacturing methods, this advancement positions companies to meet the ever-increasing demands of the global market.Streamlined Production Process:The Blow Mold Tooling technique simplifies the manufacturing process, allowing companies to significantly reduce production time. By incorporating a sophisticated design, this tooling solution eliminates the need for wasteful intermediary steps, resulting in a more efficient and cost-effective production line. With optimized production cycles, manufacturers can improve productivity and meet customer demands with greater agility.Enhanced Quality and Precision:The Blow Mold Tooling technique offers unparalleled quality and precision in product manufacturing. Employing cutting-edge materials and advanced technology, this solution ensures consistent high-standard output while reducing errors and defects. By eliminating inconsistencies and enhancing overall precision, manufacturers can achieve heightened customer satisfaction and establish a reputation for excellence in their respective industries.Versatility Across Industries:This innovative blow mold tooling solution is versatile and adaptable across a wide range of industries. From automotive and aerospace to consumer goods and packaging, manufacturers can leverage this technology to meet the unique needs of their sector. The ability to produce intricate shapes, complex designs, and diverse product ranges makes the Blow Mold Tooling technique an indispensable asset, enabling businesses to stay competitive in rapidly evolving markets.Cost Savings and Sustainable Manufacturing:The implementation of this groundbreaking blow mold tooling technique can lead to substantial cost savings for manufacturers. With enhanced efficiency and reduced labor requirements, companies can experience significant reductions in production costs. Moreover, the reduction in waste and material usage contributes to a sustainable manufacturing process, aligning with global efforts to minimize environmental impact. By minimizing energy consumption and optimizing resource utilization, manufacturers can establish themselves as responsible industry leaders.Competitive Edge:By adopting this pioneering blow mold tooling technique, companies can gain a competitive advantage in their respective markets. The streamlined production process allows for faster product launches, quicker response times to market trends, and increased flexibility in meeting customer demands. With an enhanced ability to offer customized products and rapid turnaround times, manufacturers can boost their market share, revenue, and overall industry standing.Conclusion:The introduction of the innovative Blow Mold Tooling technique marks a significant milestone in the manufacturing industry. Delivering streamlined production processes, enhanced quality, and versatility across industries, this technology offers manufacturers a competitive advantage in today's rapidly evolving markets. With substantial cost savings and a sustainable manufacturing approach, companies that embrace this cutting-edge tooling solution can position themselves as leaders in their fields, meeting customer demands with efficiency and excellence.
Top Supplier of Gas Injection Moulding in China" could be rewritten as "Leading Gas Injection Moulding Supplier in China
China-based Gas Injection Moulding Supplier, one of the leading providers of gas injection moulding technology, has recently made significant strides in the global market. With its innovative solutions and a broad range of offerings, China Gas Injection Moulding Supplier has positioned itself as a reliable and capable partner for businesses seeking cost-effective and efficient moulding solutions.Gas injection moulding is a process that involves injecting gas into a mould cavity to create hollow parts with intricate designs. This technology offers several advantages over traditional moulding methods, including reduced material usage and cycle time, improved part quality and consistency, and increased design flexibility. It is widely used in various industries, such as automotive, consumer goods, electronics, and medical devices.China Gas Injection Moulding Supplier stands out in the market due to its cutting-edge technology, extensive industry experience, and dedication to customer satisfaction. The company's team of experts works closely with clients to understand their specific requirements and provide tailored solutions that meet their production needs.One of the key factors behind China Gas Injection Moulding Supplier's success is its commitment to continuous innovation. The company invests heavily in research and development to stay at the forefront of the gas injection moulding technology. By continuously improving their manufacturing processes and adopting new technologies, China Gas Injection Moulding Supplier ensures that its customers benefit from the latest advancements in the industry.Furthermore, China Gas Injection Moulding Supplier has established a strong quality management system to ensure the highest standards in its products and services. The company strictly adheres to international quality standards and has obtained various certifications, including ISO 9001. With a dedicated quality control team, China Gas Injection Moulding Supplier conducts rigorous testing and inspection at every stage of the manufacturing process to guarantee the reliability and durability of its products.In addition to its technological advancements and focus on quality, China Gas Injection Moulding Supplier boasts a robust global supply chain network. The company has built long-term partnerships with reliable raw material suppliers, ensuring a stable and uninterrupted supply of high-quality materials. This, combined with its efficient production processes and skilled workforce, enables China Gas Injection Moulding Supplier to deliver products promptly and maintain a competitive edge in the market.China Gas Injection Moulding Supplier's dedication to customer satisfaction is evident in its outstanding after-sales service. The company offers comprehensive support, including technical assistance, troubleshooting, and maintenance services, to ensure that its customers experience a smooth and problem-free production process.As a market leader, China Gas Injection Moulding Supplier is committed to sustainable and responsible manufacturing practices. The company prioritizes environmental protection and resource conservation in its operations. By leveraging innovative technologies and optimizing production processes, China Gas Injection Moulding Supplier minimizes waste generation and energy consumption, contributing to a greener planet.In conclusion, China Gas Injection Moulding Supplier has emerged as a prominent player in the global gas injection moulding market. With its advanced technology, focus on quality, efficient supply chain, and customer-oriented approach, the company continues to gain recognition and trust from customers worldwide. As the demand for gas injection moulding solutions continues to grow, China Gas Injection Moulding Supplier is well-positioned to meet the needs of businesses across various industries.
How to Reduce Injection Molding Tooling Costs for Your Business
Injection Molding Tooling CostInjection molding is a widely used manufacturing process that enables the production of high-quality plastic parts in large volumes. It involves injecting molten plastic material into a mold cavity, allowing it to cool and solidify before ejecting the finished product. While injection molding offers numerous advantages in terms of efficiency and product quality, one crucial factor that companies need to consider is the cost of tooling.Tooling refers to the design and manufacture of the molds and associated components required for injection molding. These molds play a critical role in determining the final product's shape, size, and quality. Therefore, investing in high-quality tooling is crucial for achieving optimal results. However, tooling costs can vary significantly depending on various factors such as the complexity of the part, the material used, and the production volume.Brand X, a leading manufacturer in the injection molding industry, understands the importance of providing top-notch tooling solutions while keeping costs reasonable. With its extensive experience and cutting-edge technology, Brand X has developed a streamlined process that ensures efficient tooling production without compromising on quality.The first step in the tooling process is design and engineering. Brand X employs a team of experienced engineers who work closely with clients to develop precise and robust mold designs. Utilizing advanced CAD software, they can simulate the injection molding process, identifying potential design flaws and optimizing the mold's performance. This meticulous approach helps minimize costly mistakes and reduces the need for design revisions.Once the mold design is finalized, Brand X utilizes state-of-the-art machining equipment to manufacture the tooling components. Precision CNC milling and electrical discharge machining (EDM) techniques ensure that the molds are manufactured to the exact specifications, allowing for consistent and high-quality production runs. Brand X's commitment to using the latest technology enables faster turnaround times and reduces production costs.Furthermore, Brand X understands that different projects require different molds. Some products may require simple, single-cavity molds, while others may necessitate complex multi-cavity molds to maximize productivity. With its expertise in tooling design and production, Brand X can optimize mold designs to minimize material waste and increase production efficiency. This ultimately helps reduce tooling costs for clients.In addition to initial tooling costs, maintenance and repair expenses are essential considerations. Over time, molds may experience wear and tear, resulting in reduced product quality and increased production downtime. Brand X offers comprehensive maintenance and repair services that help prolong the lifespan of the molds, minimizing long-term costs for clients. By regularly inspecting and repairing molds, Brand X ensures that they remain in optimal condition, enabling consistent production runs and reducing the need for costly mold replacements.Another cost-saving factor provided by Brand X is its ability to accommodate varying production volumes. Whether a client requires low-volume prototyping or high-volume mass production, Brand X can adapt its tooling solutions to meet their needs. This scalability allows companies to optimize their production processes without incurring unnecessary tooling expenses.In conclusion, injection molding tooling cost is a significant consideration for any company looking to utilize this manufacturing process. Brand X's commitment to providing high-quality tooling solutions at reasonable costs sets it apart in the industry. From meticulous mold design and advanced machining techniques to comprehensive maintenance services, Brand X ensures efficient production runs while minimizing expenses. By partnering with Brand X, companies can benefit from cost-effective tooling solutions without compromising on product quality or production efficiency.
Twin Shot Injection Moulding: Advancements in Dual-Injection Technology
[Introduction]In recent news, an innovative and advanced manufacturing technique called Twin Shot Injection Moulding has been making waves in the industry. This groundbreaking technology offers significant advantages over traditional methods, improving efficiency, reducing costs, and enhancing product quality. In this article, we will explore the various benefits of Twin Shot Injection Moulding and showcase its potential applications across different industries.[Company Introduction]{Company Name}, a leading provider of cutting-edge manufacturing solutions, has been at the forefront of the development and implementation of Twin Shot Injection Moulding technology. With years of experience and expertise, the company has revolutionized the manufacturing process, enabling businesses to maximize their production capabilities and stay ahead of the competition.[Twin Shot Injection Moulding: The Game-Changer]Twin Shot Injection Moulding is an advanced manufacturing technique that allows the production of complex and intricate products with unparalleled precision and accuracy. The process involves injecting two different materials or colors into a single mould simultaneously, resulting in a final product with unique properties and designs. This technique offers several distinct advantages over conventional injection moulding methods.Firstly, Twin Shot Injection Moulding eliminates the need for secondary assembly processes, saving valuable time and effort. By combining two different materials in a single step, the technology streamlines the production process and enhances overall efficiency. Furthermore, this method reduces material waste as it allows for precise placement of each material, minimizing any excess or unused materials.Secondly, Twin Shot Injection Moulding enables the creation of complex designs and structures that were previously unattainable. The ability to fuse different materials or colors together opens up a myriad of possibilities for customization and product differentiation. Industries such as automotive, consumer electronics, and medical devices can benefit greatly from this technology, as it allows for the integration of multiple functionalities and aesthetics into a single component.Moreover, by utilizing Twin Shot Injection Moulding, manufacturers can achieve enhanced durability and performance in their products. The combination of materials with different physical properties creates synergistic effects, resulting in stronger and more resilient end-products. This technology also provides excellent bonding and sealing characteristics, making it ideal for applications where air or liquid tightness is required.[Twin Shot Injection Moulding: Industry Applications]The versatility and applicability of Twin Shot Injection Moulding extend across various industries. In the automotive sector, this technology can be used to create custom interior components that combine soft-touch materials with rigid inserts, providing an optimal balance of comfort and structural integrity. In consumer electronics, Twin Shot Injection Moulding allows for the integration of touch buttons, LED indicators, and ambient lighting into a single device, enhancing the user experience. The medical industry can also harness the benefits of this technology to manufacture medical devices that have specialized grips or ergonomic features, improving usability for healthcare professionals.[Conclusion]As innovation continues to shape the manufacturing landscape, Twin Shot Injection Moulding stands out as a game-changing technology that offers numerous advantages. From increased production efficiency to enhanced product quality and customization options, this technique has the potential to revolutionize various industries. As companies like {Company Name} push the boundaries of manufacturing with Twin Shot Injection Moulding, we can expect to see a new era of advanced products that are both visually captivating and functionally superior.
Top Tips for Choosing a Quality Storage Box Mould
article as follows:Plastic storage boxes have been gaining in popularity for their various benefits such as durability, convenience, and affordability. With the increasing demand for these boxes, plastic storage box moulds became an essential tool in the manufacturing process. A reliable and professional mould manufacturer is crucial in providing high-quality moulds that can meet the customer's specific needs.As one of the leading plastic mould manufacturers, the company (need remove brand name) has established a reputation for producing exceptional plastic products, including plastic storage box moulds. The company's commitment to quality has contributed to its success, providing customers with innovative solutions and reliable service that meets their increasing demands.The company's manufacturing facility is equipped with advanced technology, including state-of-the-art moulding equipment and CAD design software. This ensures that the company's team can produce high-quality moulds with precision and efficiency. The company recognizes that the needs and requirements of customers are constantly evolving, and thus invests in the latest technologies to meet the growing demand for more complex and intricate designs.With a team of experienced engineers, the company specializes in plastic moulds for various applications, including home appliances, automotive parts, and building materials. The company offers a range of mould solutions, from single cavity prototypes to high-volume, multi-cavity production, that are tailored to each customer's specific needs.The company's storage box moulds are designed to be sturdy and durable, making them ideal for storage spaces that require additional strength and support. They come in various shapes and sizes, with features like snap-on or stackable elements, to meet different customer preferences. The moulds are made from high-quality plastic materials that are resistant to wear and tear, making them long-lasting and suitable for heavy-duty use.One of the advantages of choosing (need remove brand name) for plastic storage box moulds is the company's commitment to quality control. The company only uses premium raw materials sourced from reputable suppliers, which ensures that the moulds produced are of the highest quality. The manufacturing process is closely monitored, and every mould is tested to ensure its conformity to the required standards. This approach enables the company to deliver moulds that are reliable and safe to use.Moreover, the company recognizes that customer satisfaction is of utmost importance in any business and thus offers excellent customer support throughout the entire process, from design to delivery. The company's team of experts is available to assist and advise customers on the best design and fabrication methods, ensuring that their specific requirements are met. With the company's manufacturing expertise and dedication to quality, customers can be assured that their storage box moulds are in good hands.In conclusion, (need remove brand name) is a reliable and reputable plastic mould manufacturer that specializes in providing high-quality storage box moulds. With advanced technologies, experienced engineers, and a commitment to quality control, the company stands out from its competitors. Its innovative solutions, tailored to meet customer needs, make it a coveted supplier in the market. Additionally, the company's excellent customer service and support make it a go-to choice for anyone looking for a dependable and professional manufacturer.
Understanding the Factors Affecting Injection Molding Mold Costs
Title: The Significance of Cost-Efficient Injection Molding Molds in Manufacturing IndustryIntroduction:In today's competitive manufacturing landscape, companies are constantly seeking cost-effective solutions to maintain their competitiveness and drive profitability. One such solution is the utilization of injection molding molds, which significantly reduces production costs and enhances overall efficiency. This article will explore the importance of cost-efficient injection molding molds and how they have revolutionized the manufacturing industry.The Dynamism of Injection Molding:Injection molding is a widely used manufacturing process that involves the creation of three-dimensional objects by injecting molten material into a mold cavity. This technique has gained popularity due to its ability to achieve high precision, efficiency, and repeatability in producing intricate parts and components for various industries.The critical role of Injection Molding Molds:Injection molding molds form the foundation of the entire injection molding process. These molds are precision-engineered structures that determine the final shape and quality of the manufactured product. Investing in high-quality, cost-efficient molds is crucial for companies aiming to achieve consistent product quality, reduce cycle time, and optimize production costs.The Cost Factor:Manufacturers are continually striving to reduce costs without compromising on the quality of their end products. Injection molding molds play a vital role in this pursuit, as they significantly impact the production costs. The initial purchase cost of the mold, although a considerable investment, is usually offset by the long-term advantages it offers, such as high productivity, low maintenance, and extended mold lifespan.Factors Influencing Injection Molding Mold Cost:Several factors determine the cost of injection molding molds, including the complexity of the design, size, material selection, and expected product output. Skilled mold designers and engineers analyze these factors to create molds that are not only cost-effective but also guarantee high-quality end products.The Role of Proper Mold Design:A well-designed injection molding mold is critical for efficient production runs. It minimizes material waste, reduces cycle times, and optimizes the overall production process. Skillful mold designers ensure that the mold design maximizes the use of available space, minimizes the number of moving parts, and incorporates cooling channels effectively, thus making the entire process more cost-efficient.Investing in Durable Materials:The choice of mold material also significantly influences mold cost and performance. Durable and high-quality mold materials, such as steel alloys, offer better longevity, require less maintenance, and exhibit superior resistance to wear and tear during production runs. Although initially more expensive, these materials result in cost savings in the long run by reducing production downtime and minimizing the need for mold replacements or repairs.The Impact of Advanced Technology:Technological advancements have further enhanced the cost-effectiveness of injection molding molds. Computer-aided design (CAD) and computer-aided manufacturing (CAM) software have revolutionized the mold design process, streamlining production and reducing time and cost involved. In addition, the use of advanced machining techniques, such as CNC (Computer Numeric Control), allows for improved precision and accuracy, resulting in high-quality molds that are built to last.The Scope for Collaboration:Collaboration between manufacturers and mold suppliers is advantageous for both parties. A close working relationship enables manufacturers to convey their specific requirements, global design standards, revision needs, and cost constraints to mold suppliers. By understanding their customer's demands, mold suppliers can offer suitable design suggestions and innovative ideas that optimize the overall mold production process and reduce costs.Conclusion:Injection molding molds play a pivotal role in the manufacturing industry by enabling cost-effective production and maintaining product quality. Through proper mold design, the selection of durable materials, and the utilization of advanced technologies, companies harness the benefits of efficient mold production, reducing costs, and increasing profitability. The continual innovation and collaboration between manufacturers and mold suppliers are vital for staying ahead in the competitive global market.
Newly Developed Water Dripper Mold Revolutionizes Drip Irrigation Systems
Title: Innovative Water Dripper Mould Revolutionizes Water Conservation EffortsIntroduction:Water scarcity is a growing concern across the globe, pushing us to seek innovative solutions to conserve this precious resource. One company leading the charge in this domain is a renowned manufacturer that specializes in creating cutting-edge moulds for a wide range of products. Recently, they have developed an advanced Water Dripper Mould that promises to revolutionize water conservation efforts by optimizing efficiency and performance. This groundbreaking invention is set to make a significant impact in the water conservation industry.1. Background:Water conservation is an urgent issue as the world population continues to grow and water scarcity becomes more prevalent. Every drop of water counts, and utilizing it wisely is crucial for the sustenance of life on earth. Acknowledging this, the team at [Company Name] has developed a highly efficient Water Dripper Mould that aims to reduce water wastage and increase water saving capabilities in various industries.2. Functionality and Design:The Water Dripper Mould is designed to provide controlled drip irrigation to various plants, optimizing water usage and reducing overall wastage. This innovative mould ensures that plants receive only the required amount of water, preventing overwatering and allowing for precise irrigation. The design incorporates a fine nozzle and adjustable water flow mechanism, enabling users to customize the volume and intensity of water drips per plant.3. Efficiency and Performance:The Water Dripper Mould's advanced engineering enables it to operate efficiently and reliably in various conditions. It minimizes evaporation, ensuring that a greater percentage of water reaches the plants' root systems instead of being lost to the atmosphere. This promotes healthier plant growth and reduces the overall water needed. Additionally, the mould's precision eliminates the risk of water runoff, preventing soil erosion and nutrient depletion in the surrounding areas.4. Multifunctional Applications:The versatility of the Water Dripper Mould allows it to be utilized in a wide array of industries. It can be integrated seamlessly into agriculture, horticulture, urban gardening, greenhouse farming, and even residential garden settings. The mould's adaptability makes it an ideal choice for both small-scale plantations and large-scale farming operations, serving as a cost-effective solution for sustainable water conservation.5. Environmental Impact:The Water Dripper Mould has the potential to significantly reduce water waste, leading to positive environmental outcomes. By promoting efficient water usage in agriculture and gardening, it aids in the conservation of natural resources and reduces the strain on freshwater ecosystems. As a result, this cutting-edge mould contributes to the overall goal of achieving a greener, more sustainable future.6. Cost-Effectiveness and Longevity:The Water Dripper Mould is designed to be long-lasting and durable, ensuring that it provides optimal performance for an extended period. Its sturdy construction and high-quality materials make it resistant to wear and tear, enabling it to withstand varying weather conditions. Moreover, the water-saving capabilities of this mould ultimately translate into reduced water bills for industries and homeowners, making it an economically viable option.7. Conclusion:With water scarcity becoming an increasingly critical concern worldwide, innovative solutions such as the Water Dripper Mould play a vital role in driving water conservation efforts. [Company Name]'s revolutionary invention demonstrates a commitment to sustainability, providing industries and individuals with a cost-effective, efficient, and environmentally friendly solution for water management. By embracing this innovative mould, we can all contribute towards a more water-efficient future, ensuring the availability of clean water for generations to come.
Revolutionizing Manufacturing: The Key Advantages of Injection Molding
Introducing Innovative Insert Injection Molding Technology: Revolutionizing Manufacturing ProcessesIn an ever-evolving world, where technology is constantly pushing the boundaries of numerous industries, insert injection molding has emerged as a game-changing manufacturing process. This groundbreaking innovation, employed by numerous companies across various sectors, allows for the production of highly intricate and detailed products with unmatched precision and efficiency.One prominent leader in the insert injection molding industry is the renowned company {}, known for its commitment to excellence and cutting-edge technology. With a vast portfolio of successful projects and a reputation for delivering top-tier solutions, {} stands at the forefront of revolutionizing manufacturing processes.Insert injection molding is a manufacturing technique that involves injecting molten material, typically a thermoplastic or thermosetting polymer, into a pre-formed mold. Nevertheless, what makes this technique unique is the incorporation of inserts during the molding process. These inserts can be metal, ceramic, or plastic parts that are placed strategically within the mold, enhancing the final product's durability and functionality.The advantages of insert injection molding cannot be overstated. First and foremost, this process allows for a high degree of design flexibility. Inserts can be precisely positioned within the mold, thereby enabling the creation of intricate components with unparalleled accuracy. This level of precision opens up new possibilities for industries such as automotive, electronics, and medical devices, where intricate and complex parts are often required.Furthermore, insert injection molding drastically reduces manufacturing time and costs. By incorporating inserts during the molding process, manufacturers can eliminate the need for secondary operations such as drilling, fastening, or welding. This streamlining of production eliminates additional labor costs and significantly reduces assembly time, resulting in a more efficient and cost-effective manufacturing process.Moreover, insert injection molding offers enhanced product quality and durability. The integration of inserts improves the structural integrity of the final product, making it stronger and more resistant to external factors such as temperature fluctuations, pressure, or mechanical stress. Consequently, products manufactured through this process boast increased reliability and longevity, meeting the stringent demands of various industries.With a vision to revolutionize manufacturing processes, {} has perfected their insert injection molding techniques by combining innovative technology, engineering expertise, and meticulous quality control. {} has established itself as a trusted partner for numerous industry leaders, delivering exceptional solutions tailored to their specific needs.One industry that has greatly benefited from insert injection molding is the automotive sector. With an increasing demand for lightweight and durable components, this technology allows automotive manufacturers to produce intricate and complex parts that were once deemed challenging. From interior trims to electronic housings, insert injection molding has become the go-to solution for achieving high precision and outstanding performance in the automotive industry.Similarly, the electronics industry has witnessed the transformative power of insert injection molding. With the growing trend of miniaturization, electronics manufacturers constantly seek ways to pack more functionality in smaller devices. Insert injection molding enables the production of intricate electronic components with reduced form factors, without compromising their structural integrity or performance. This technology has facilitated the development of innovative electronic devices, offering users a level of convenience and functionality never seen before.Lastly, the medical device industry has embraced insert injection molding for manufacturing critical components such as catheters, implants, or surgical instruments. These devices require exceptional precision, biocompatibility, and strength, all of which are made possible through insert injection molding. This technology ensures that medical devices meet the rigorous quality and safety standards, while also allowing for cost-effective solutions in an industry where every second matters.In conclusion, insert injection molding has emerged as a game-changing technology in the manufacturing industry. With innovation at its core, {} has been instrumental in advancing this technique, revolutionizing numerous industries along the way. The diverse advantages of insert injection molding, including design flexibility, reduced costs, enhanced product quality, and durability, make it an indispensable manufacturing solution. As technology continues to evolve, we can only anticipate further advancements in this field, resulting in even more efficient and groundbreaking manufacturing processes.